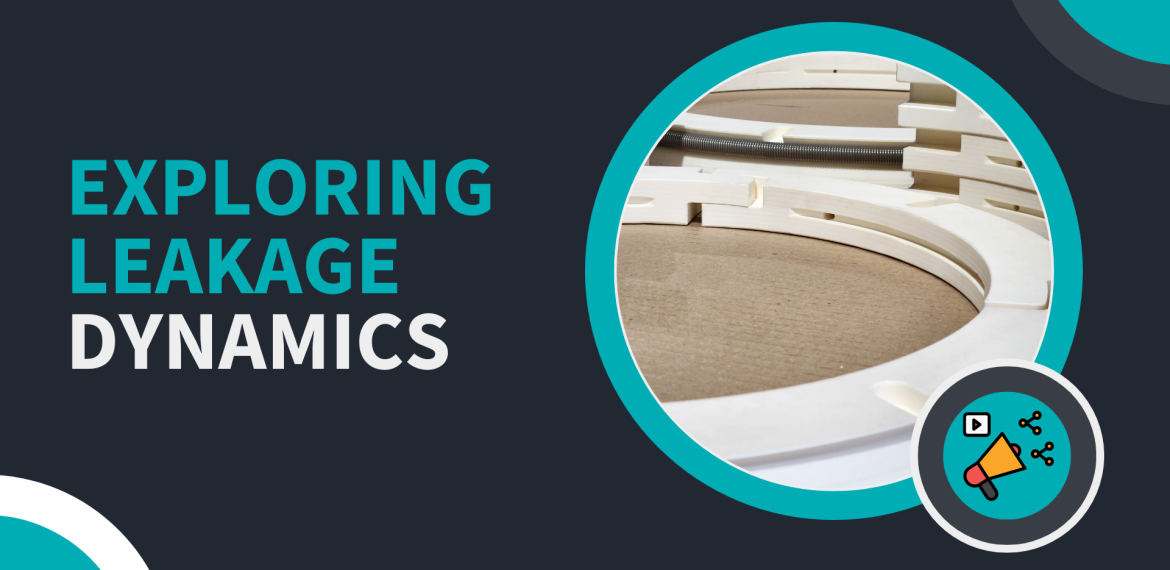
Exploring Leakage Dynamics: Advanced Insights into Radial Shaft Seal Design
Exploring Leakage Dynamics: Advanced Insights into Radial Shaft Seal Design
Radial segmented shaft seals play a vital role in the reliable operation of large hydro turbines, which can feature shaft sizes ranging from 400 to 2000+ mm (16 to 80 inches). Understanding the specific leakage pathways within these seals is critical, particularly when considering the varying designs and material compositions used in modern sealing solutions.
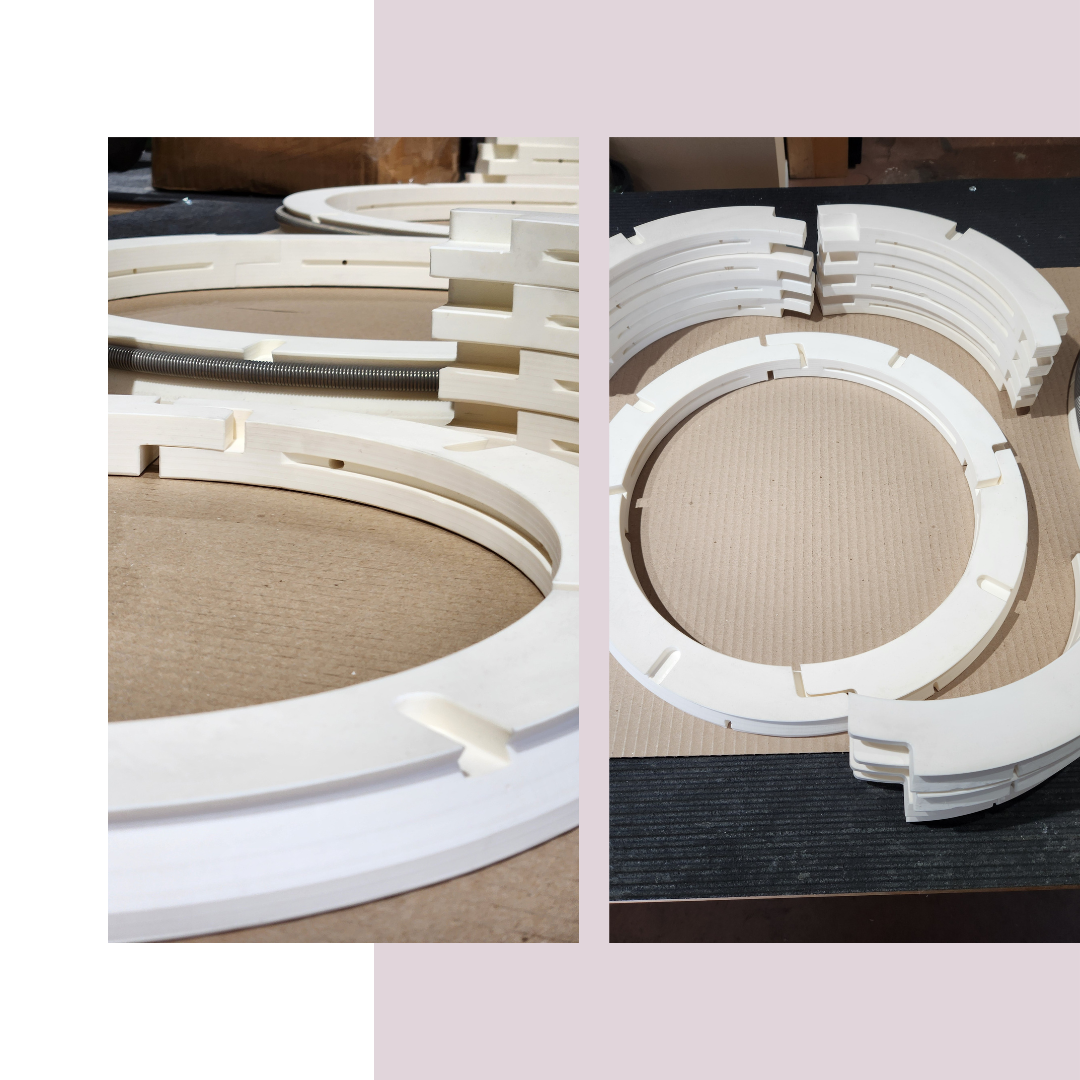
Contextual Background on Turbine Seal Applications
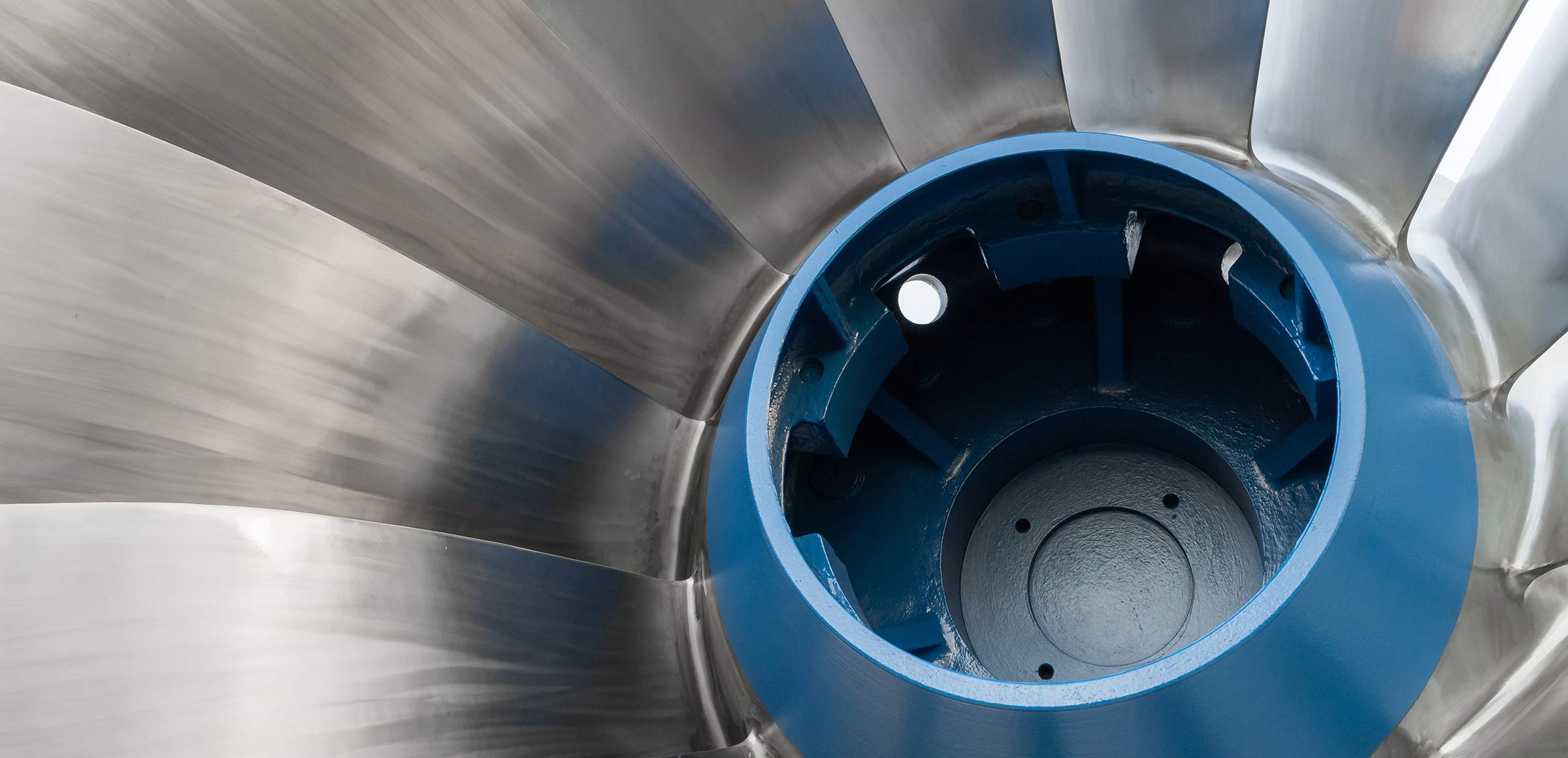
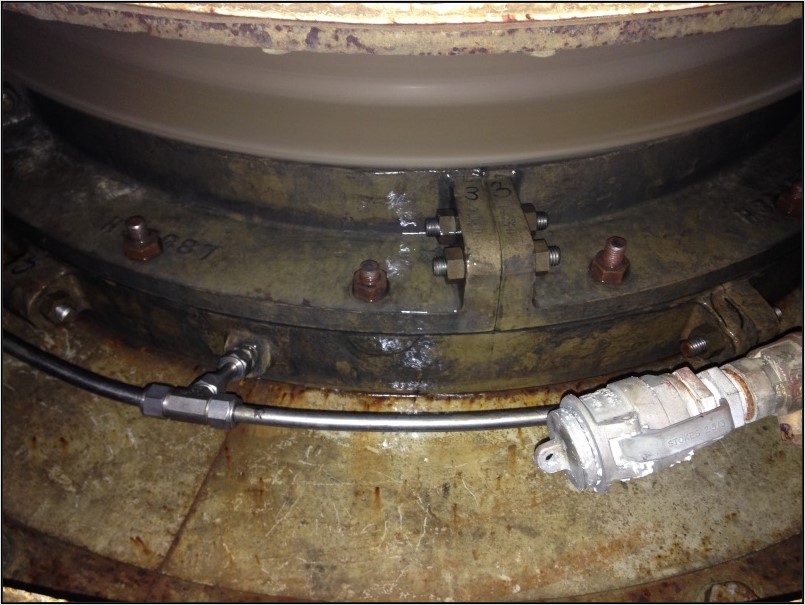
Large hydro turbines rely on segmented rings of carbon, phenolic, or elastomer materials, typically arranged in two, three, or four stages, to ensure effective sealing of the water pressure in the turbine below the head cover. These segmented rings, while highly effective at minimizing the leakage from the turbine, they are not able to act as an entirely watertight seal. For such large shaft diameters, it is not practical or cost-effective to strive for a “zero-leakage” solution, and some amount of reasonable leakage is easily managed via drains and head cover pumps.
Detailed Leakage Pathways in Radial Shaft Seals
Given the structural and operational complexity of these seals, understanding their leakage pathways is essential for predictive maintenance and design optimization:
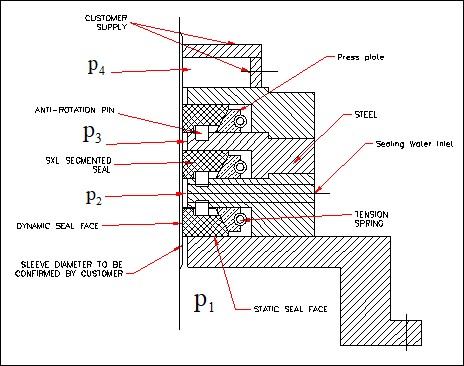
- Segmental Interaction Points
The interaction points between segmented carbon rings, especially in the tongue and groove areas, are critical leakage pathways. The design of these areas, particularly in the context of the seal’s three-stage construction, necessitates precise engineering to minimize leakage. The introduction of higher-pressure injection flow between the first and second rings not only aids in lubrication and cooling but also serves as a preventive measure against abrasive ingress, thereby influencing the leakage dynamics.
- Dynamic Sealing Interfaces
The area where the seal contacts the rotating shaft is of paramount importance. Utilizing materials like SXL enhances the seal’s resistance to wear and abrasion, thus reducing the likelihood of leakage. The seal’s design, incorporating a garter spring, ensures consistent pressure against the shaft, minimizing the gap and, consequently, the leakage potential during both operational and downtime periods.
- Static Sealing Interface
The seal’s contact with the housing introduces another potential leakage path. Despite the seal’s design to conform to the housing under differential pressure, this interface can never be perfectly sealed. Understanding the material properties, such as those of SXL, helps in predicting the seal’s behavior under varying pressure conditions and aligning the seal design accordingly to mitigate leakage.
Importance of Advanced Material and Design Consideration
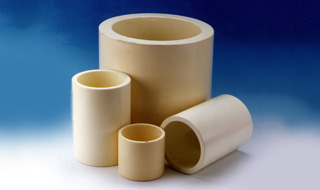
The transition to advanced materials like Thordon’s SXL in seal construction underscores the industry’s shift toward more resilient and long-lasting sealing solutions. These materials not only extend the operational life of the seals but also enhance their performance under adverse conditions, offering a twofold benefit of reduced leakage and improved reliability. SXL, a tough synthetic polymer alloy, is recognized for its superior abrasion resistance and durability compared to traditional seal materials, making it an excellent choice for harsh turbine environments.
Radial shaft seal leakage remains a complex challenge, necessitating a deep understanding of the seal’s design, material properties, and operational environment. By focusing on the critical leakage pathways and leveraging advanced materials, designers can significantly improve seal performance in large hydro turbines. This comprehensive approach ensures that the seals not only meet but exceed the operational demands of modern hydroelectric power generation, marking a significant step forward in the field of mechanical engineering and fluid dynamics.
Join us for an enlightening webinar that will explore the advanced concepts of radial shaft seal design, with a special focus on case studies of seal retrofits within Canada. This session is an excellent opportunity to gain insights into real-world applications and the impact of innovative sealing solutions on turbine efficiency and durability. Learn from detailed case studies, interact with leading experts, and get your questions answered. Sign up now to enhance your knowledge and stay at the forefront of seal design technology in Canada.