Putting Polymers to the Test: Ensuring the Reliability of Non-Metallic Self-Lubricating Bearings
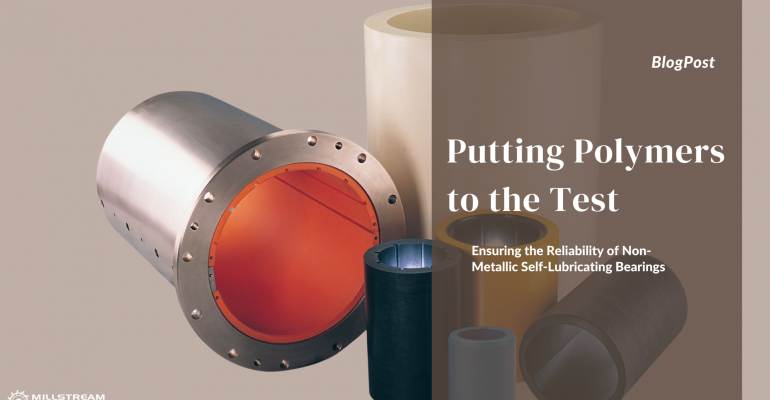
Putting Polymers to the Test: Ensuring the Reliability of Non-Metallic Self-Lubricating Bearings
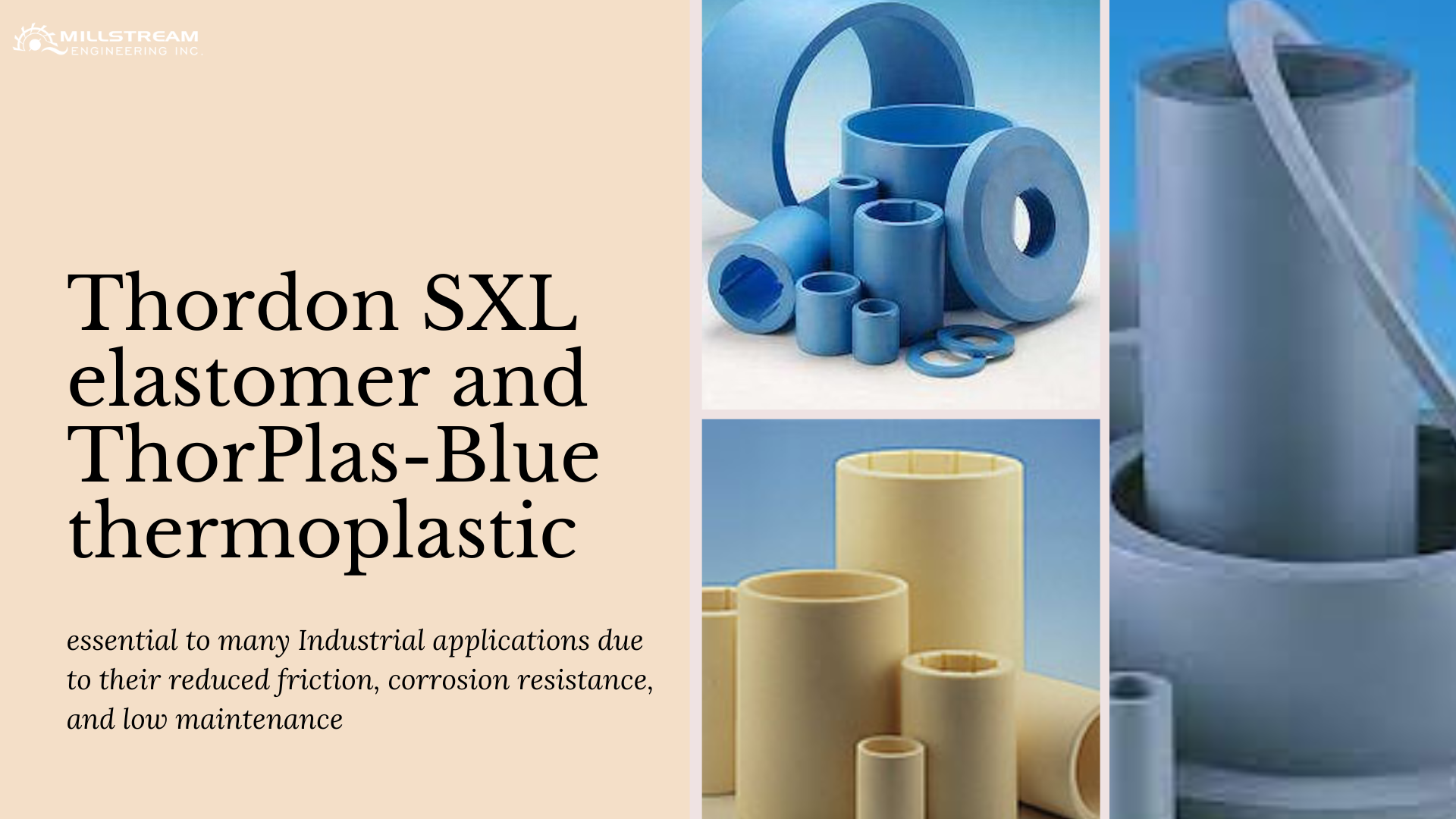
Mechanical Testing
Tensile Strength and Elongation Tests
Tensile strength tests measure a material's ability to withstand pulling forces until it breaks, providing insights into strength and ductility. High tensile strength and appropriate elongation rates are crucial for applications where bearings experience significant loads.
Compressive Strength Tests
Compressive strength tests assess a material's reaction under compression, common in bearing applications. These tests determine the load-bearing capacity, with materials needing high compressive strength to avoid deformation.
Impact Resistance Tests
Impact resistance tests evaluate durability against sudden forces, simulating real-world impacts. These tests measure the material's ability to absorb energy without fracturing, essential for dynamic or impact-prone applications.
Hardness Tests
Hardness tests measure resistance to surface indentation and wear. Common tests include Shore and Rockwell hardness tests, providing information on the material's ability to resist surface damage and wear over time.
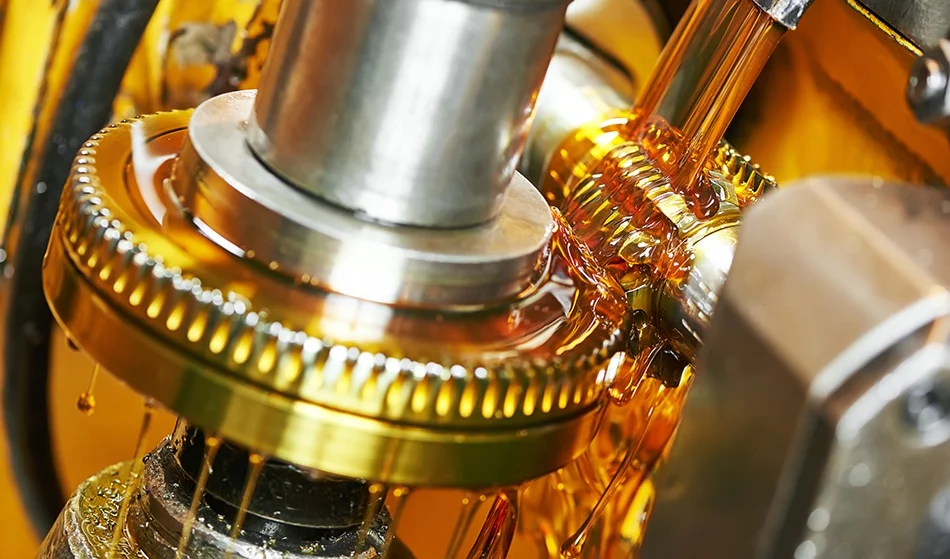
Tribological Testing
Friction & Wear Testing
Wear and friction tests are critical for evaluating the longevity and efficiency of self-lubricating bearings. These tests simulate contact and movement between surfaces to measure wear rate and coefficient of friction, indicating effective self-lubrication and longer service life.
Coefficient of Friction Measurements
The coefficient of friction (COF) measures resistance to sliding between surfaces. Lower COF values are desirable for self-lubricating bearings to reduce energy losses and wear, ensuring optimal performance.
Lubrication Effectiveness Tests
Lubrication effectiveness tests evaluate self-lubricating properties under various conditions. These tests involve running the bearing material against a counter surface, measuring friction and wear over time. Effective self-lubrication is indicated by low friction coefficients and minimal wear.
Thermal Testing
Heat Resistance and Thermal Conductivity Tests
Heat resistance tests determine how well a material withstands high temperatures without degrading, while thermal conductivity tests measure heat transfer ability. High heat resistance and appropriate thermal conductivity prevent failure in high-temperature environments.
Thermal Cycling and Aging Tests
Thermal cycling tests repeatedly heat and cool the material to simulate real-world temperature fluctuations. Aging tests expose the material to elevated temperatures for extended periods, assessing durability and performance over time.
Effects of Temperature on Mechanical Properties
Tests measure changes in tensile strength, compressive strength, and impact resistance at various temperatures, helping select materials that maintain performance across a wide temperature range.
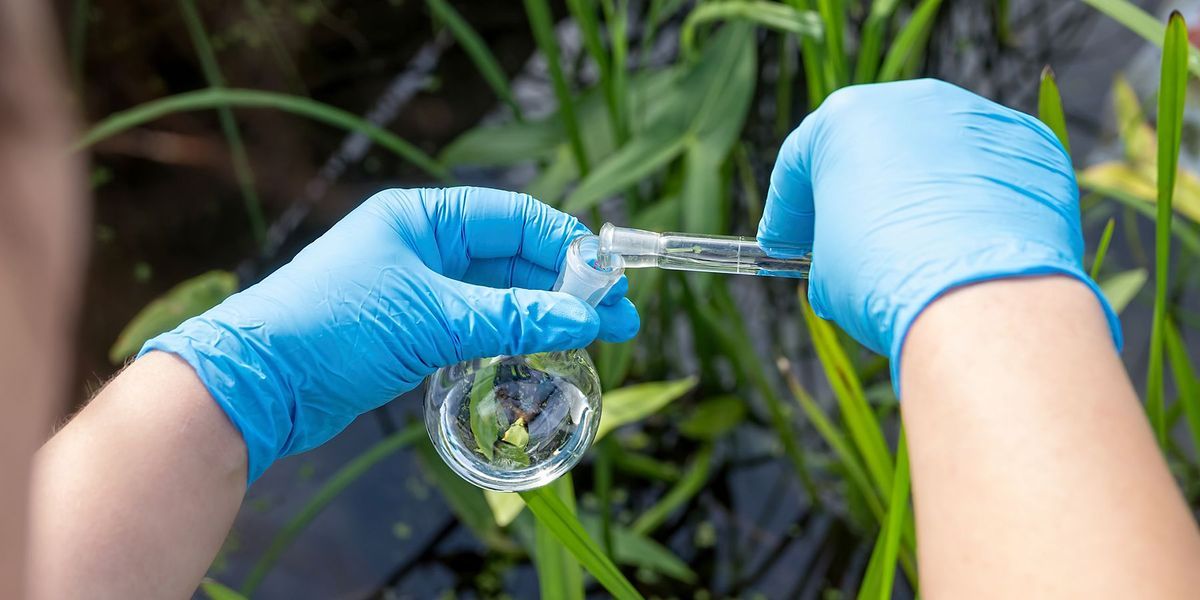
Environmental Testing
Chemical Resistance Tests
Chemical resistance tests expose materials to various chemicals to evaluate durability and performance in aggressive environments. These tests are crucial for applications where bearings encounter oils, solvents, or other chemicals that could cause degradation.
UV and Weathering Tests
UV and weathering tests simulate prolonged exposure to sunlight and outdoor conditions, assessing resistance to degradation. High UV and weathering resistance is essential for outdoor applications.
Moisture Absorption Tests
Moisture absorption tests measure water absorption and its effect on properties. High moisture absorption can lead to swelling and reduced mechanical strength, so these tests ensure material performance in humid or wet conditions.
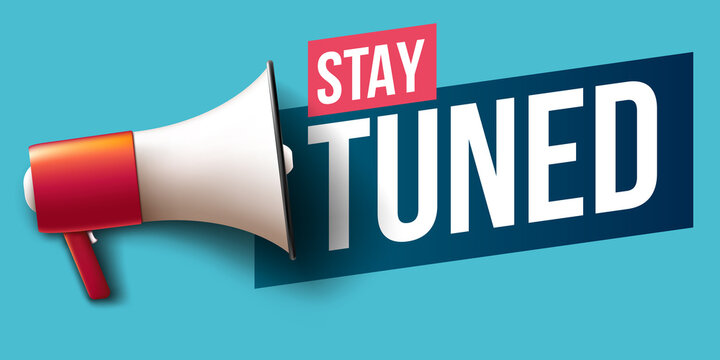