Resimac Solutions: Part 2 – Repair of Rotating Components in Hydropower Applications
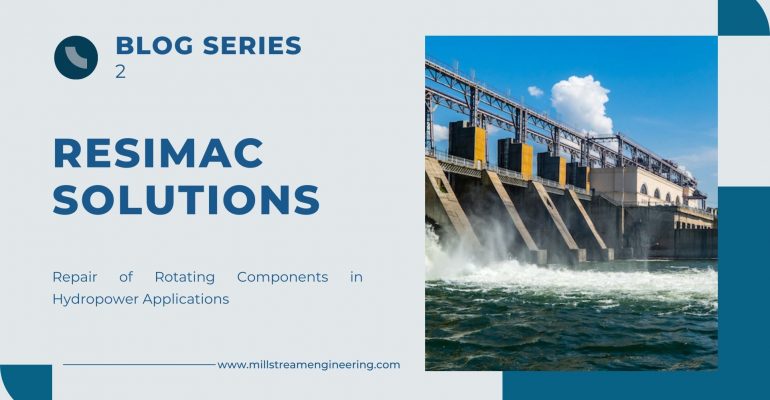
Resimac Solutions: Part 2 – Repair of Rotating Components in Hydropower Applications
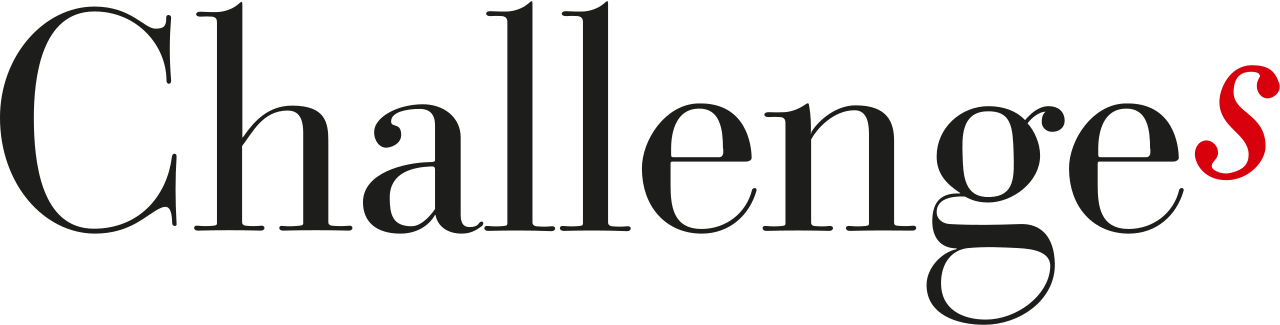
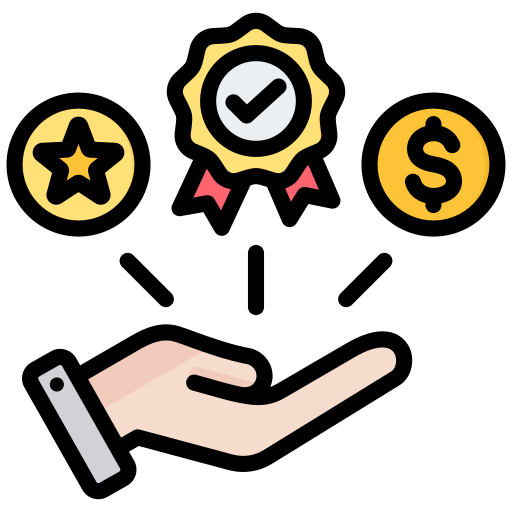
Case #1 – Kaplan Turbine Blades – Cavitation Repair
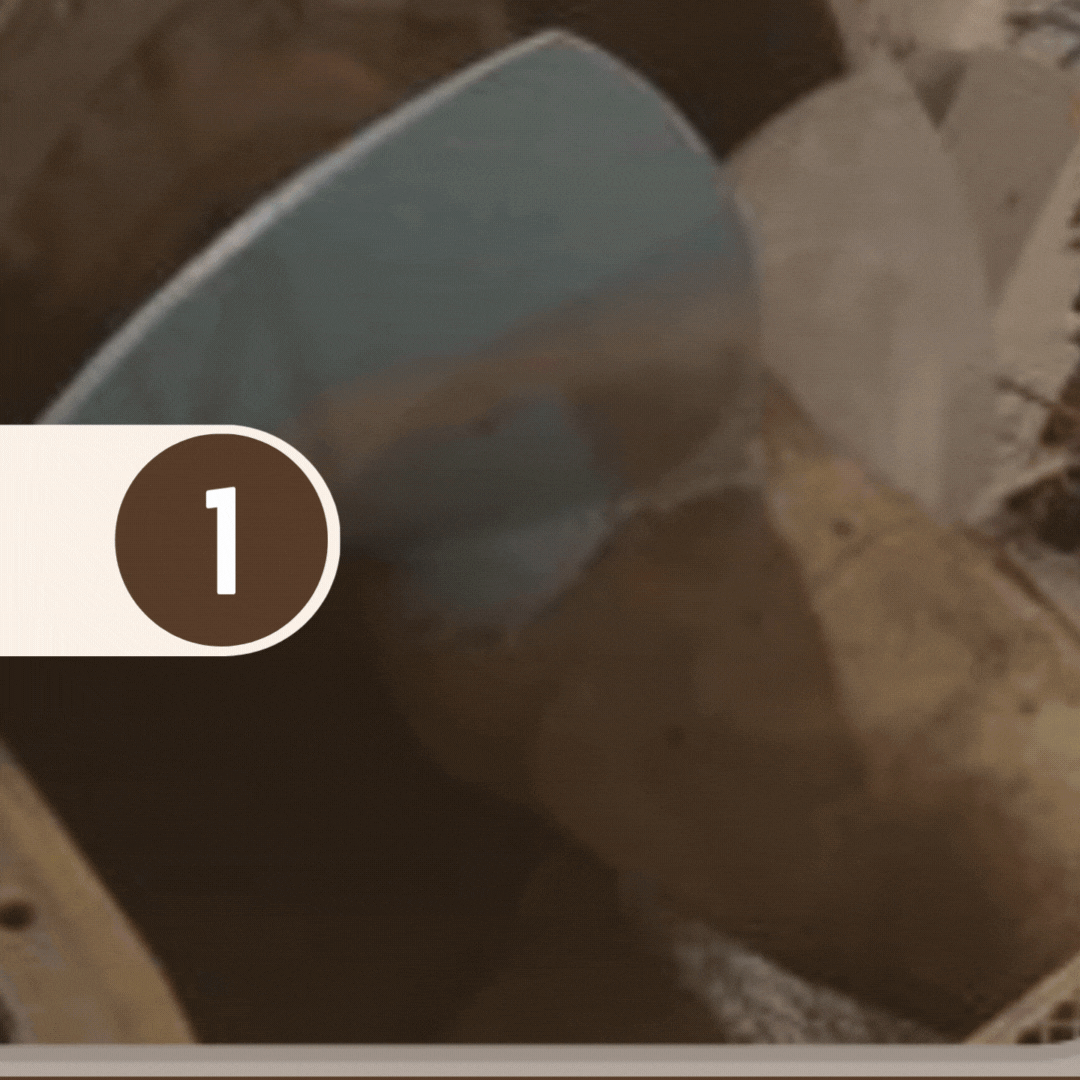
Case #2 – Kaplan Turbine Blades – Corrosion & Wear Repair
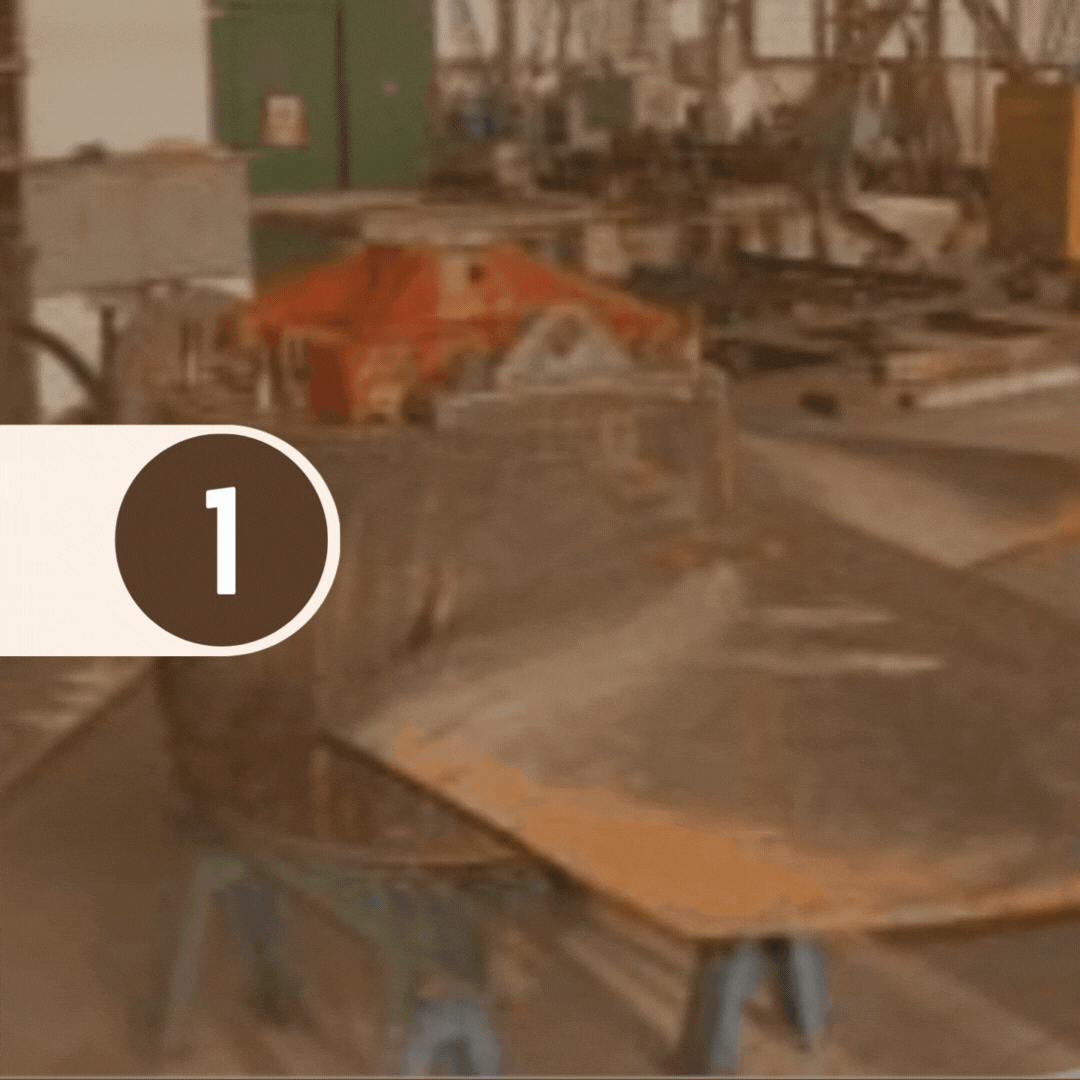
Case #3 – Francis Runners and Kaplan Runner Hubs – Pitting Repair
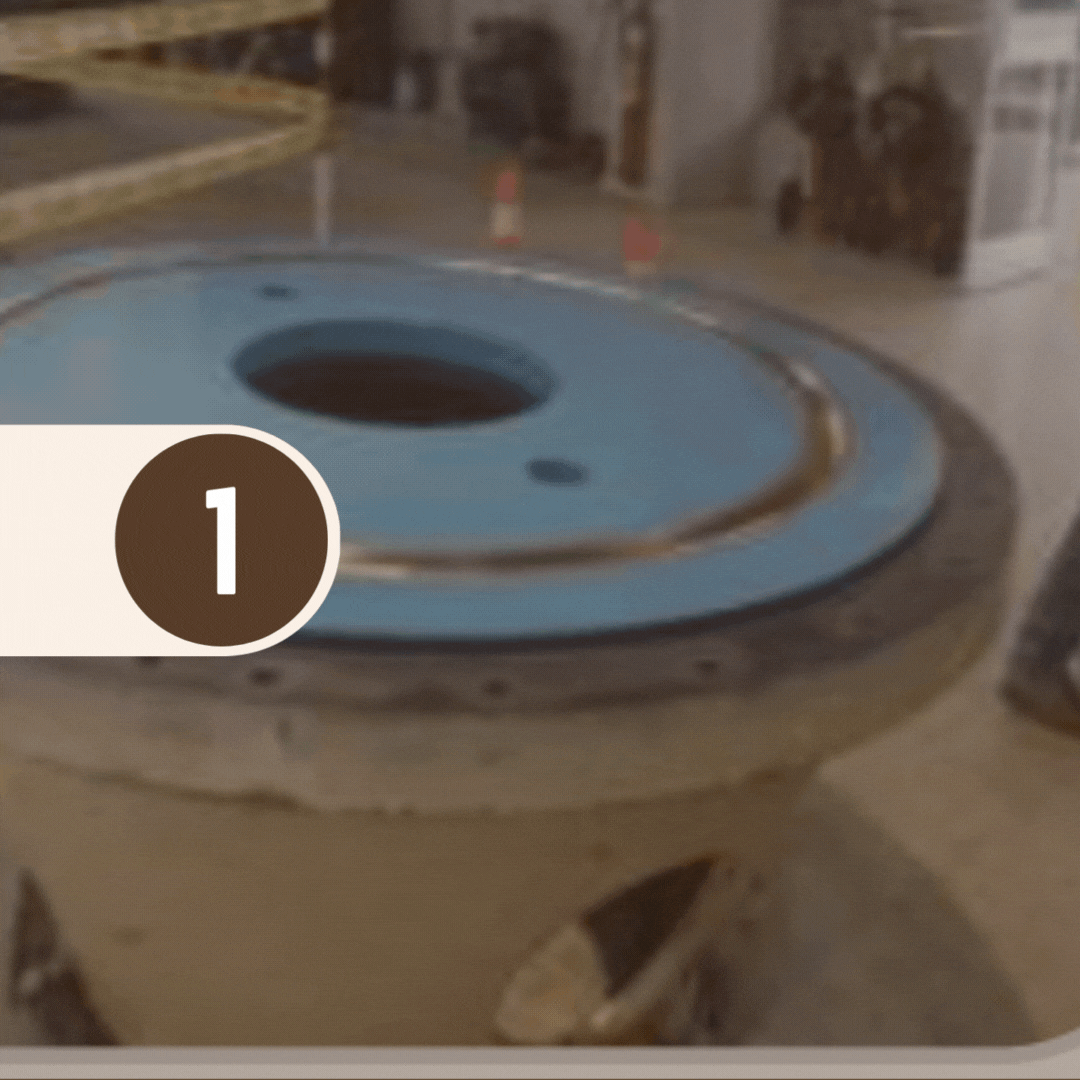
Enhanced Durability
Extends the lifespan of components by protecting against erosion and corrosion.
Cost Efficiency
Reduces maintenance costs and operational downtime by minimizing the frequency of repairs and replacements.
Improved Performance
Maintains the efficiency and reliability of hydropower systems by ensuring the integrity of critical components.
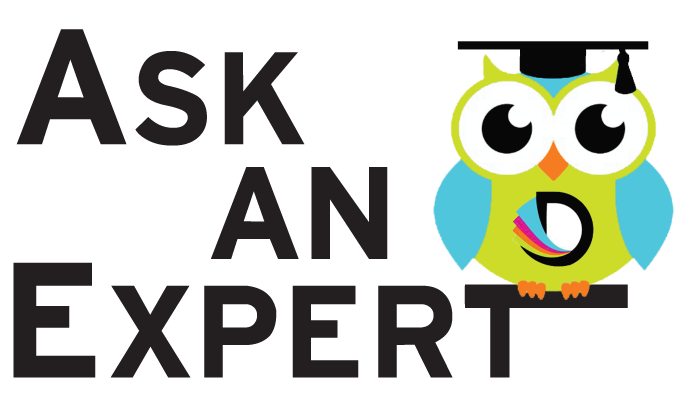
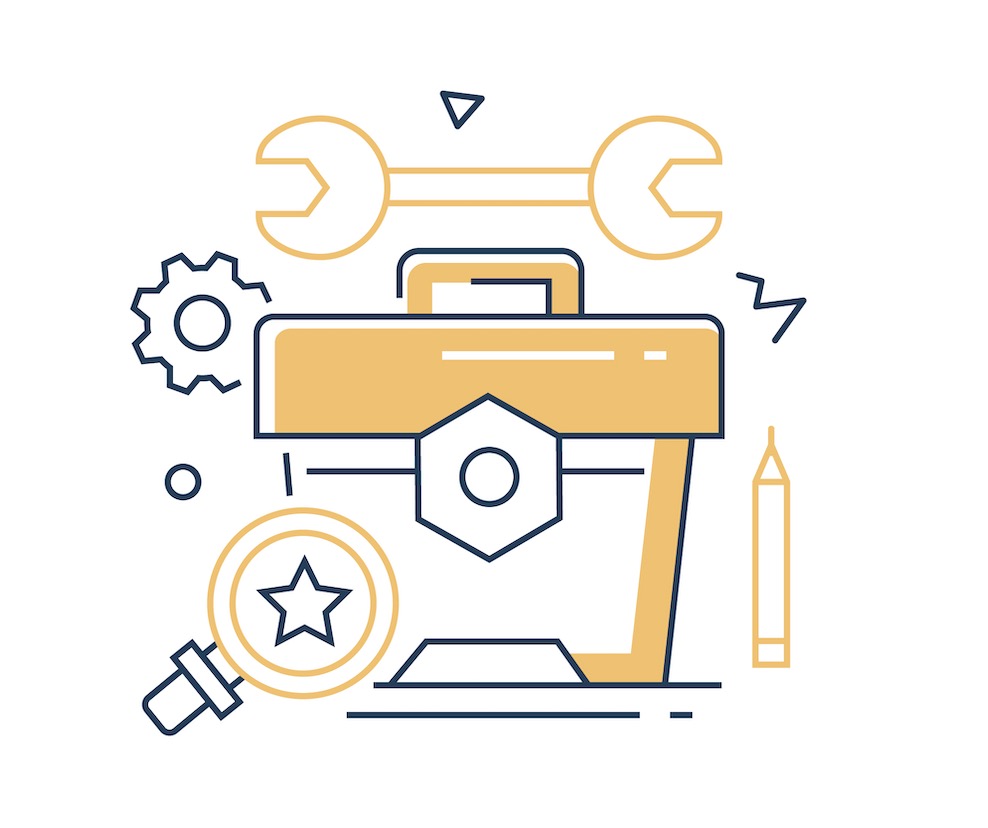