Hydro Case Study – Renewing a Block-Style Guide Bearing
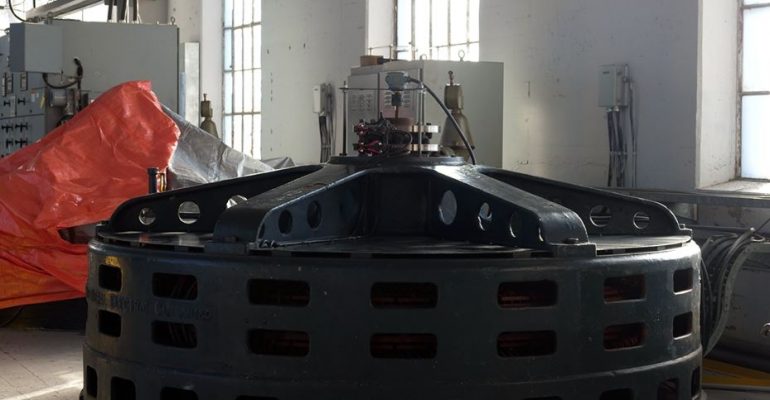
Hydro Case Study – Renewing a Block-Style Guide Bearing
THE CHALLENGE – Achieving Acceptable Wear Rates, Without Major Retrofits
In previous discussions with several Ontario-based customers, it was noted that a typical stave-type bearings in their stations are generally requiring adjustment every ~6 months to compensate for stave wear. At one specific site, the block-style bearings will be adjusted to achieve 0.004 to 0.006” diametric clearance, and then once the clearance reaches 0.012” the pads will be adjusted again to reset the clearance. It was also noted that it can take 1 week or more of downtime to make these adjustments (de-water the unit, lock it out, remove the packing gland, adjust the bearing, reassemble, unlock, re-water) so every time a unit is stopped for bearing block adjustments, this represents lost generation revenue potential. The oil bearing above the turbine bearing is also usually working with a fairly close clearance, so if the lower guide bearing clearance is too large, there is a risk of overloading the oil bearing above it – and wiping this oil/Babbitt bearing this would lead to much bigger problems!
Previous stave materials used at these older stations over the past decades included Dilecto, Micarta, Ryertex, lignum vitae (wood), and also Thordon SXL. All of the different block materials exhibit varying wear life depending on water flow rates & cleanliness, but the Thordon SXL elastomer has proven to be one of the longest lasting and most reliable options, often achieving a multi-year life with less frequent adjustments to maintain an acceptable clearance.
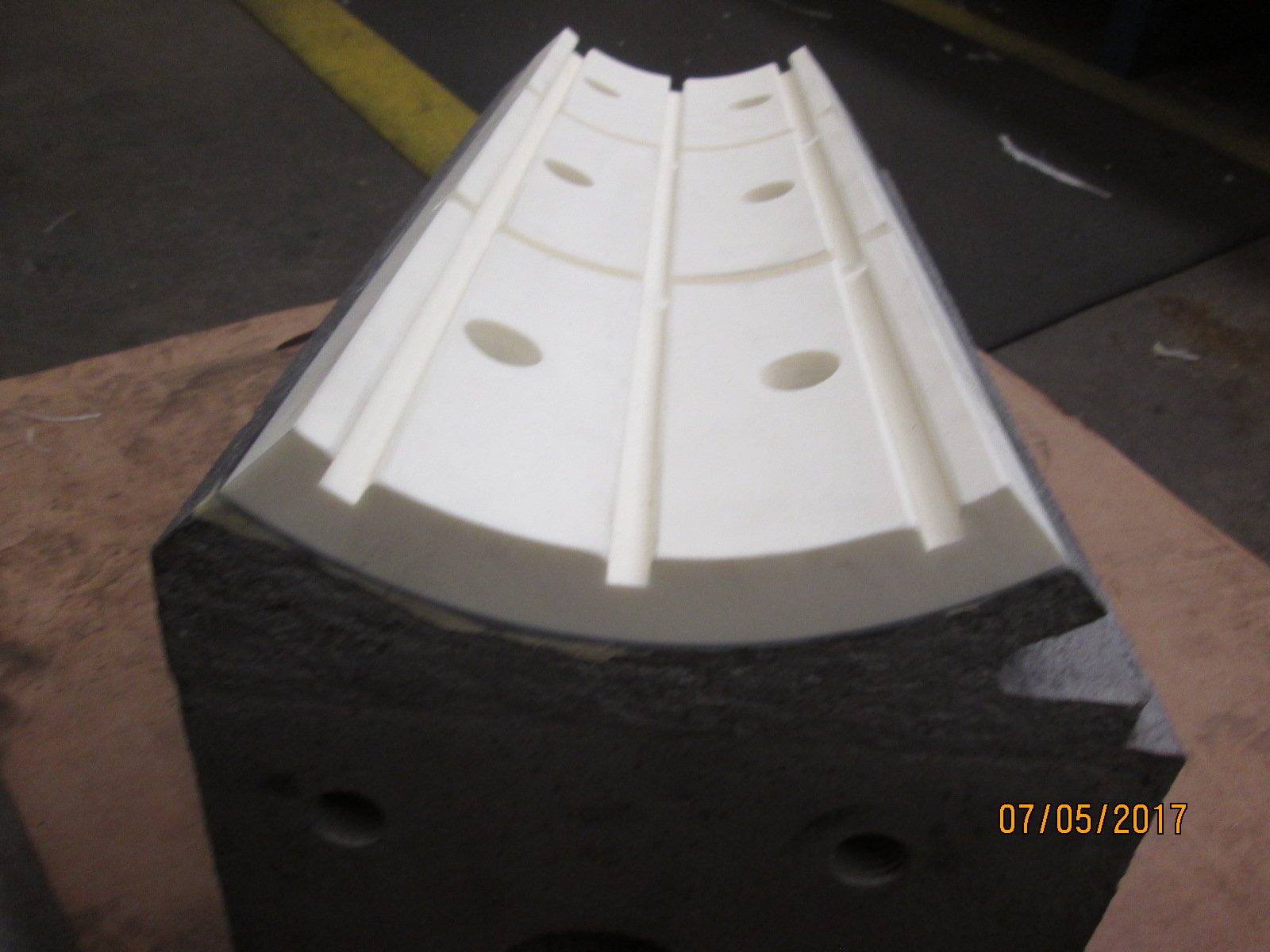
Block With Metal Backing
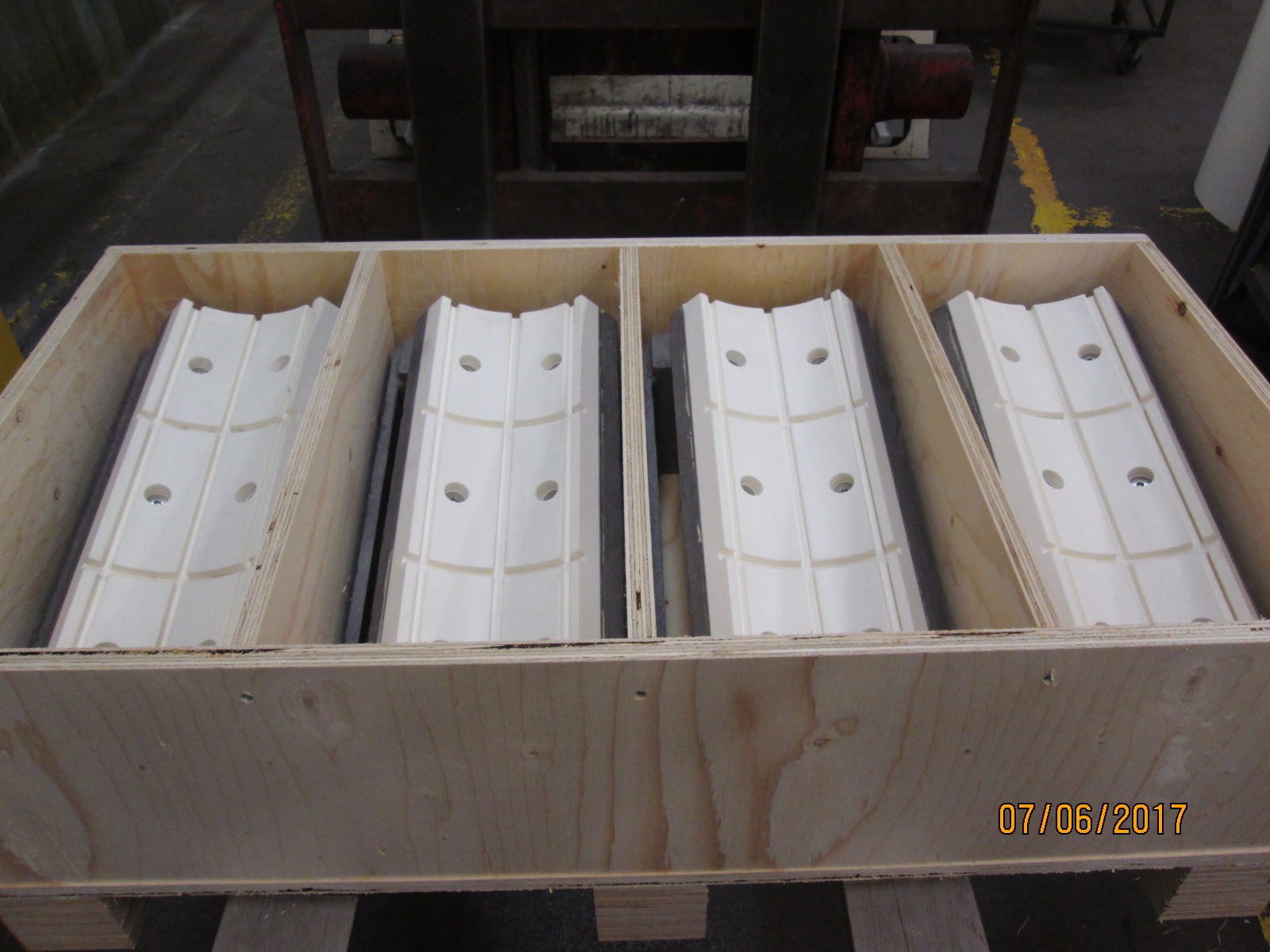
New Blocks Ready to Ship
THE SOLUTION – Upgrade with Thordon SXL!
These types of block-style turbine guide bearings are found in many older power stations around Ontario, Quebec, and the US Northeast, as these areas were historically some of the first regions with hydropower installed. Older water-driven grist mills and saw mills along smaller rivers were upgraded to the “new” and exciting technology of hydroelectric power, and in these early days the most accessible water-lubricated bearing material was often wooden blocks! A few examples where the block-style bearings are still in use around Ontario include Brewers Mills (vertical turbines, from 1939), Gananoque (horizontal unit, also 1939), Crystal Falls (vertical units, 1921), Big Eddy (vertical units, 1941), and all of these have had the Thordon SXL elastomer installed in the block or stave form.
Thordon SXL is made in Canada, with a proven track record in Hydro, Marine and Industrial applications for over 40 years. Thordon SXL offers a low coefficient of friction, superior adhesive wear performance and good resistance to wear resulting from third particle abrasion. The SXL elastomer offers minimal maintenance requirements and eliminates the need for frequent bearing adjustments.
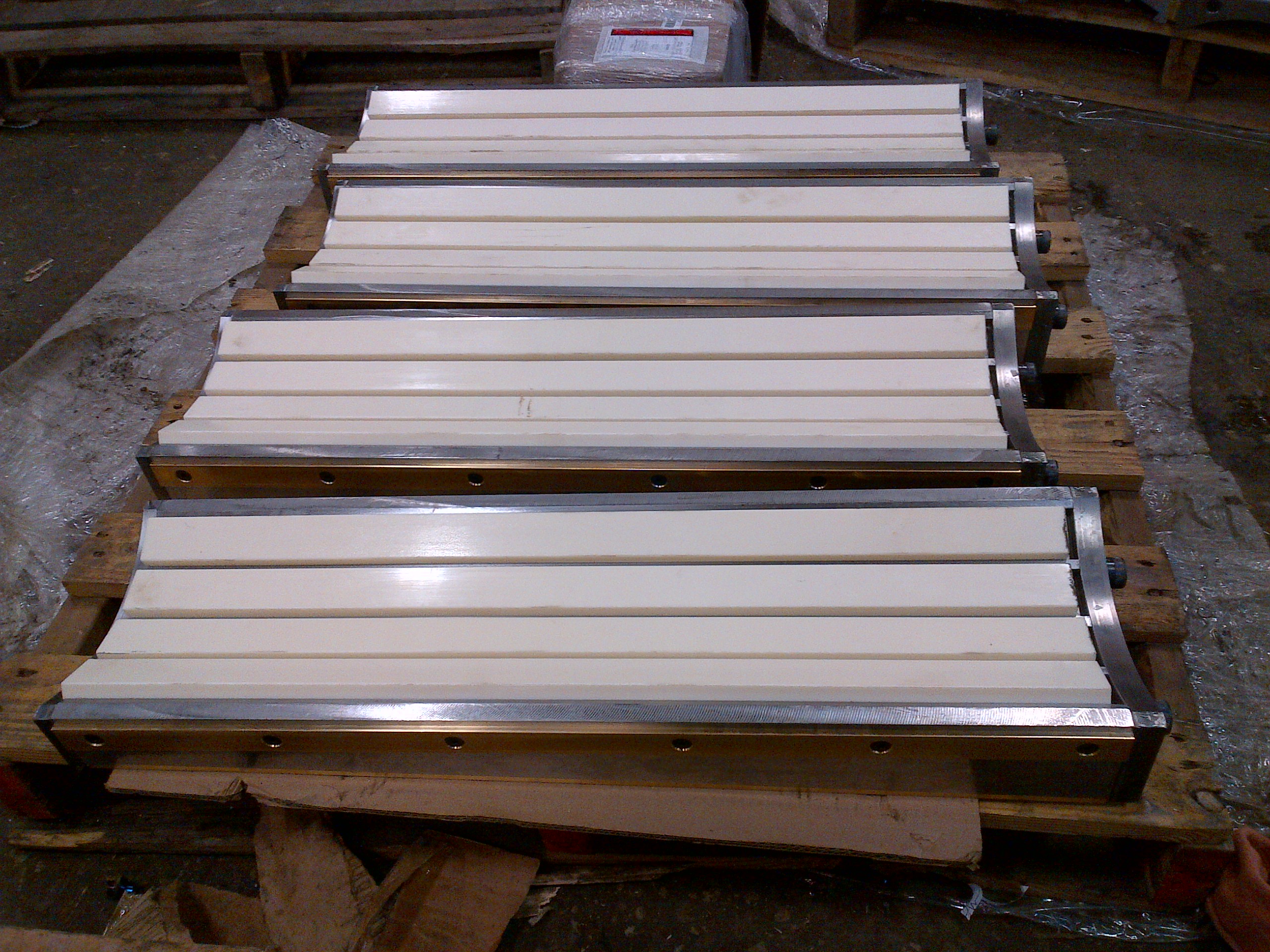
Custom Steel Blocks with Stave Pockets
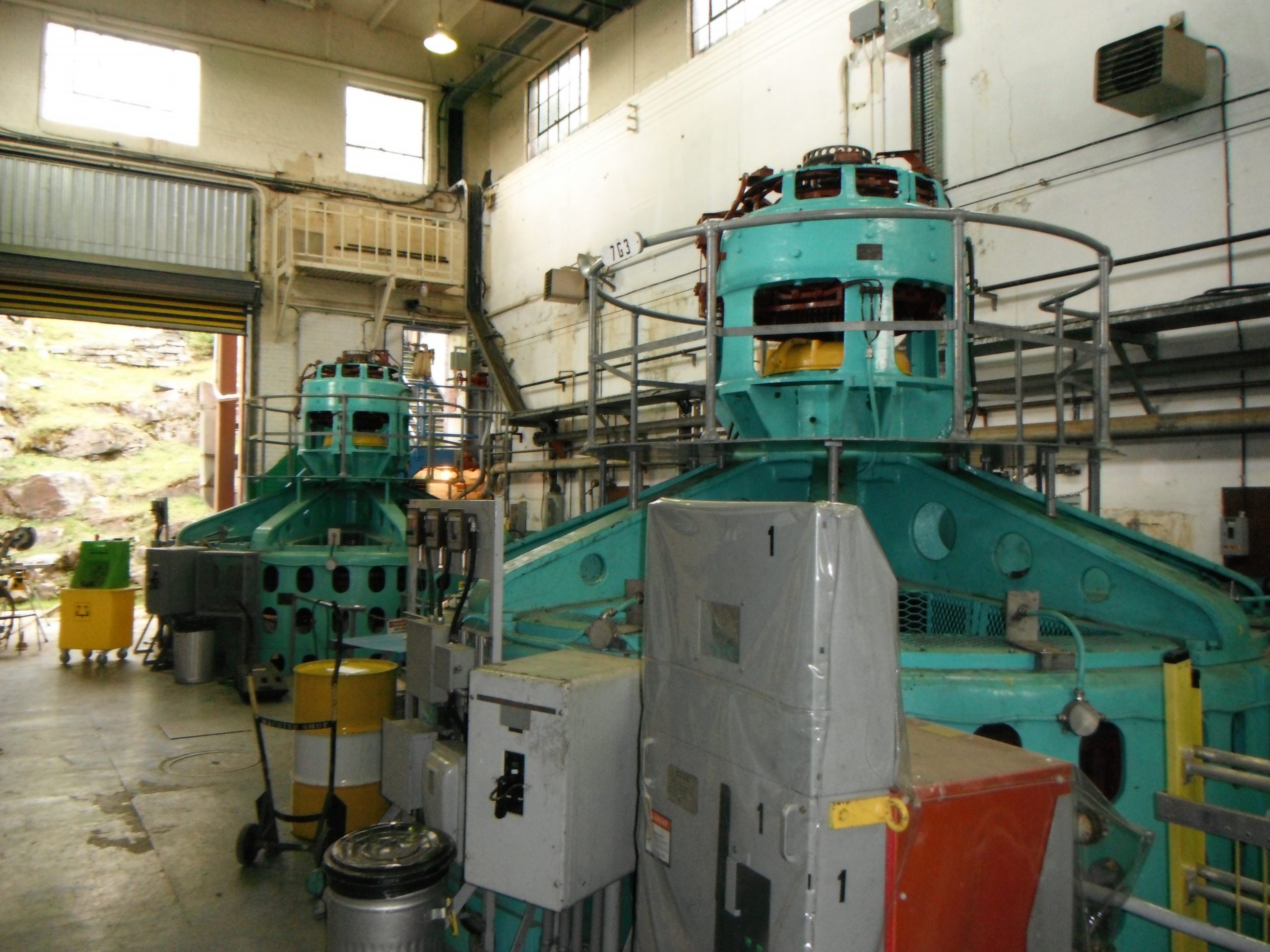
Historical Power Station
The performance of Thordon SXL in turbine guide bearing applications can be even further enhanced when installed in the full cylindrical form bearing by establishing a stable hydrodynamic water film that acts to separate the bearing and shaft surfaces and substantially reduces sliding wear in the bearing material. Find out more about this newer style of water-lubricated turbine guide bearing in a future post!
Do you have challenges with your bearings, shaft seals, or water filtration systems and need a creative, cost-effective solution? Allow Millstream Engineering’s team of specialists to lead your group to a successful, economical solution. Contact us today.