AST Mechanical Seals Case Study
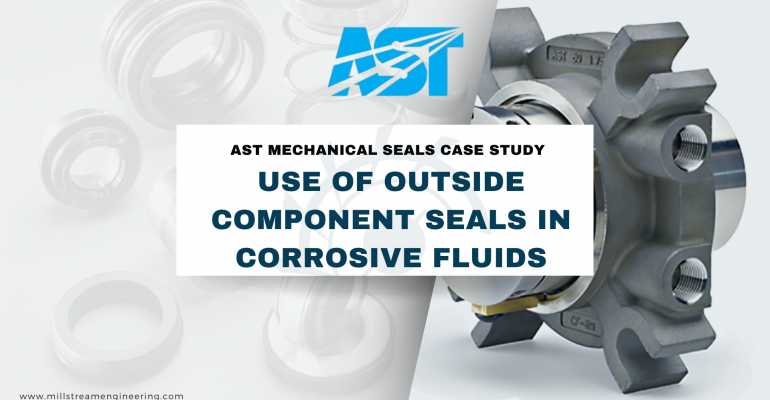
AST Mechanical Seals Case Study
AST Mechanical Seals Case Study: Use of Outside Component Seals in Corrosive Fluids
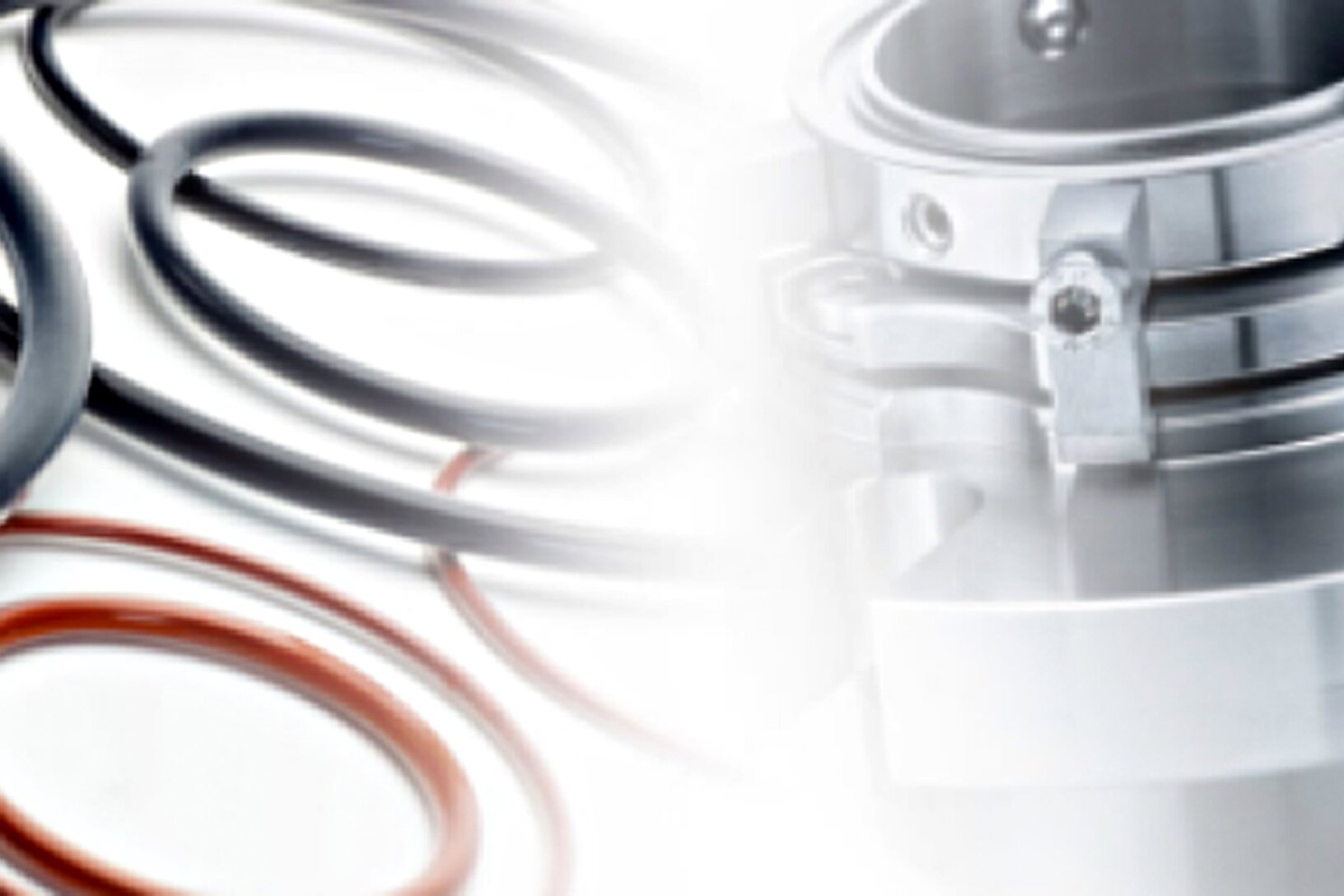
Introduction to AST’s Product Offerings
Why Choose Outside Component Seals for Corrosive Fluids?
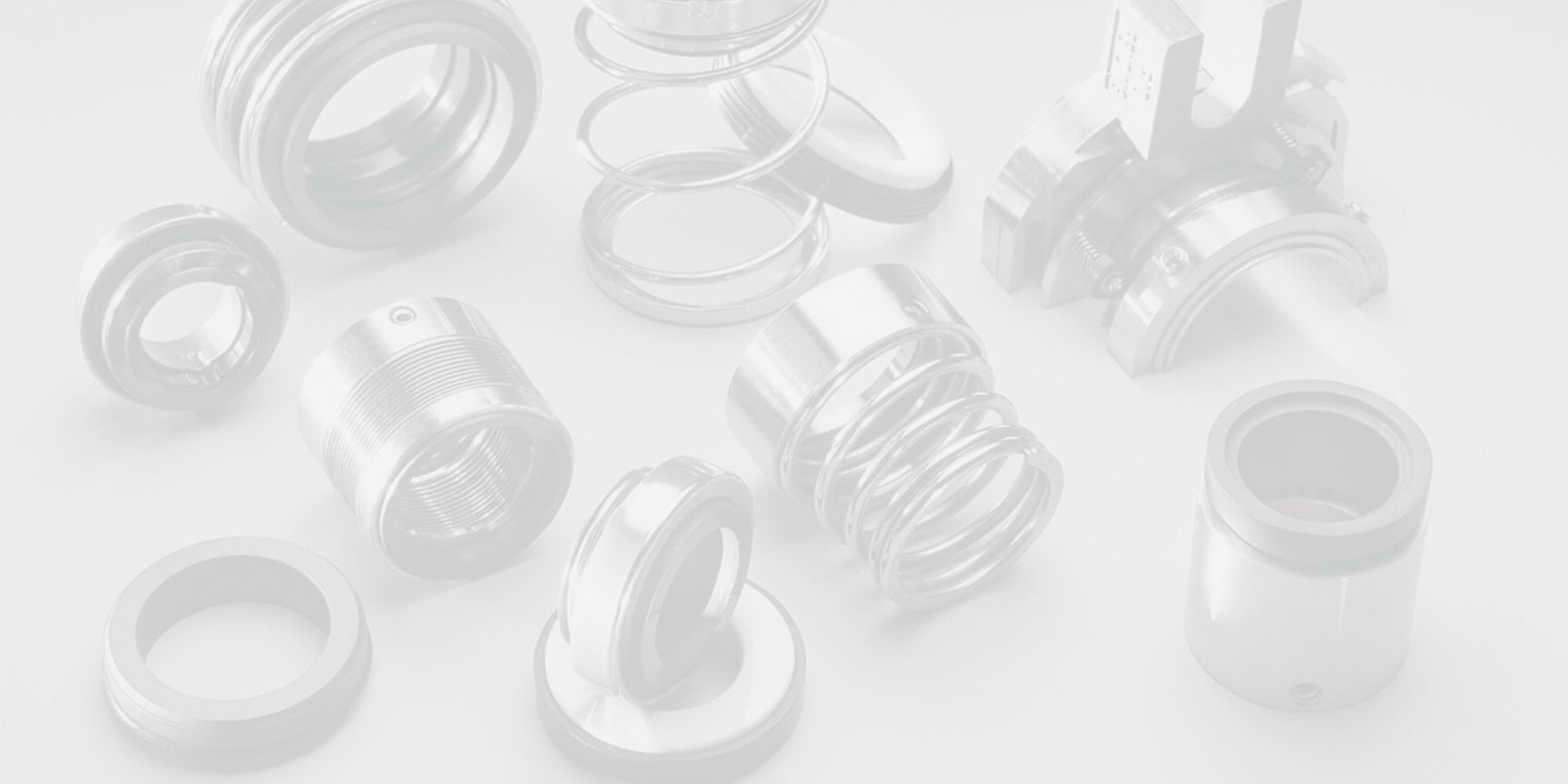
AST50 Multi-Spring Component Outside Seal
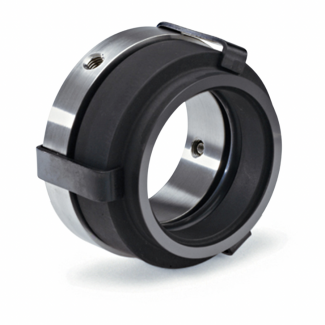
AST60 Multi-Spring Component Inside Seal
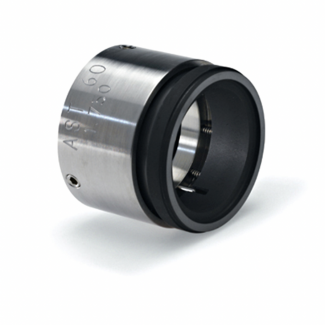
AST70 Single Cartridge Seal
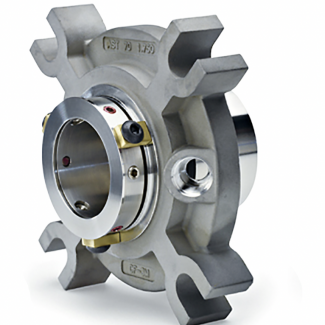
AST80 Dual Cartridge Seal
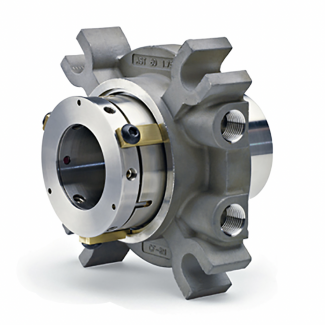
Case Study: Overcoming Challenges with Sodium Nitrate Crystallization
Problem: In a recent application, a manufacturer faced significant issues with sodium nitrate crystallization in a mixer. When the mixer was shut off, the sodium nitrate would crystallize, causing scratches and scarring on the seal faces, leading to leaks and frequent maintenance.
Solution: AST recommended switching to their dual cartridge seal with SC/SC (silicon carbide) hard faces for additional protection. The dual cartridge seal was specifically chosen to address the issue of crystallization by preventing solid formation on the seal faces.
Comments
Outcomes
Conclusion
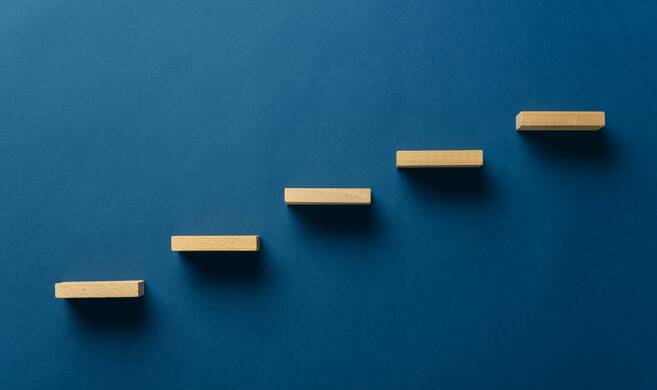