Preventing wear of shafts in water lubricated bearing applications
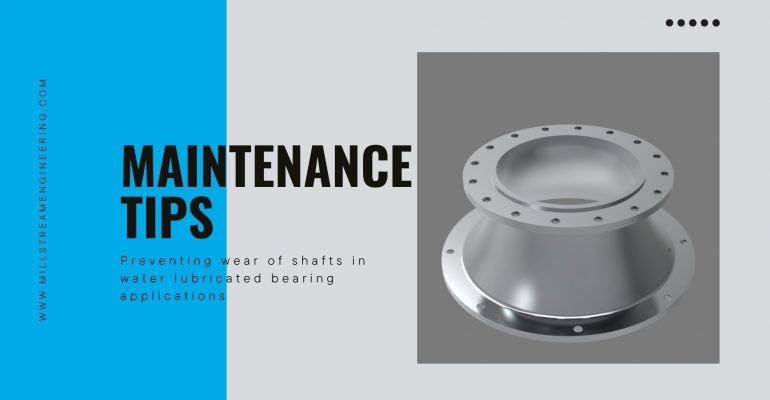
Preventing Wear in Water-Lubricated Bearings: Strategies for Long-Lasting Performance
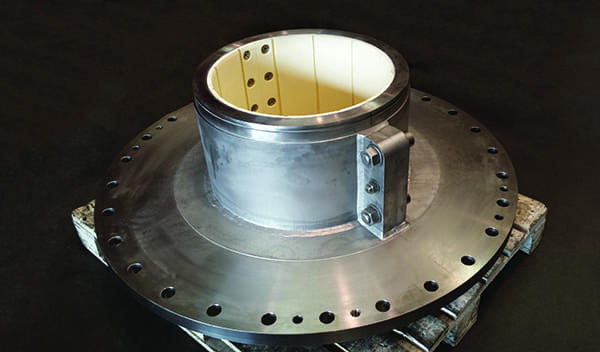
Preventing Wear in Water-Lubricated Bearing Applications
Water-lubricated bearings are ideal for eco-friendly applications where oil contamination is a concern. However, water’s low viscosity and limited lubrication properties can accelerate wear, particularly on bearing surfaces and shafts. To maximize the lifespan of these systems, engineers and maintenance professionals can use a range of techniques to effectively reduce wear.
1. Hardened Shaft Sleeves
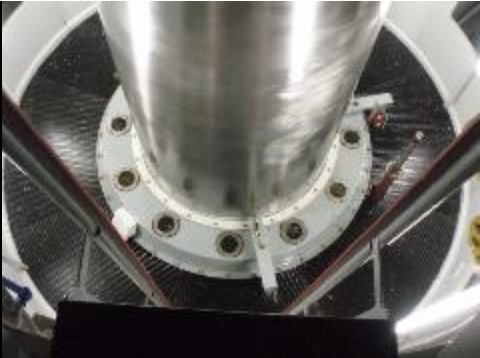
Hardened shaft sleeves offer a robust solution for protecting the shaft from wear. By encasing the shaft in a tougher material, such as stainless steel or ceramic, these sleeves can resist abrasion from water and contaminants. Hardened sleeves are especially valuable in high-demand applications where durability and corrosion resistance are essential.
2. Shaft Coatings
Applying specialized coatings to the shaft is an effective strategy to minimize wear and corrosion in water-lubricated environments. Common coatings like tungsten carbide, chromium oxide, and diamond-like carbon (DLC) create a hard, protective barrier that reduces friction and extends the shaft’s life. Another excellent option is Nickel Chrome Boron (NiCrB) coating, which offers outstanding wear resistance and corrosion protection. NiCrB is particularly effective in high-wear applications, as it forms a dense, durable layer that withstands abrasive conditions and maintains performance even under constant exposure to water. The choice of coating depends on the specific operating environment, with each type tailored to different performance needs.
3. Water Filtration
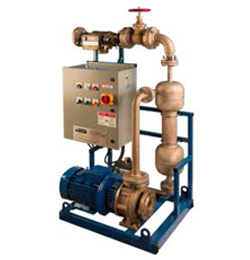
Contaminants in water, such as dirt, grit, and particulates, are significant contributors to wear. Installing a high-quality filtration system can keep the water clean, minimizing the abrasive impact on bearing surfaces. Regular maintenance of the filtration system is crucial to ensure optimal performance and prolong the lifespan of bearings and shafts alike.
4. High-Quality Bearing Materials
Selecting resilient materials for bearings is vital for wear reduction. Materials like elastomers and polymer composites perform well in water-lubricated environments due to their low friction properties and resistance to wear. These materials are suited to the unique challenges of water lubrication, providing a longer lifespan for the bearings.
5. Hydrodynamic Groove Design
Hydrodynamic performance relies on the water film that forms as the bearing rotates, separating surfaces and reducing wear. Proper groove design is essential to enhance this effect. The size, shape, and quantity of grooves in the bearing significantly impact the distribution and thickness of the water film. Small, strategically placed grooves can optimize film formation, while too many or overly large grooves may cause the water film to dissipate, reducing load-carrying capacity and increasing wear.
6. Routine Maintenance and Predictive Monitoring
Routine inspections and predictive maintenance play a critical role in preventing unexpected wear. Techniques like vibration analysis and ultrasonic testing help detect early signs of wear, misalignment, or contamination. Identifying and addressing these issues proactively reduces damage, prolongs equipment life, and minimizes costly repairs.
Conclusion
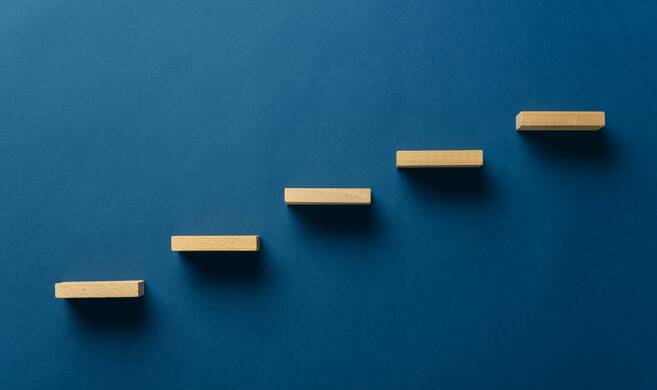
Wear prevention in water-lubricated bearing systems involves selecting durable materials, improving hydrodynamic performance, and maintaining a contaminant-free environment. Techniques such as hardened sleeves, shaft coatings, filtration, and optimized groove design work together to extend bearing life. By integrating these methods, engineers and maintenance teams can improve reliability, reduce downtime, and cut maintenance costs in water-lubricated applications.