Understanding Hydro
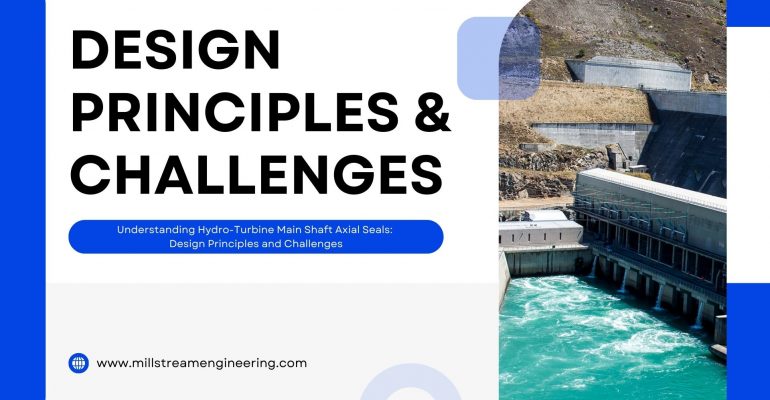
Understanding Hydro
Understanding Hydro-Turbine Main Shaft Axial Seals: Design Principles and Challenges
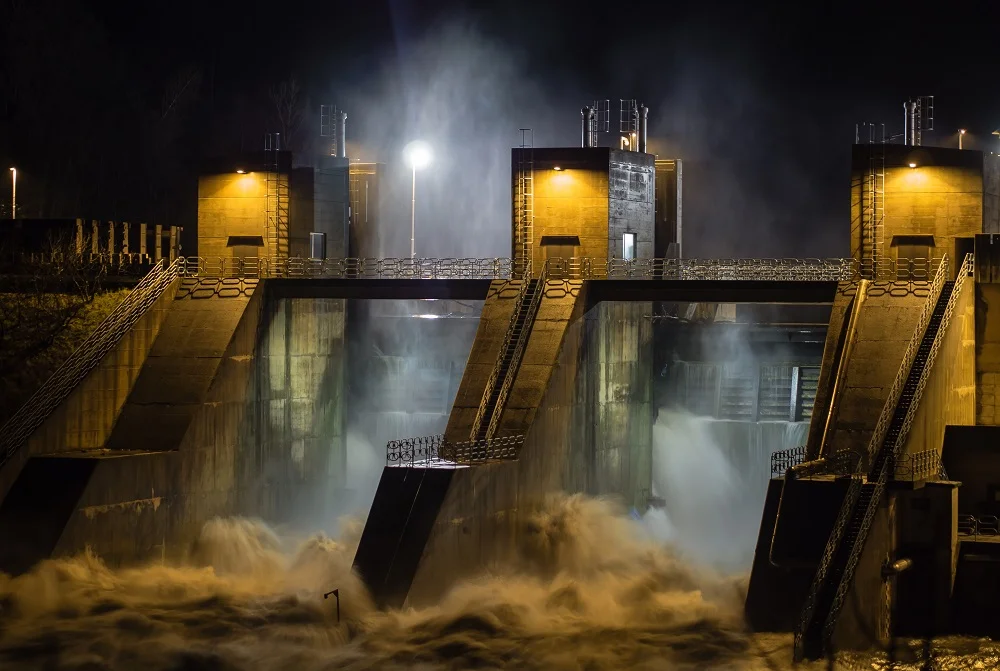
Axial Seal Design Principles for Hydro-Turbines
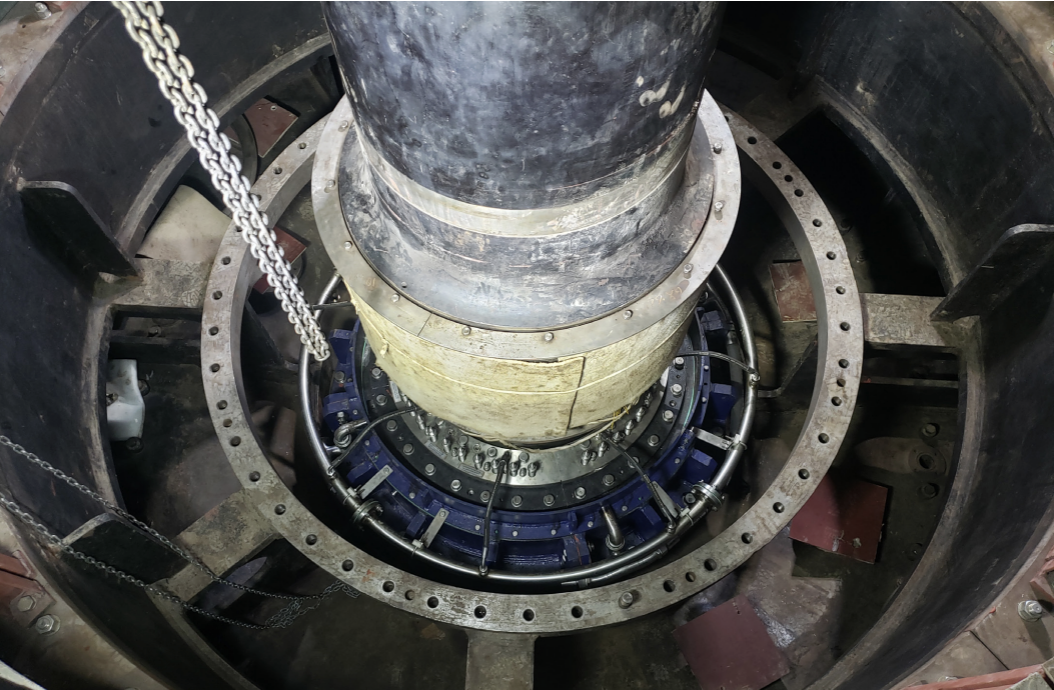
Factors Affecting Axial Seal Performance
Size
Larger seals are prone to increased unevenness due to machining tolerances and deformation caused by fasteners and springs.
Surface Finish
Elastomeric polymer seals cannot be machined to a perfectly smooth finish, often exhibiting surface roughness that contributes to leakage.
Thermal Expansion and Water Swell
Polymers are more susceptible to thermal expansion and water absorption, leading to localized deformation that must be accounted for in the design.
Centrifugal Force
The operation of the turbine generates centrifugal forces that can either aid or hinder leakage, depending on the direction of the flow.
Wear and Static Leakage Paths
As seals wear over time, unevenness in the surface creates dynamic conditions that influence the balance between leakage and frictional heat removal.
Conclusion: Balancing Leakage Control and Performance
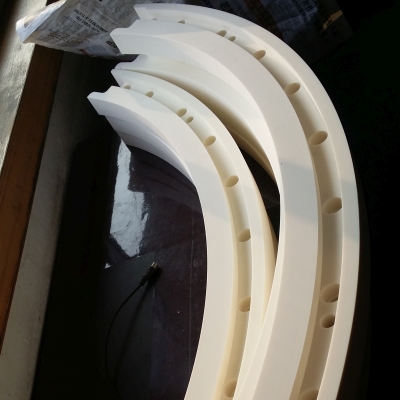