Resimac Solutions: Part 1 – Safeguarding Stationary Components in Hydropower
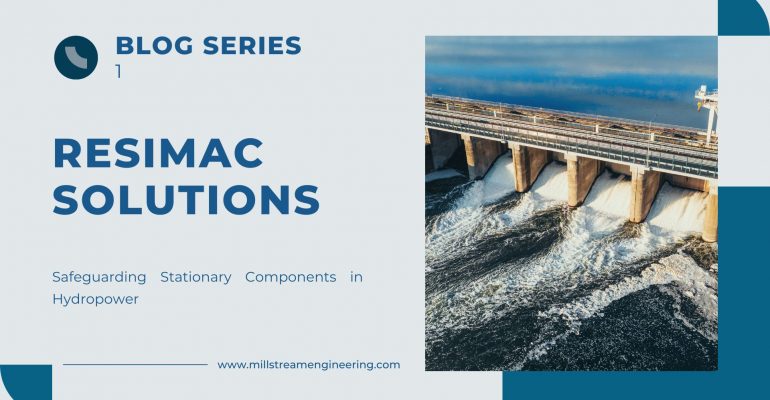
Resimac Solutions: Part 1 – Safeguarding Stationary Components in Hydropower
Introduction
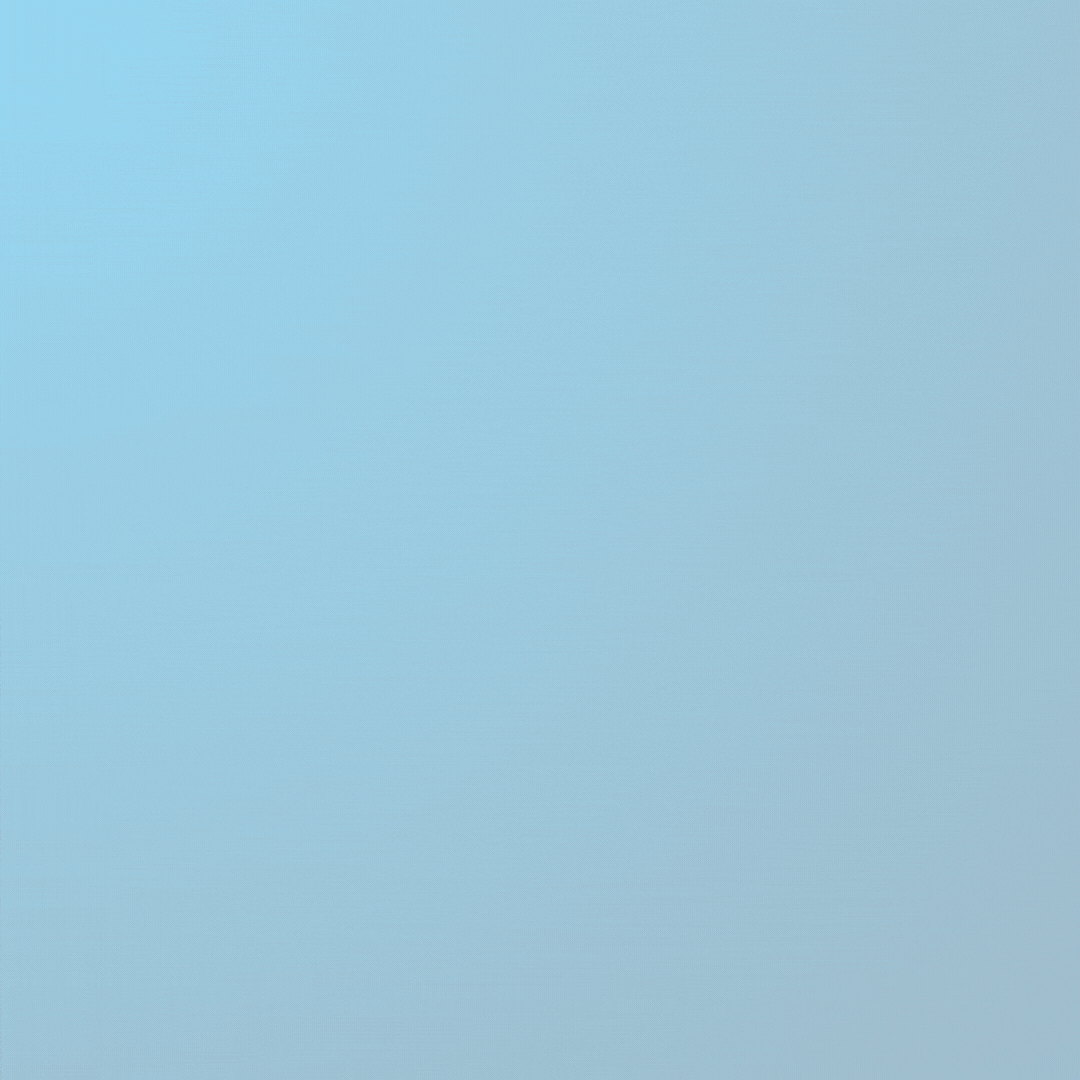
Case #1 – Stay Vanes – Rebuild Leading Edges
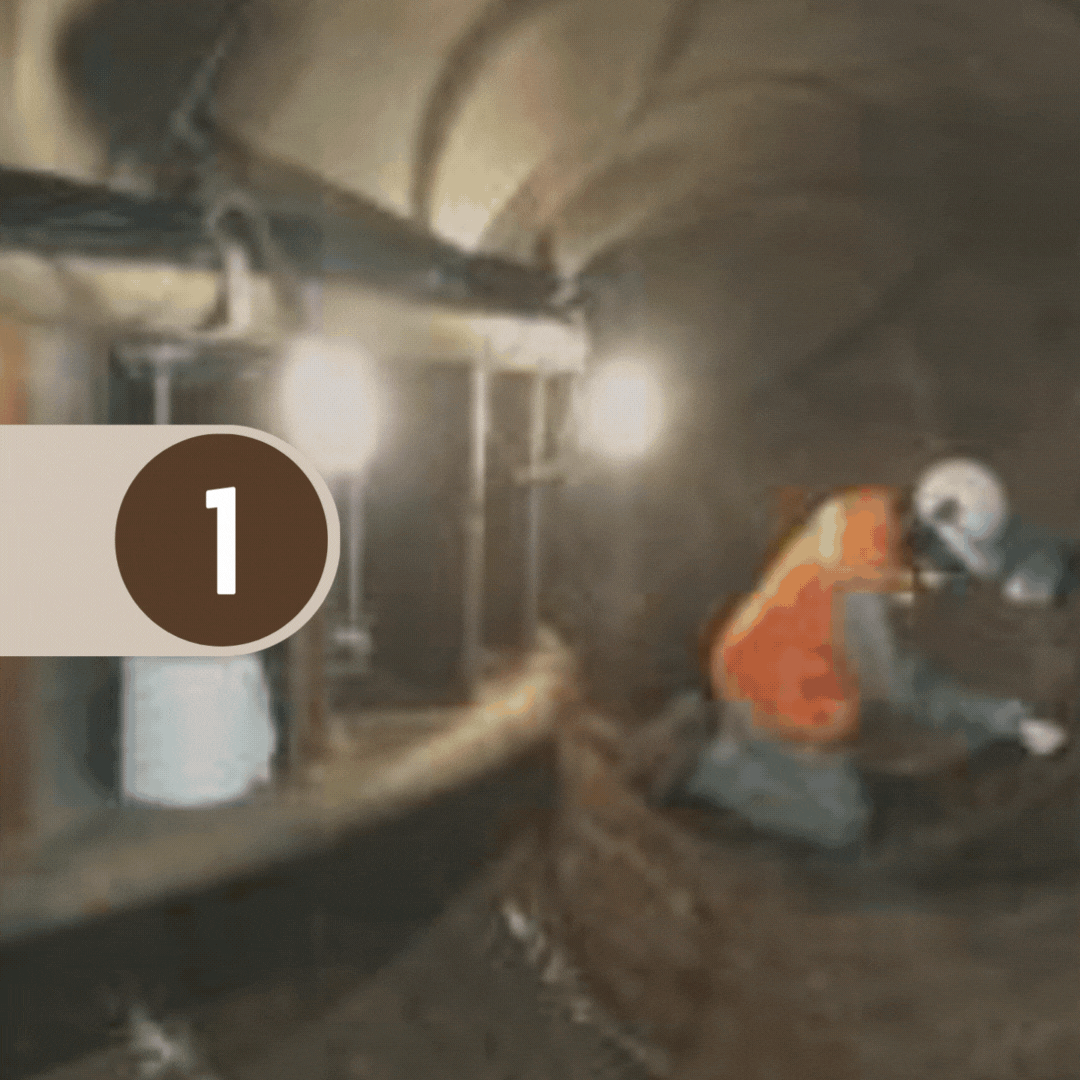
Case #2 – Francis Turbine Head Cover – Repair Erosion Damage
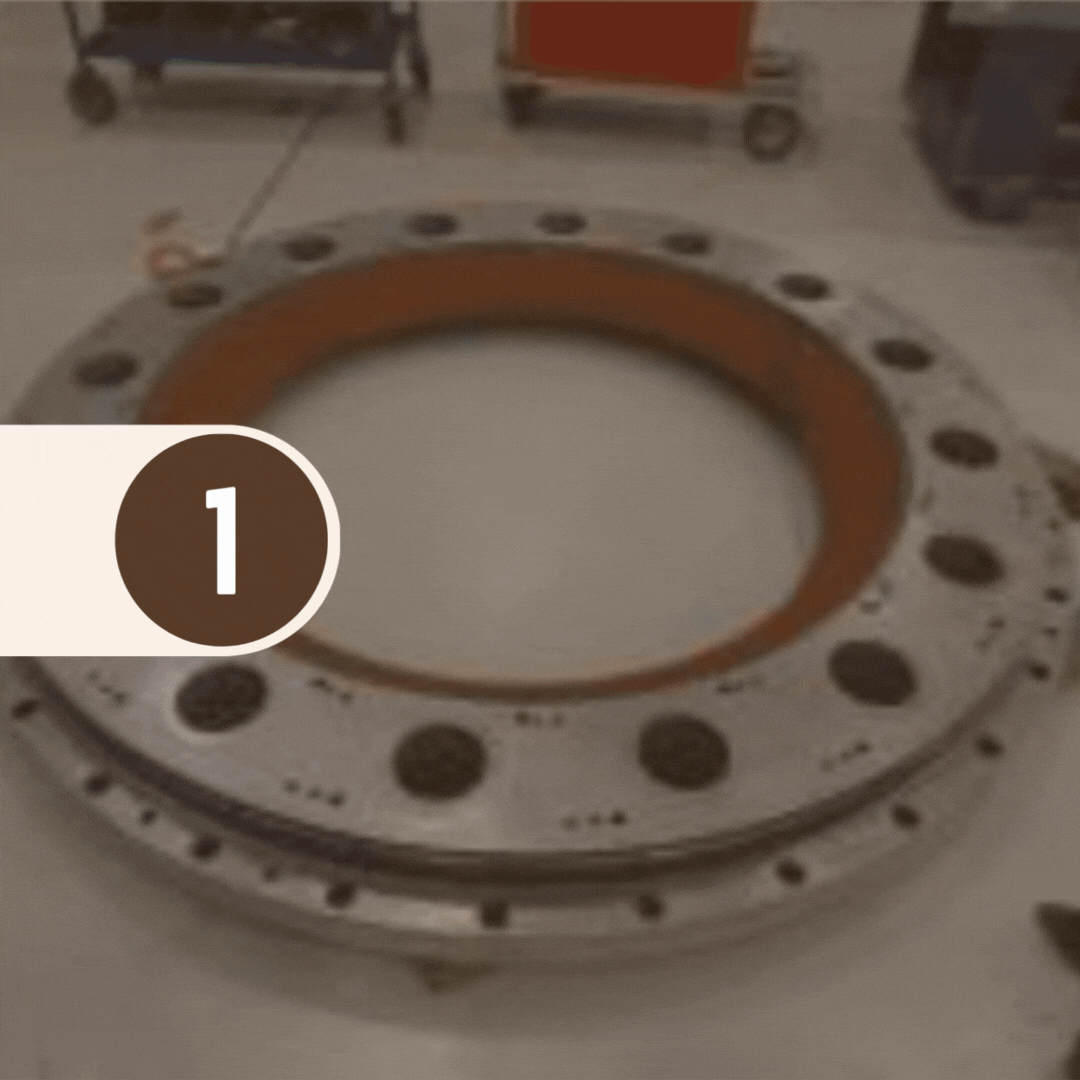
- Situation: Extreme erosion damage observed on the internal edge of the head cover at a small hydropower station.
- Solution: Rebuild the damage using 204 Heavy Duty Ceramic Paste and resurface with 202 Ceramic Repair Fluid.
- Application Details: Damaged face abrasive blast cleaned to SA2.5 with a 75-micron angular profile. 204 Heavy Duty Ceramic Paste applied to the maximum allowed thickness. Two coats of 202 Ceramic Repair Fluid applied to create a smooth, low-friction finish.
Case #3 – Turbine Head Cover – Corrosion Protection
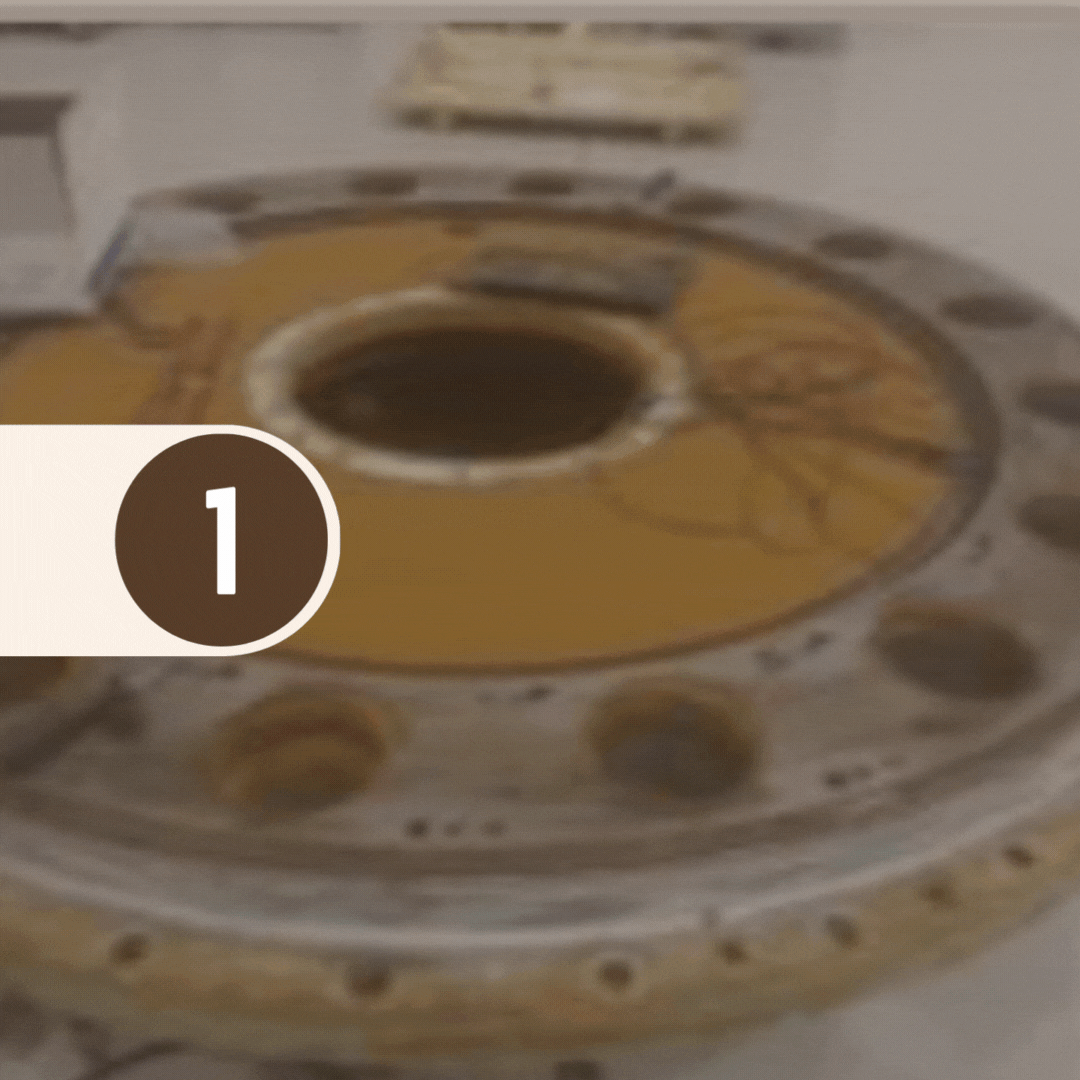
Case #4 – Stationary Throat Ring – Repair of Cavitation Damage
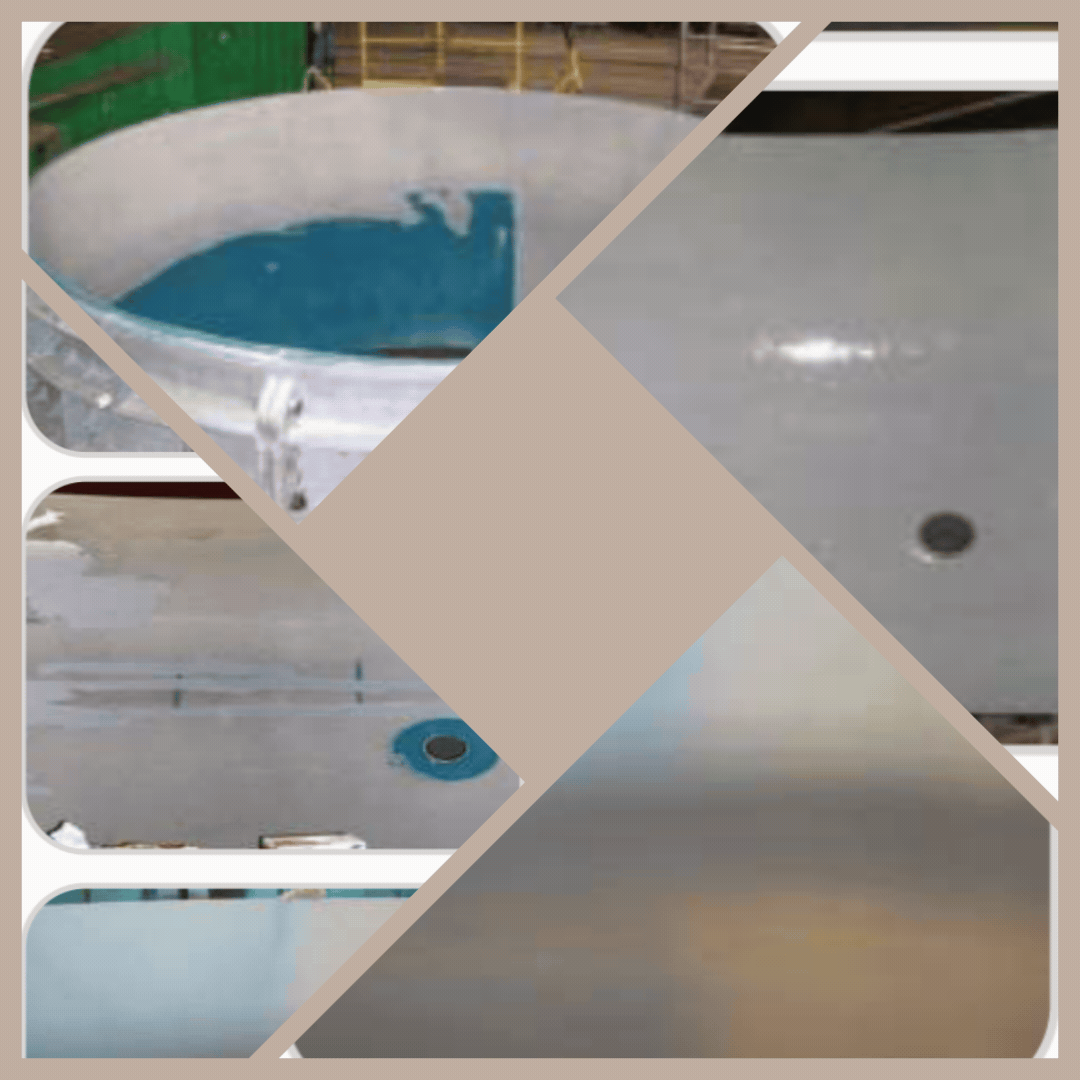
Case#5 – Scroll Case – Protect Against Corrosion
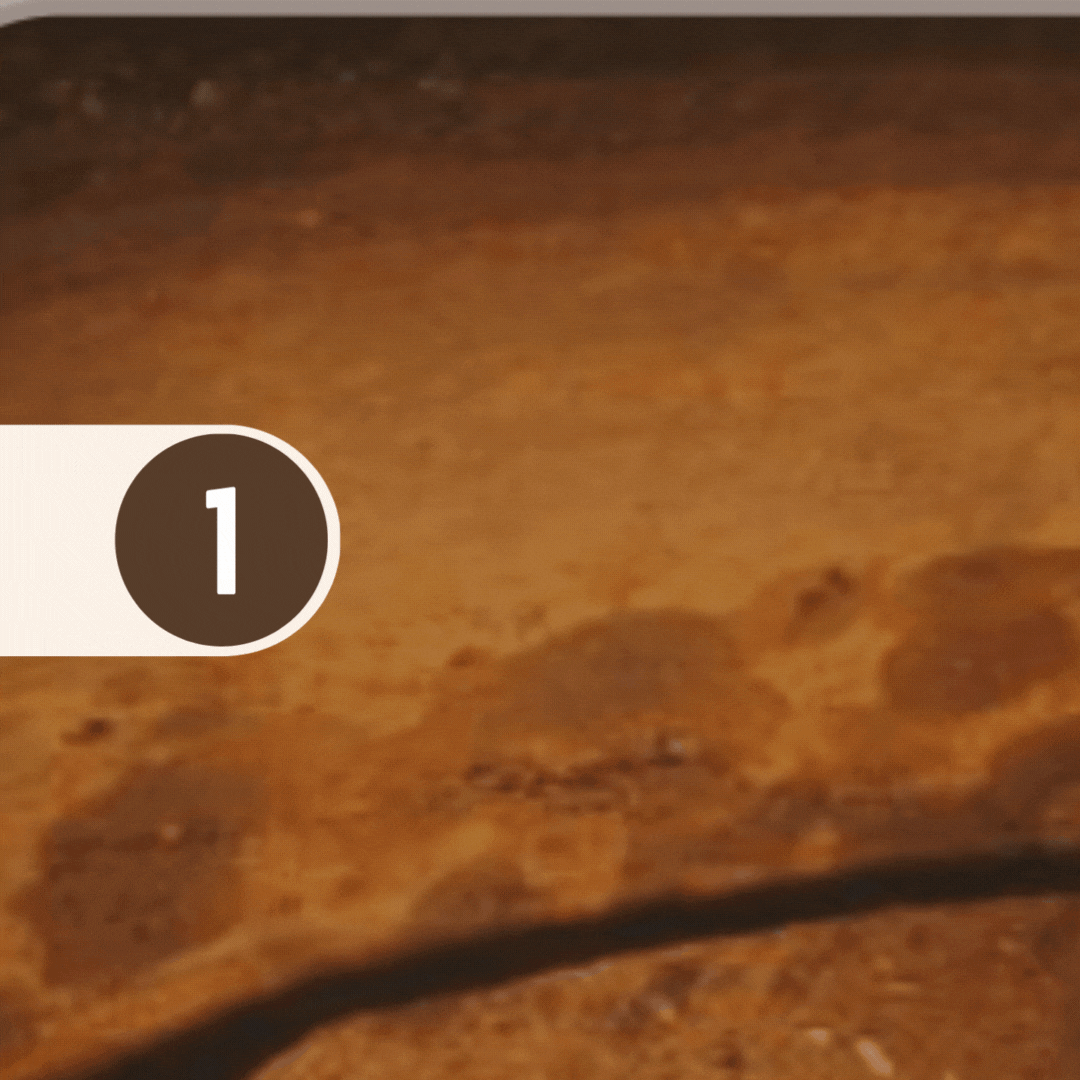
Enhanced Durability
Extends the lifespan of components by protecting against erosion and corrosion.
Cost Efficiency
Reduces maintenance costs and operational downtime by minimizing the frequency of repairs and replacements.
Improved Performance
Maintains the efficiency and reliability of hydropower systems by ensuring the integrity of critical components.
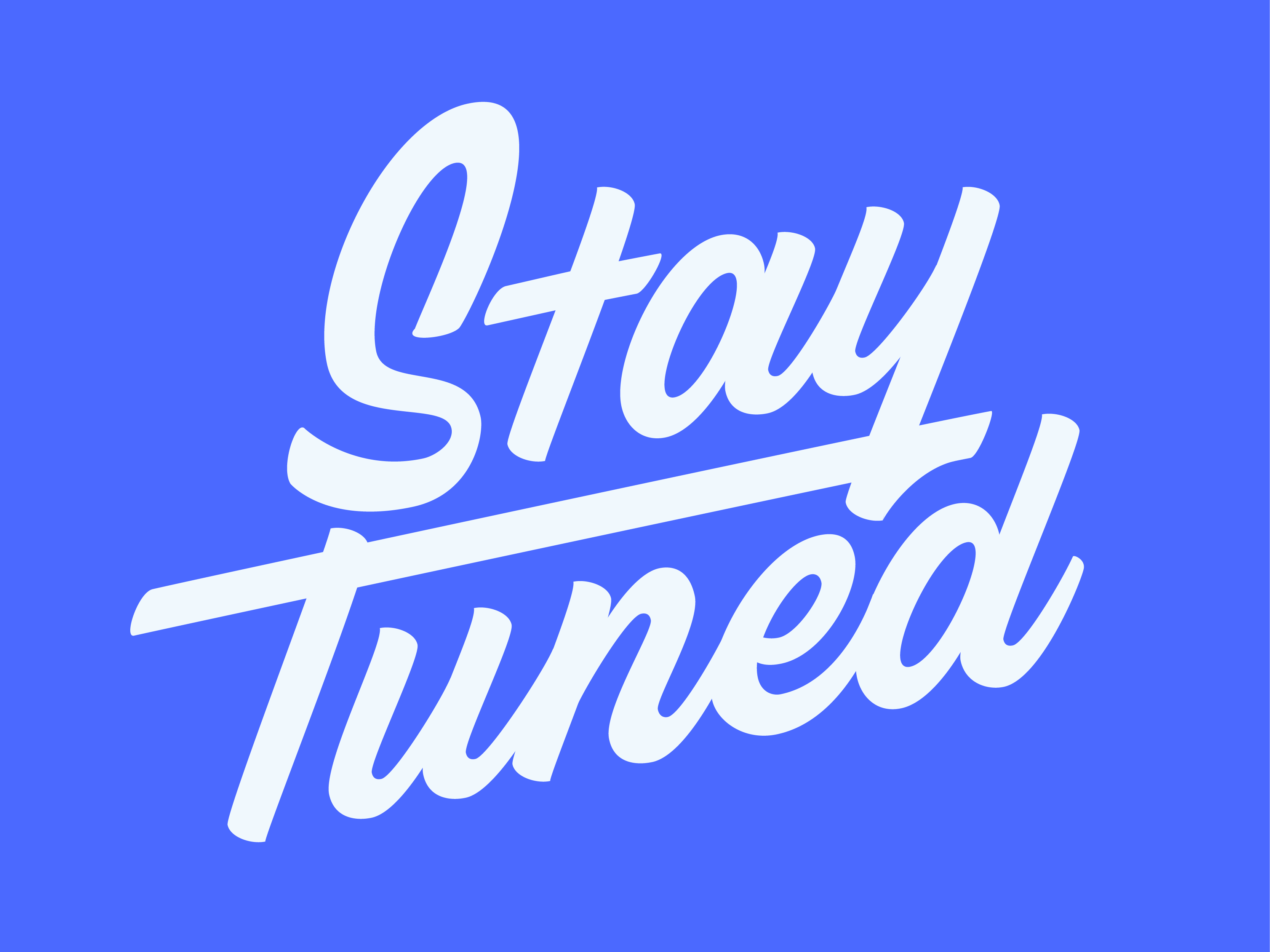