Resimac Solutions : Protection of Pumps and Valves Against Corrosion in Industrial Applications I
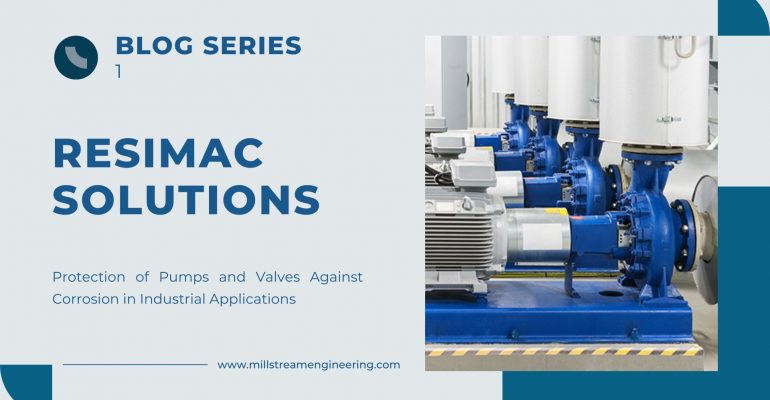
Resimac Solutions : Protection of Pumps and Valves Against Corrosion in Industrial Applications I
In industrial settings, pumps and valves are critical components that play essential roles in maintaining operational efficiency and reliability. However, these components are often exposed to harsh environments that can lead to corrosion, significantly impacting their performance and lifespan. In this blog post, the first in a two-part series, we will explore how Resimac’s advanced protective coatings and repair solutions can effectively safeguard pumps and valves from corrosion. Through real-world case studies, we’ll demonstrate the practical applications and benefits of these products across a variety of industries.
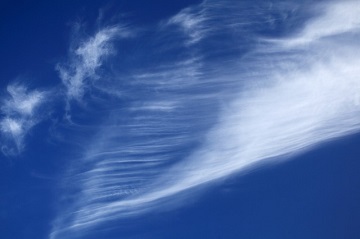
Corrosion is a major challenge for pumps and valves in industrial applications. It occurs due to chemical reactions between metal surfaces and environmental elements such as water, chemicals, and air. This process can cause material degradation, leading to leaks, reduced efficiency, and ultimately, equipment failure. Understanding the mechanisms of corrosion and implementing effective protection strategies are crucial for maintaining the integrity and performance of these components.
Case 1# Split Case Pump Housing – Repair of Worn Interior Surface
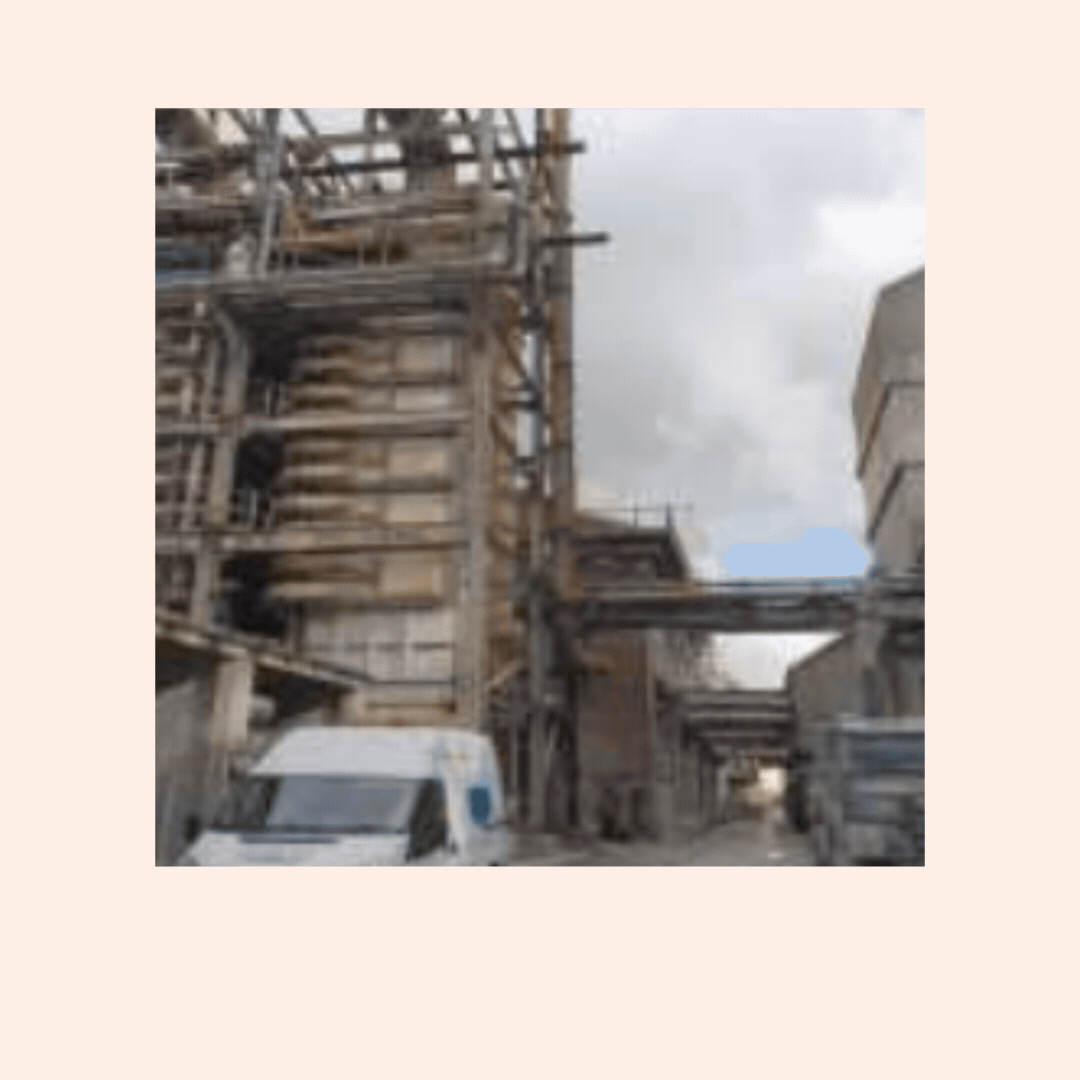
- Situation: An aged pump housing at a water plant in Ecuador required refurbishment to prevent further wear and enhance efficiency.
- Solution: Prepare the substrate, rebuild damaged sections with 101 Metal Repair Paste, and coat and protect with 202 Ceramic Repair Fluid.
- Application Details: The internal surfaces of the pump housing were abrasive blasted to produce a 75-micron profile and a surface cleanliness of SA2.5. Pitted sections were rebuilt using 101 Repair Paste, then machined back to a smooth finish. Two coats of 202 Ceramic Fluid were applied by brush to a nominal 300 microns dry film thickness per coat.
Case 2# Displacement Pump – Repair & Protect Lobes
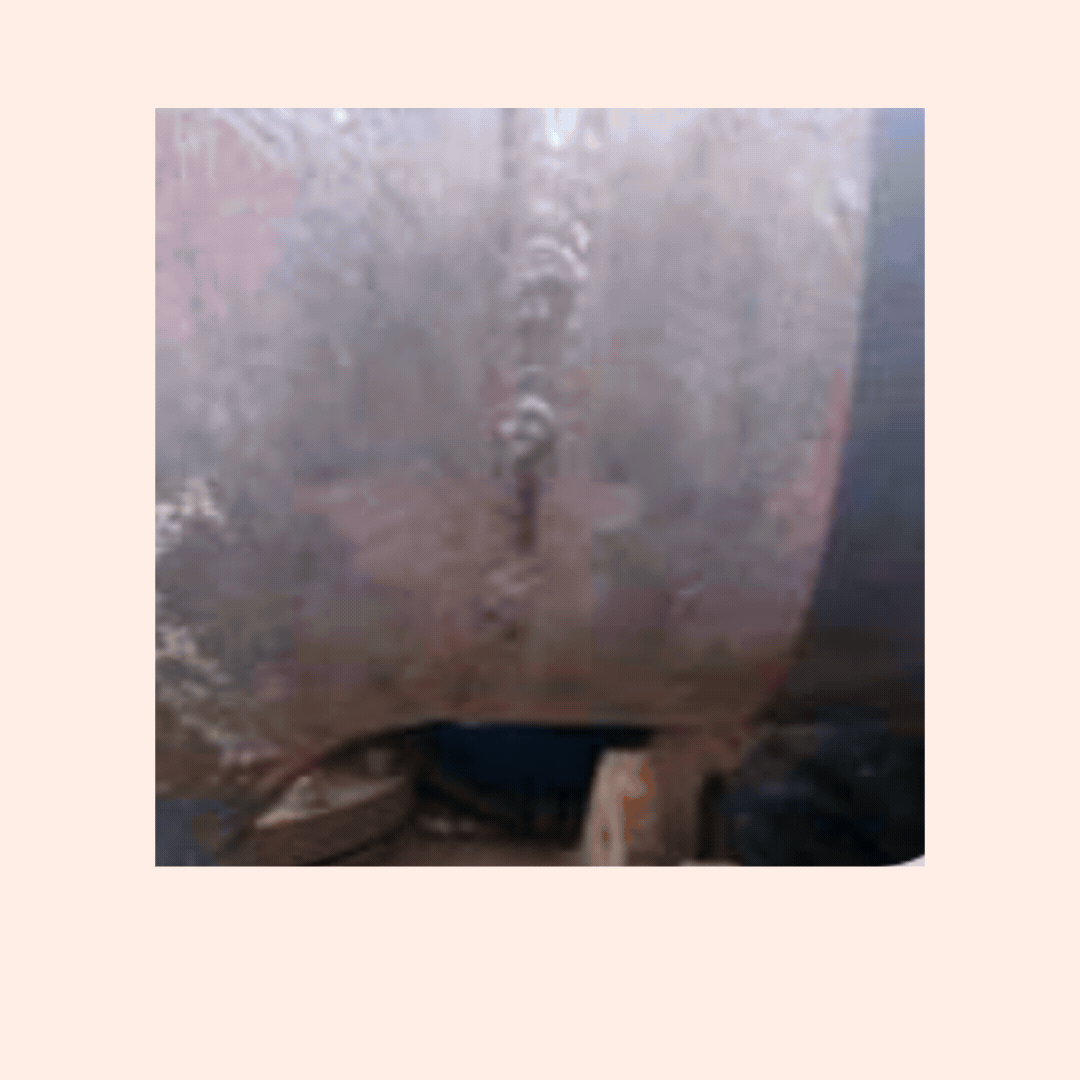
- Situation: A lobe displacement pump at a water treatment facility needed repair and protection to restore its maximum operating efficiency.
- Solution: Disassemble the unit, prepare the surface, rebuild with 101 Repair Paste, and protect with 203 Super Flow.
- Application Details: The lobes were abrasively grit blasted to create an SA2.5 surface cleanliness with a 75-micron profile. Erosion damage was rebuilt with 101 Repair Paste. The surfaces were then protected with two coats of 203 Super Flow to a total dry film thickness of 500 microns.
Case 3# Centrifugal Pump – Saltwater Corrosion Repair
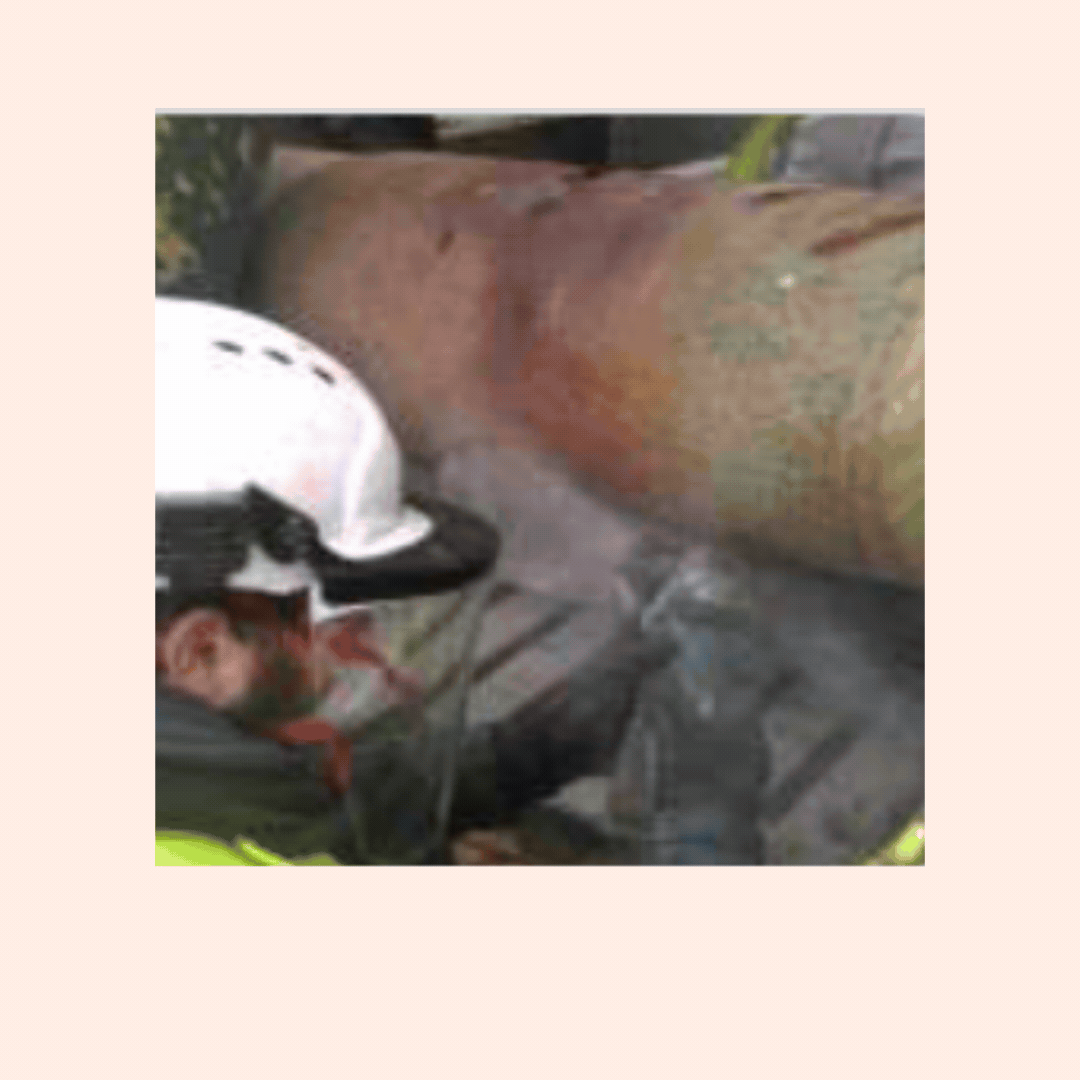
- Situation: A seawater pump in Portugal required total refurbishment with abrasive-resistant coating for the internals and a corrosive-resistant solution for the external.
- Solution: Prepare the surface by abrasive blast cleaning, rebuild with 201 Ceramic Paste where required, coat and protect internals with 202 Ceramic Fluid, and external surface with 501 CRSG.
- Application Details: Internal pitted sections of steel were rebuilt with 201 Ceramic Paste. The interior was then coated with two applications of 202 Ceramic Fluid, applied by brush at a nominal 350 microns per coat. The external surfaces were treated with two coats of 501 CRSG to protect against corrosion.
Case 4# Butterfly Valve – Corrosion Protection
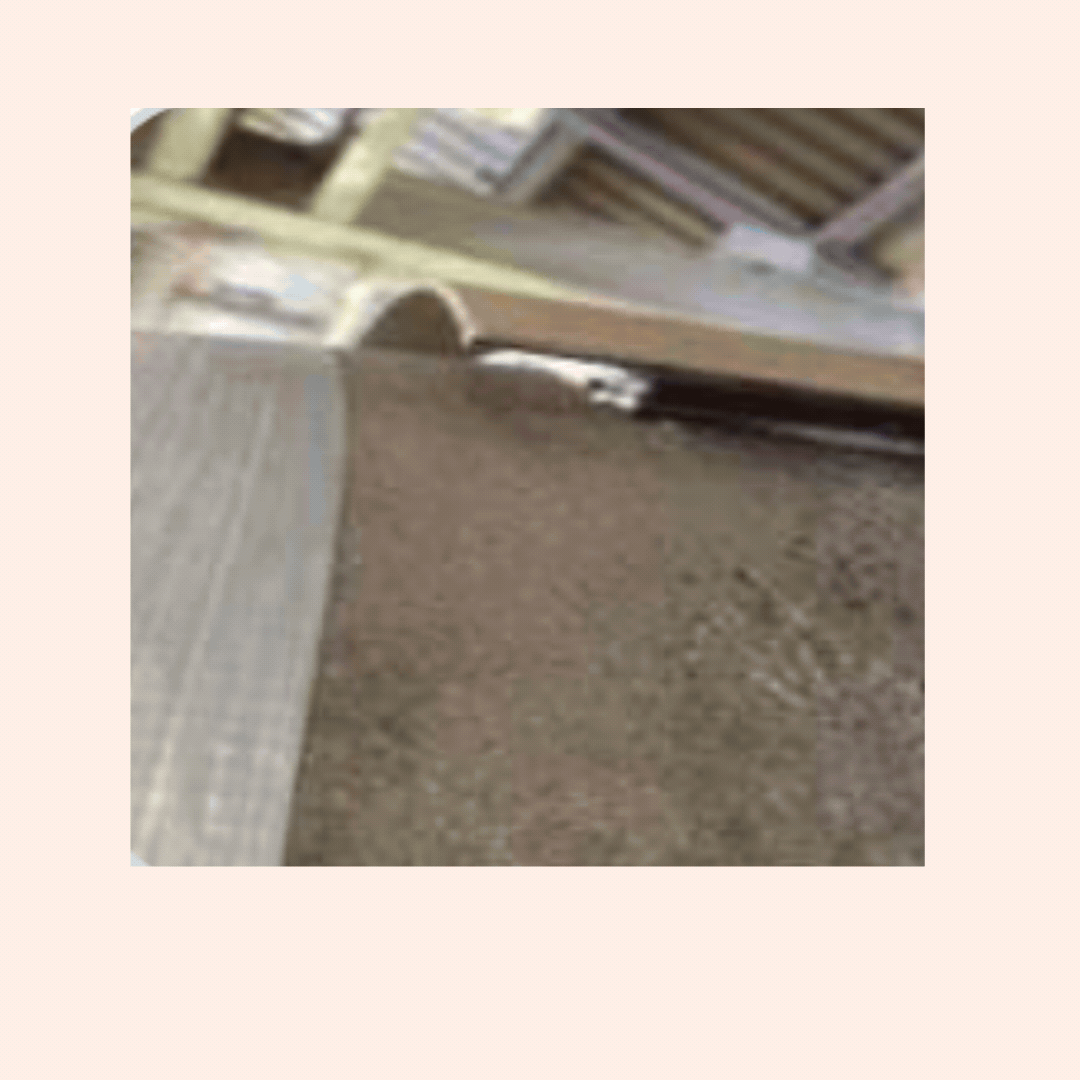
- Situation: New valves at a nuclear plant in Fujiang Province, China, required corrosion protection before operation.
- Solution: Brush apply two coats of 202 Ceramic Repair Fluid at 350 microns per coat.
- Application Details: The valve pipe internals were prepared by abrasive blasting to SA2.5 with a minimum angular blast profile of 75 microns. The surfaces were cleaned and degreased before applying two coats of 202 Ceramic Repair Fluid.
Case 5# Butterfly Valve – Improve Chemical Resistance
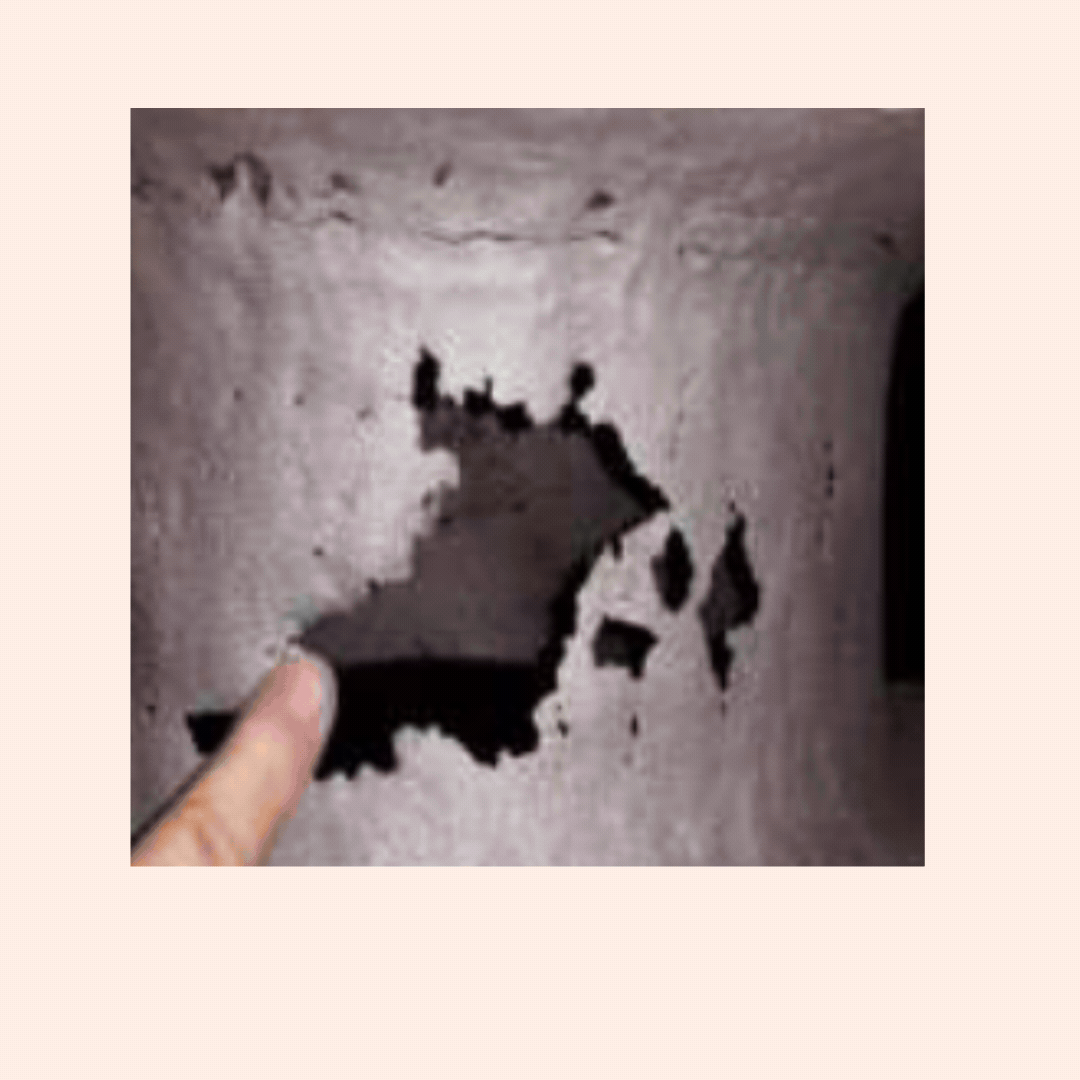
- Situation: A butterfly valve in a Mexican chemical processing plant required a protective coating to prevent future wear and extend its operating life.
- Solution: Prepare the surface and protect with 203 Super Flow.
- Application Details: The valve was abrasive blast cleaned to SA2.5 with a 75-micron profile. The surface was coated by brush with two applications of 203 Super Flow to produce a nominal total dry film thickness of 500 microns.
Case 6# Seawater Valve – Erosion and Corrosion Protection
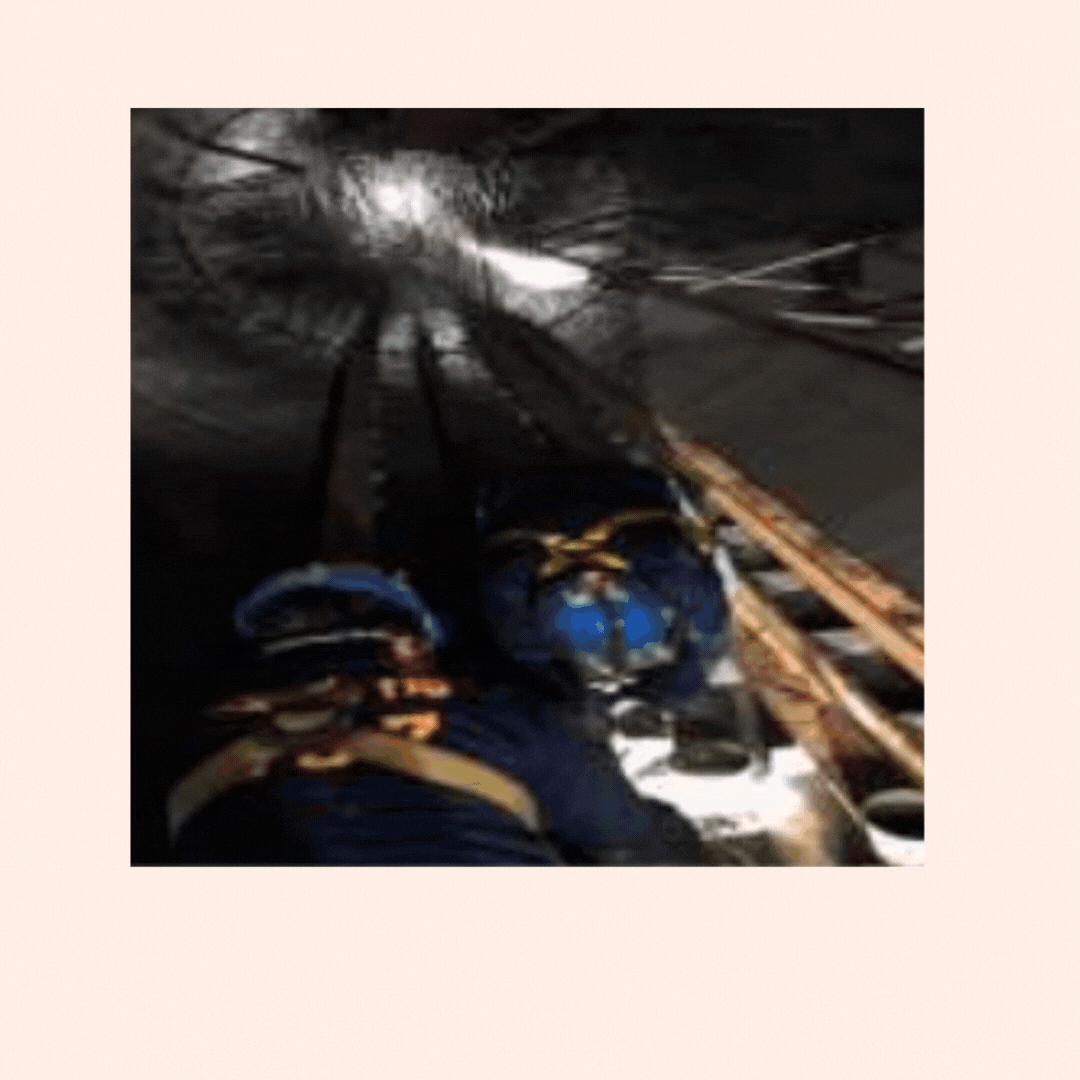
- Situation: A vessel seawater valve required a protective coating to prevent erosion and corrosion damage.
- Solution: Prepare the substrate and protect with 203 Super Flow.
- Application Details: The internal brass substrate was abrasive blast cleaned to SA2.5 with a 75-micron angular profile. The internal lining was protected with two coats of 203 Super Flow, applied at a nominal 300 microns per coat.
Using Resimac’s protective coatings and repair solutions offers numerous benefits for industrial pumps and valves:
- Enhanced Durability: Extends the lifespan of components by protecting against corrosion.
- Cost Efficiency: Reduces maintenance costs and operational downtime by minimizing the frequency of repairs and replacements.
- Improved Performance: Maintains the efficiency and reliability of industrial systems by ensuring the integrity of critical components.
Protecting pumps and valves against corrosion is essential for maintaining optimal performance and extending the lifespan of industrial equipment. Resimac’s advanced protective coatings and repair solutions provide effective and durable protection, ensuring that these components remain in excellent condition.
Stay tuned for our next blog post
where we will focus on the repair of leaking or damaged pipes and tanks. We will share detailed case studies, application-specific examples, and comprehensive content that highlights the transformative impact of Resimac Solutions in various industrial settings. Don’t miss out on these insights to see how our innovative solutions can address your unique operational challenges.
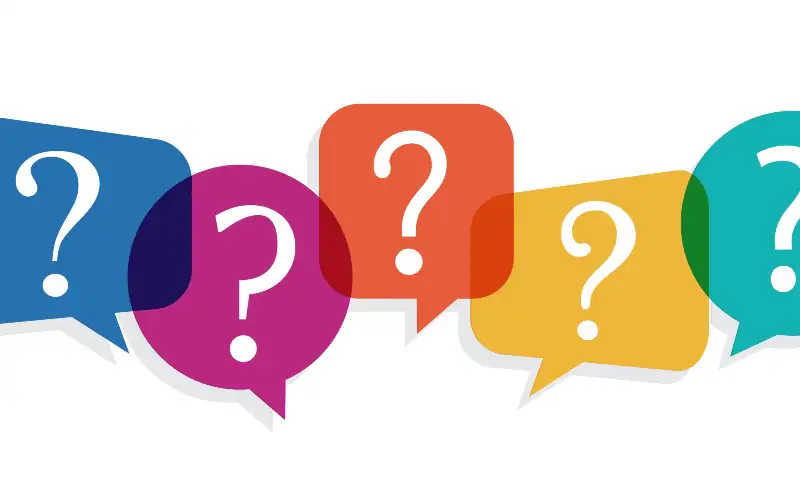
If you have any questions or are interested in exploring Resimac’s solutions for your industrial applications, don’t hesitate to contact Millstream Engineering for more information.