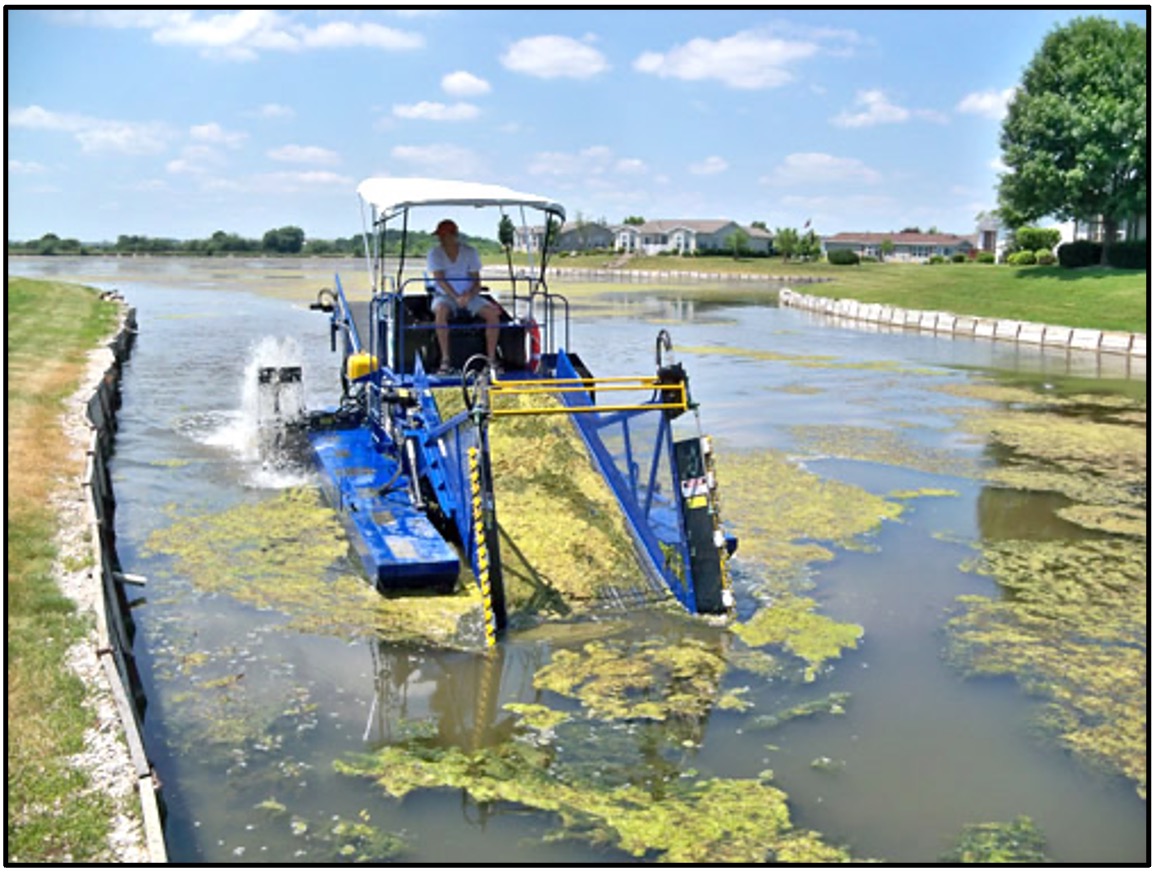
Problematic Water Filtration? Demystifying the Journey to a Reliable System
Problematic Water Filtration? Demystifying the Journey to a Reliable System
When dealing with water filtration in hydroelectric plants, many of us may ponder – why not just utilize raw water? This article will help you comprehend the importance of water filtration, its benefits to the operator, and provide an overview of various filtration technologies.
The Challenges in Water Filtration
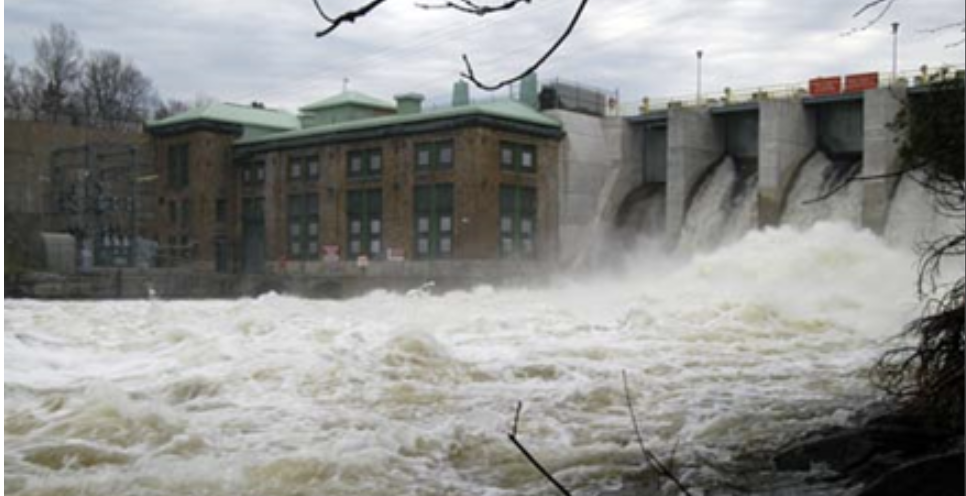
The Essence of Filtration in Hydroelectric Plants
Within the confines of a typical hydro plant, water is primarily used for cooling and lubrication (aside from generating power!). The generator and generator bearings, for example, utilize water for oil cooling. Water also aids the cooling and lubrication of turbine guide bearings and shaft seals. The longevity of these essential components rests significantly on the quality of the lubricating water that is supplied to them – it is effectively the “lifeblood” of a water-lubricated turbine bearing or shaft sealing system. Moreover, in the Hydraulic Power Unit (HPU), it functions as a heat exchange medium for maintaining the correct temperature of hydraulic oil.
The source of raw water in such scenarios can vary, ranging from direct river water, water from head ponds or tail waters, or from upstream reservoirs, to pressurized water from Penstocks. Groundwater or well water and city or municipal water supplies also serve as potential sources.
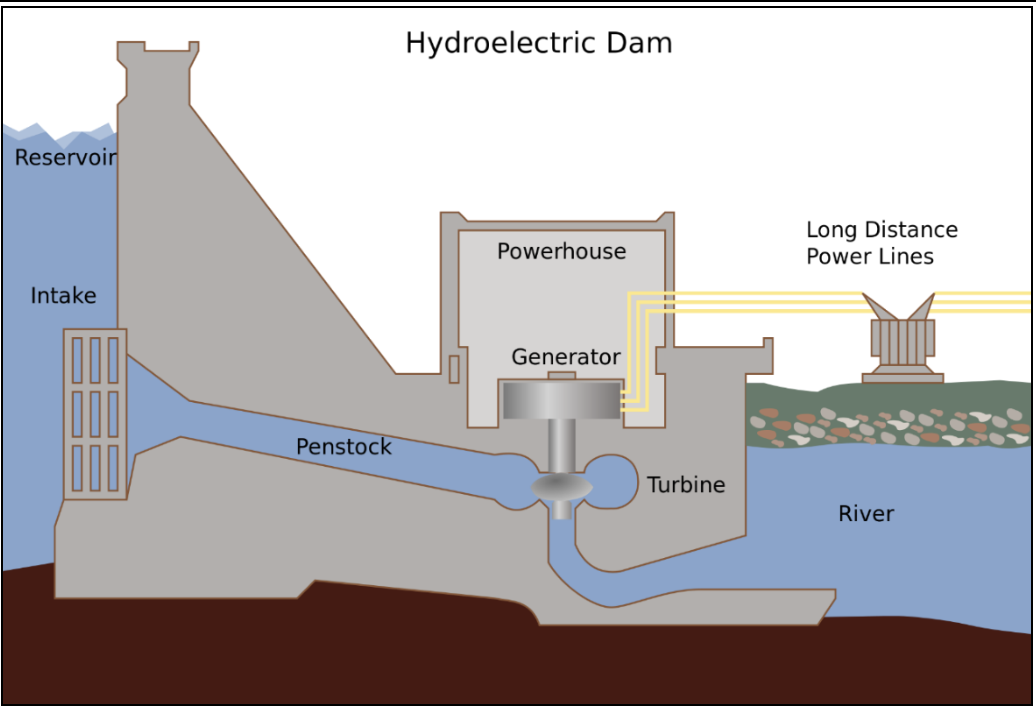
However, raw water comes with its own set of challenges that require filtration. These challenges can be natural or man-made, including rocks, sand, fine silt, mud, glacial till, and even floating lava particles (pumice). Organic matter such as leaves, pine needles, sticks, logs, trees, humus, peat, and algae also add to the problem, as do man-made pollutants like trash, plastic, and metal. In certain cases, marine growth, such as zebra mussels, could also pose significant problems.
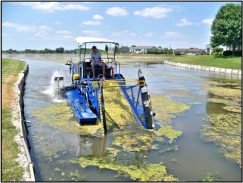
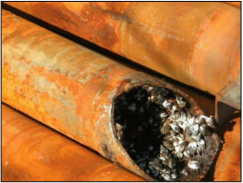
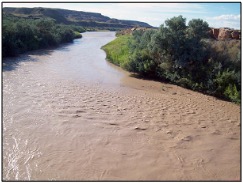

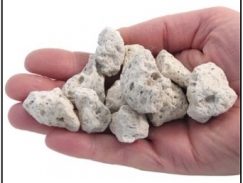
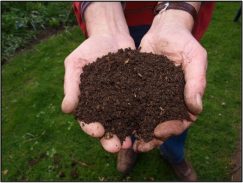
How Does Water Filtration Aid the Operator?
Water filtration helps operators control the bearing and seal wear environment. For any water-lubricated guide bearing or shaft seal, the flow of water is critical for flushing abrasives, cooling, and hydrodynamic lubrication. Filtration to a level of less than 100 microns is advisable for maximizing bearing and shaft seal life and providing consistent wear behavior.
Filtration level and minimum flow rates are generally recommended by the seal or bearing manufacturer, typically ranging from 25 – 200 microns. For oil cooling/heat exchangers, the filtration requirements are less stringent, typically below 500 microns. Monitoring and alarms on bearing water flow rate & supply pressure can significantly reduce the risk of bearing or seal failure.
Filtration systems come in various styles & configurations and can be flow or pressure regulated, or both. These systems typically have at least two stages: pre-filtration or coarse strainers and primary filtration.
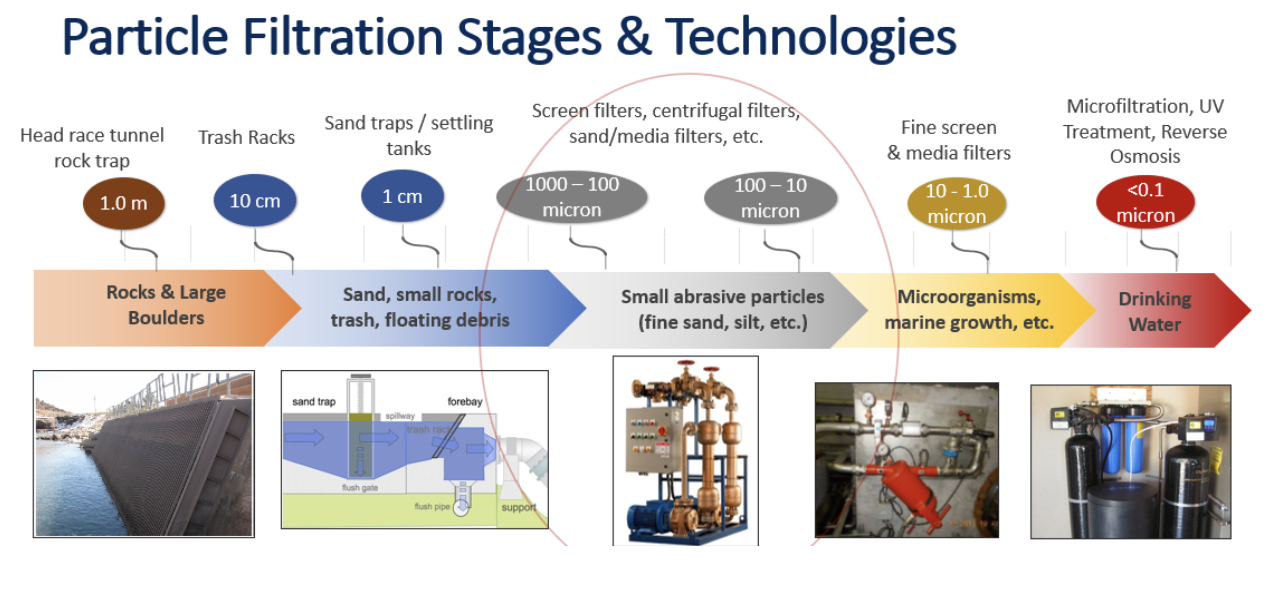
A Quick Look at Filtration Technologies
There are various types of equipment that can be used in water filtration systems:
- Manual Screen Filters: These are mechanically simple, low-cost options with internal baskets or bags for filtration. They are highly reliable but require manual switchover and/or back flushing to remove debris.
- Centrifugal Separators (Hydro Cyclones): They offer low maintenance, high reliability, and high flow rates, with the capacity for customization to suit site and customer requirements. These require automatic or continuous purging of debris.
- Sand or Media Filters: These can achieve very fine filtration levels but have high water consumption for back flushing cycles. Their large size may require a pressure tank or reservoir to deal with fluctuation in demand.
- Automatic Backflushing Filters: These have high flow rate capacity with automatic cleaning or back flushing. They are mechanically complex and their reliability depends on sediment loading and the quality of design.
Understanding the importance of water filtration in hydroelectric plants and the relevant technologies can be instrumental in maintaining operational efficiency, reducing wear and tear, and ensuring the longevity of the plant’s key components.
With extensive experience and industry-leading expertise, Millstream Engineering is well-positioned to assist you at every stage of your water filtration journey. Whether you need help understanding the available technologies in the marketplace, solving common filtration system issues, optimizing your overall turbine water supply system, or meeting specific manufacturer requirements for water filtration levels, Millstream Engineering is your go-to partner.
We recognize that in some cases, achieving the required filtration level may be almost unattainable, making it necessary to consider alternate solutions like reevaluating bearing and seal material selection. At Millstream Engineering, we are prepared to walk this path with you, guiding you towards the most reliable and trouble-free system.