Introduction to Mechanical Sealing for Industrial Applications
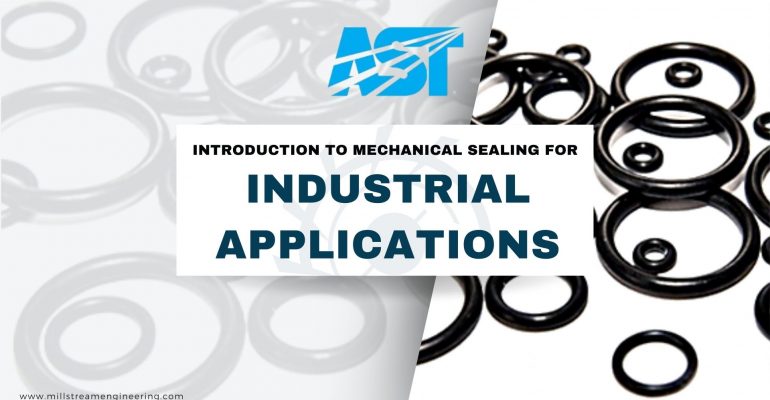
Introduction to Mechanical Sealing for Industrial Applications
Understanding the Basics of Mechanical Seals
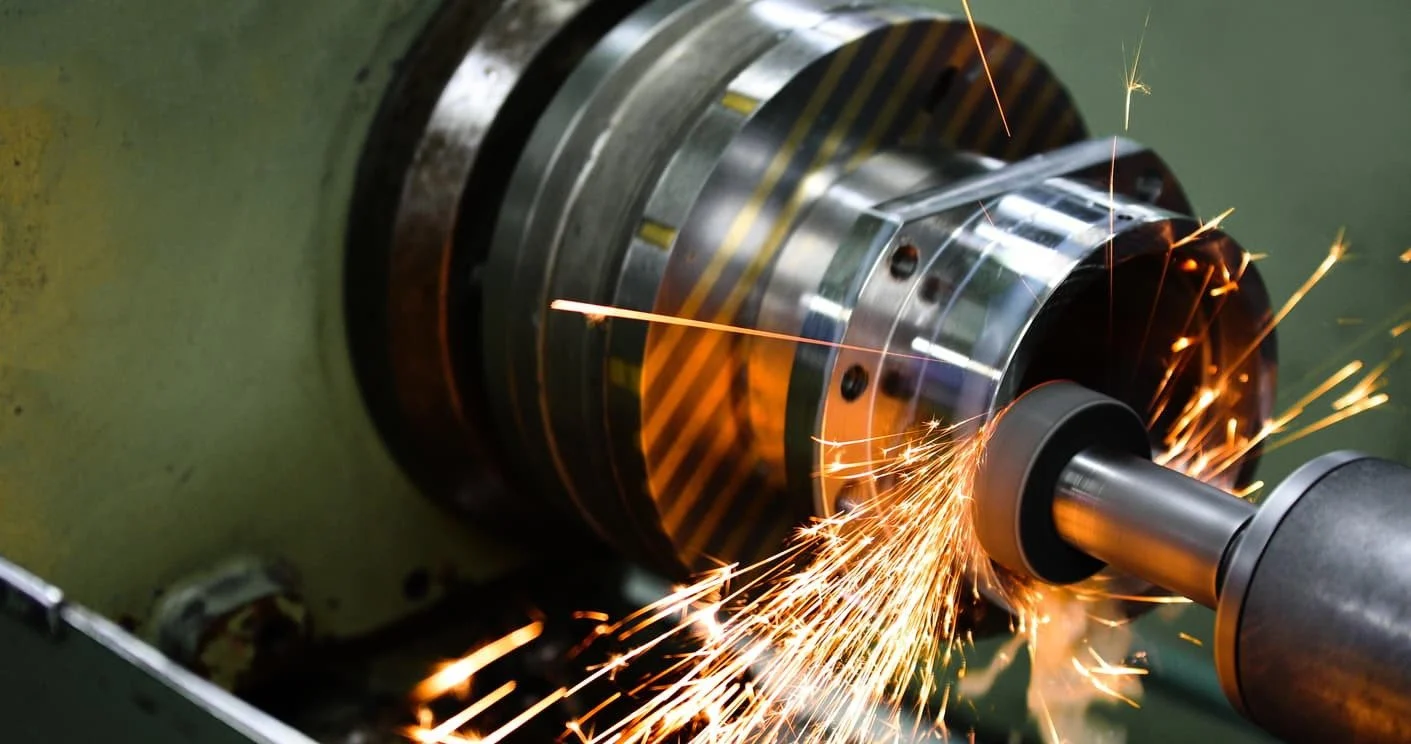
In the world of industrial machinery, mechanical seals play a pivotal role in ensuring the reliability and efficiency of rotating equipment such as pumps, mixers, and compressors. By preventing leaks and minimizing friction, mechanical seals contribute to the smooth operation of machinery, reducing downtime, and extending the lifespan of critical components. This blog post delves into the essentials of mechanical sealing, exploring the different types of mechanical seals. Mechanical seals are used across a wide range of industries, including oil and gas, chemical processing, water and wastewater management, power generation, food and beverage, and pharmaceuticals their applications, and why they are increasingly preferred over traditional packing methods.
Why Mechanical Seals Over Packing?
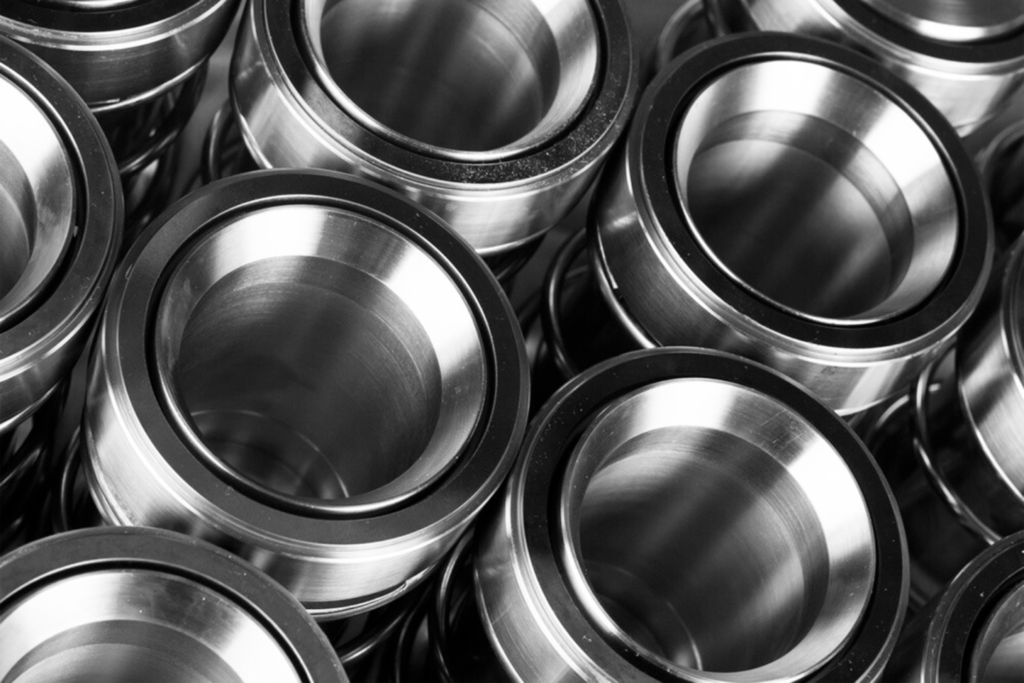
Traditionally, many industrial applications relied on packing to prevent leaks in pumps and rotating equipment. Packing involves compressing material around a shaft to form a seal, which, while effective, has significant drawbacks. Over time, packing can wear down, leading to increased friction, energy loss, and frequent maintenance requirements. Additionally, packing requires continuous adjustment to maintain its sealing capabilities, which can be both time-consuming and costly.
Mechanical seals, on the other hand, offer a modern solution that addresses these issues. Unlike packing, mechanical seals create a more reliable seal by using a combination of rotating and stationary elements that come into contact under controlled conditions. This design minimizes wear and tear, reducing friction and heat generation, which ultimately leads to a longer lifespan for the equipment.
Some of the key advantages of mechanical seals over packing include:





Types of Mechanical Seals
Mechanical seals are available in a variety of designs, each suited for specific industrial applications. Understanding the different types of mechanical seals can help in selecting the right solution for your needs.
OEM Style (Single Spring Seals)
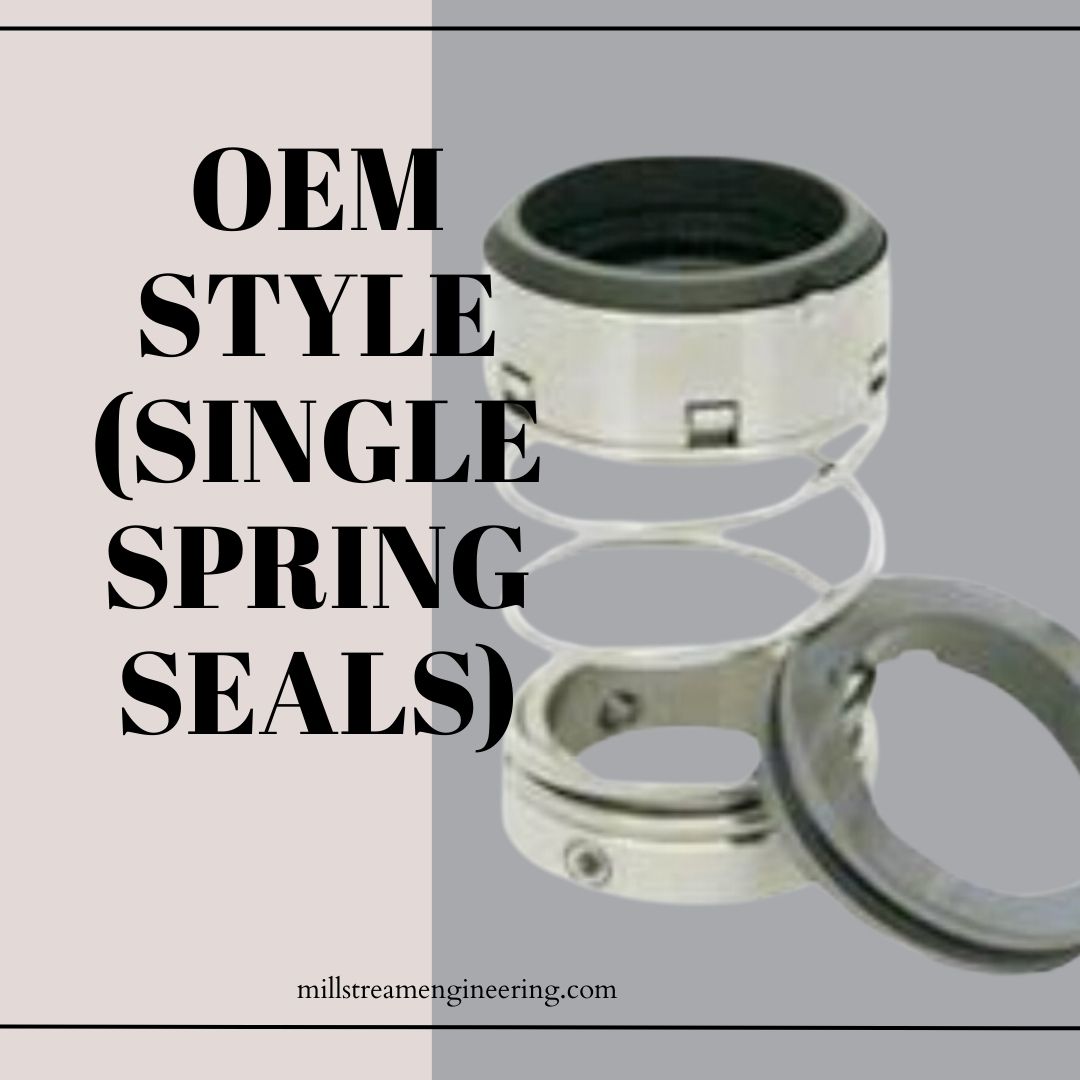
These seals are commonly used in standard applications and are known for their cost-effectiveness. The single spring design is relatively simple but requires precise installation to function correctly. OEM style seals are a good choice for general-purpose applications where cost is a primary concern.
Outside Component Style
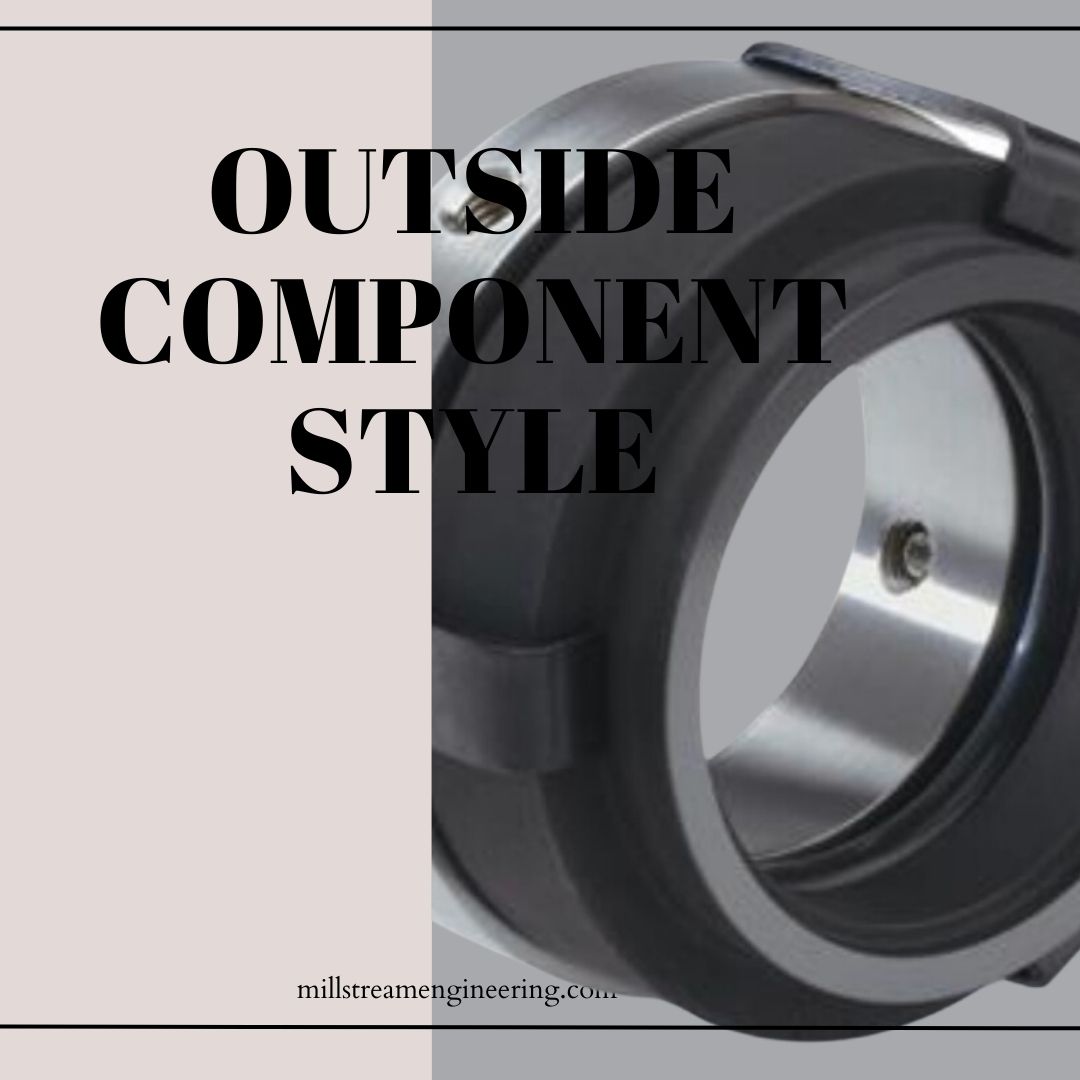
Outside component seals feature multiple springs that provide even loading across the seal faces. This design is more robust than single spring seals and is ideal for applications where the seal must withstand higher pressures or more demanding conditions. However, the installation process is more complex, requiring a higher level of expertise.
Inside Component Style
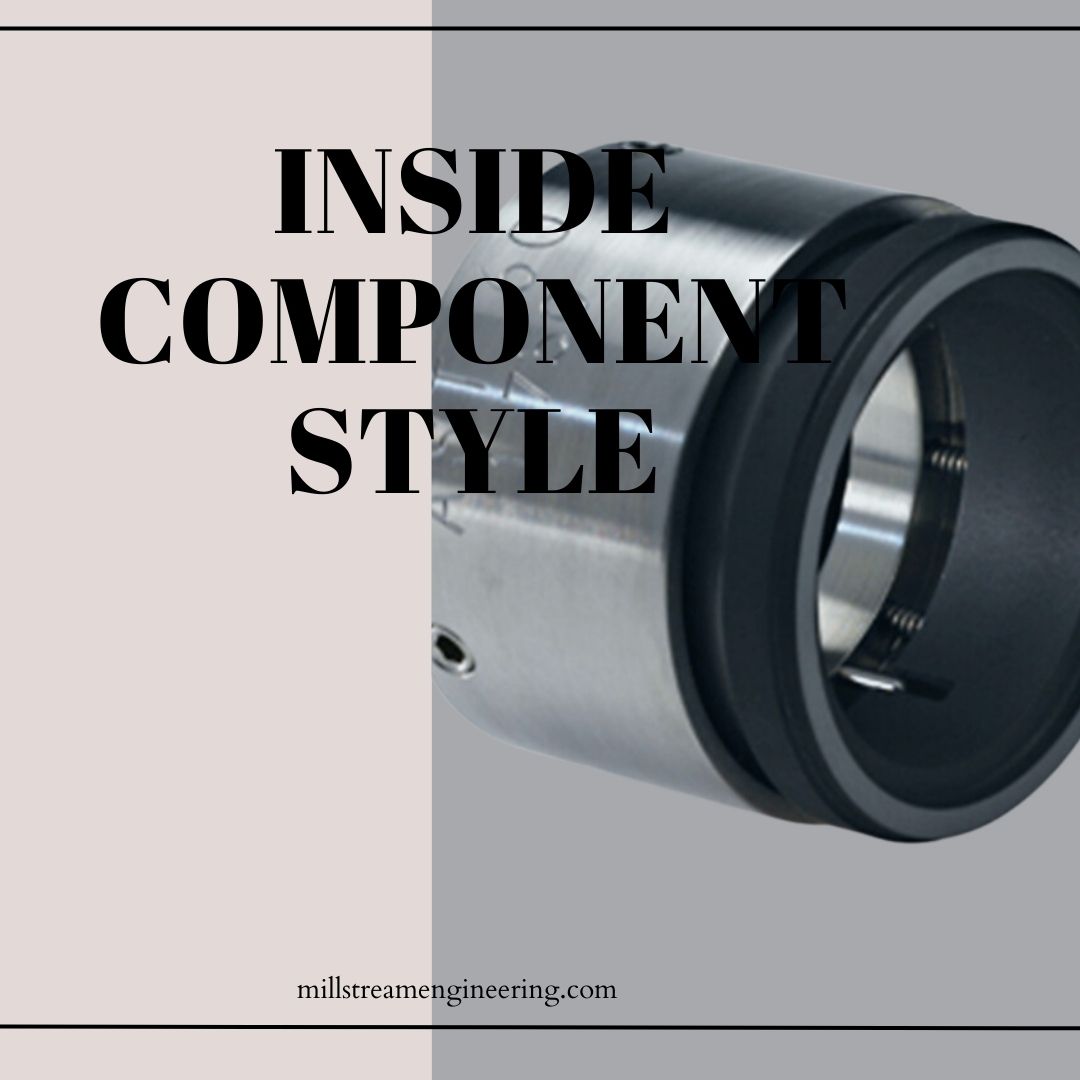
Similar to the outside component style, these seals have springs located inside the process fluid. This configuration allows the springs to be shielded from external contaminants, making inside component seals suitable for environments where cleanliness is critical, such as food and beverage processing.
Single Cartridge Style
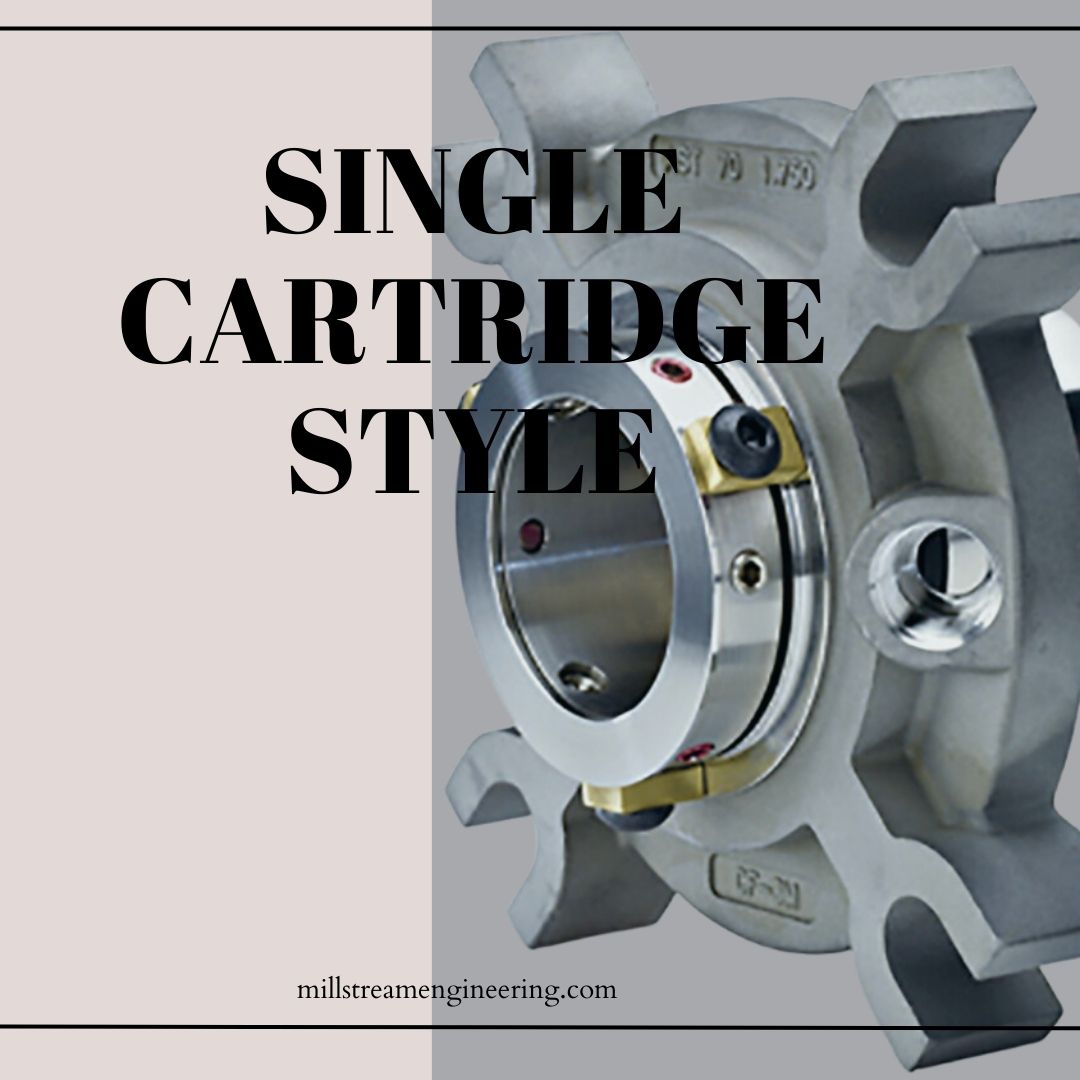
Single cartridge seals are pre-assembled units that simplify the installation process. The springs in these seals are preset outside the process fluid, reducing the risk of installation errors. While they may have a higher upfront cost, single cartridge seals offer long-term savings through reduced installation time and lower maintenance requirements.
Dual Cartridge Style
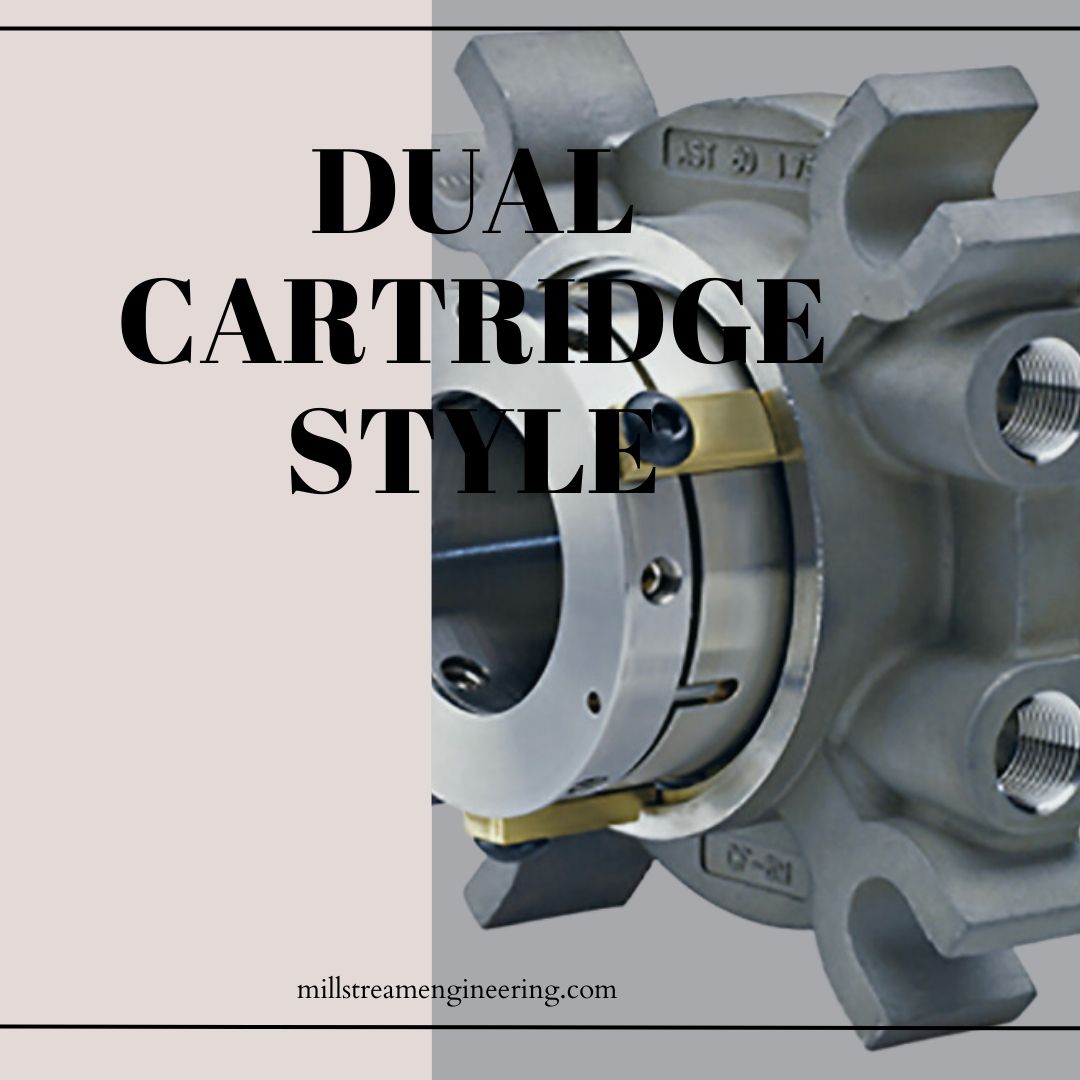
Dual cartridge seals combine two mechanical seals into one assembly, providing an additional layer of protection for challenging environments. These seals are often used in applications involving hazardous or corrosive fluids, where a secondary seal is necessary to prevent leaks if the primary seal fails.
Applications of Mechanical Seals
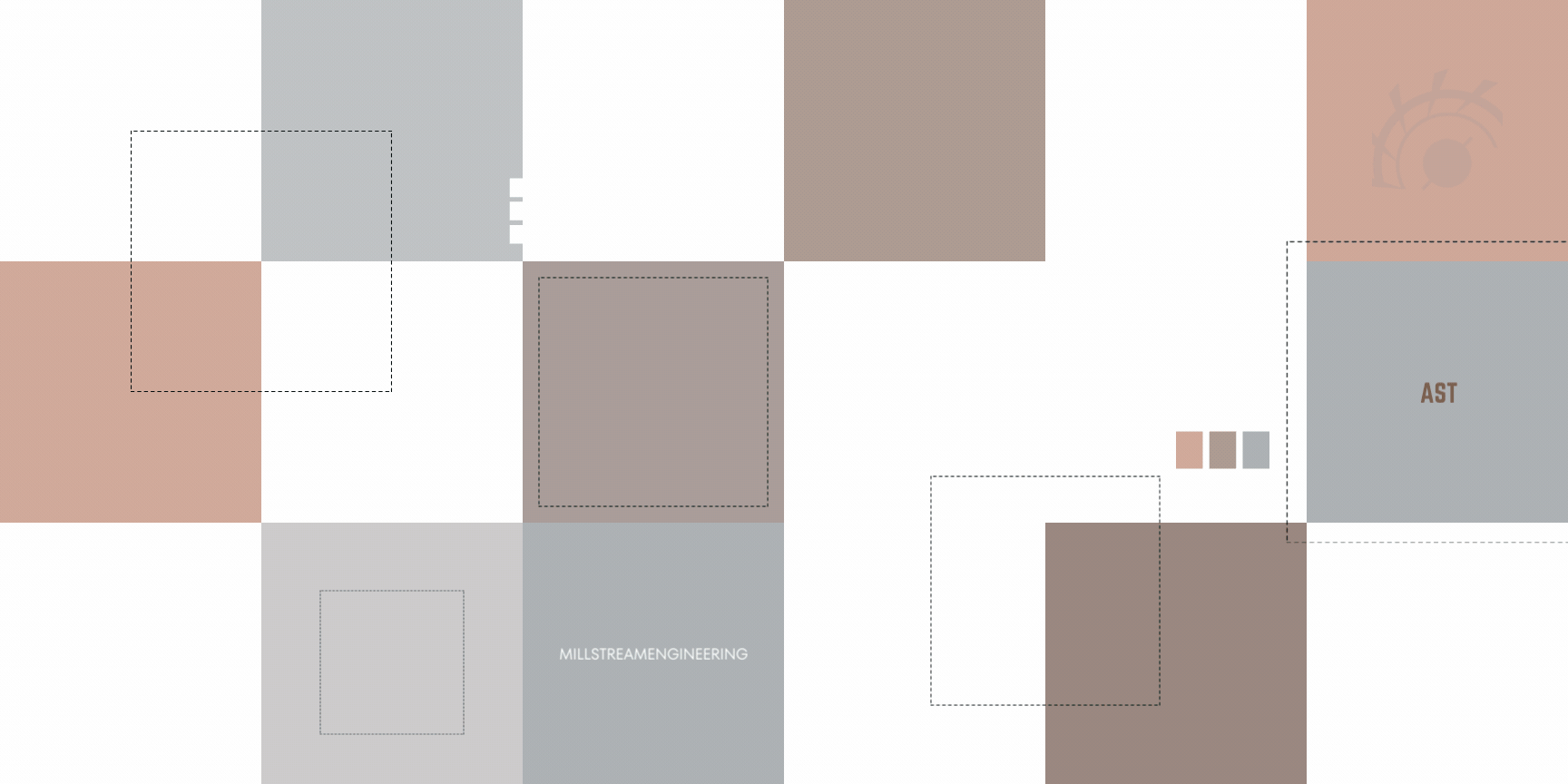
Mechanical seals are used across a wide range of industries, including oil and gas, chemical processing, water and wastewater management, power generation, and pharmaceuticals. The choice of mechanical seal depends on several factors, including the type of fluid being sealed, operating temperature and pressure, and the specific requirements of the application.
For instance, in the oil and gas industry, mechanical seals must withstand extreme temperatures and pressures, as well as corrosive and abrasive fluids. In contrast, in the food and beverage industry, seals must comply with stringent hygiene standards and be able to operate effectively in clean, low-temperature environments.
Conclusion
Selecting the right mechanical seal is crucial for optimizing the performance and longevity of your industrial equipment. By understanding the different types of mechanical seals and their respective applications, you can make informed decisions that will enhance the efficiency and reliability of your operations. Whether you are looking to reduce maintenance costs, improve energy efficiency, or extend the life of your equipment, mechanical seals offer a superior solution compared to traditional packing methods.
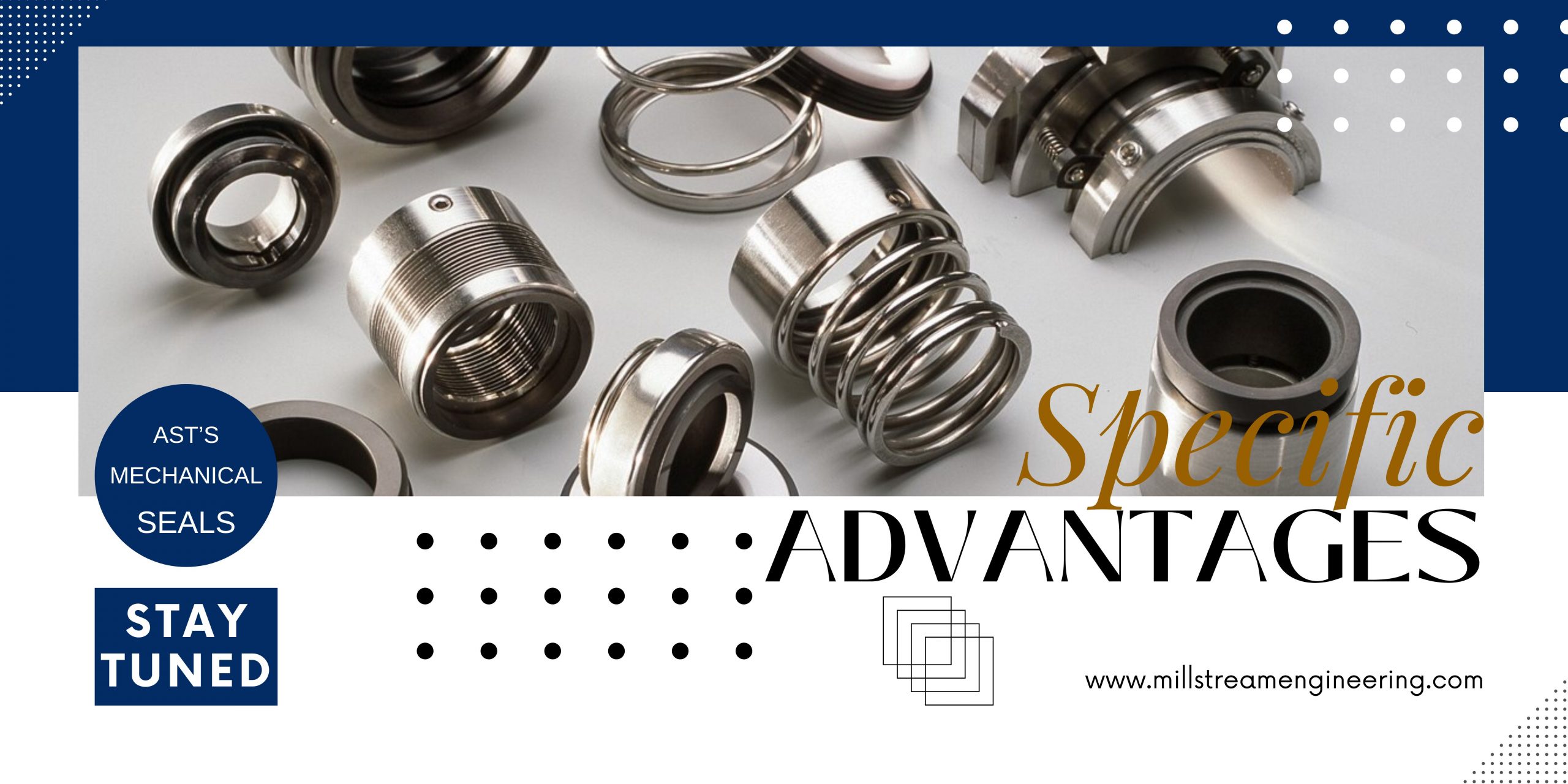
Stay tuned for our next blog post, where we will dig deeper into the specific advantages of AST’s mechanical seals and how they are engineered to meet the unique challenges of various industrial applications.