Resimac Solutions for Industrial Applications: Repair of Leaking or Damaged Pipes and Tanks II
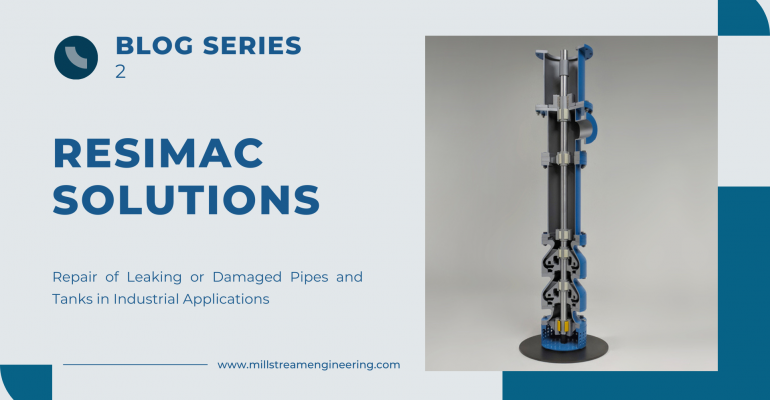
Resimac Solutions for Industrial Applications: Repair of Leaking or Damaged Pipes and Tanks II
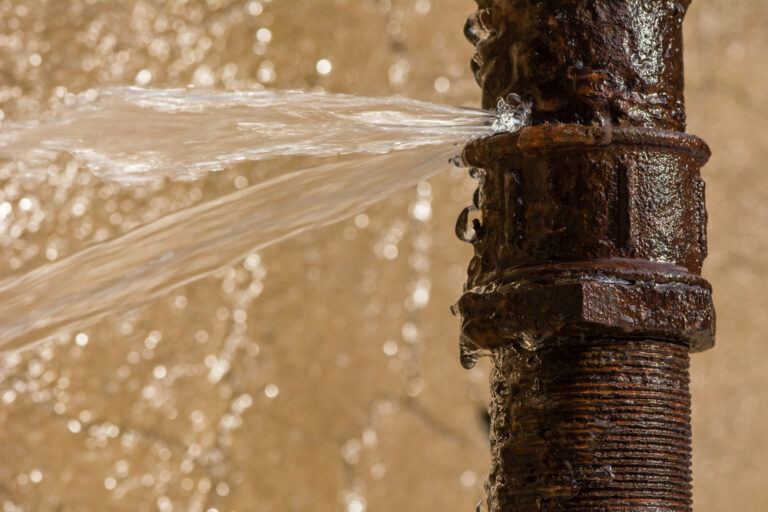
Leaking or damaged pipes and tanks pose significant challenges across various industrial settings. These issues can lead to operational downtime, safety hazards, and increased maintenance costs. In this second part of our blog series, we will explore how Resimac’s advanced repair solutions can effectively address leaks and damage in industrial pipes and tanks. Through detailed case studies, we’ll demonstrate the practical applications and benefits of these products in different industrial scenarios.
Leaks and damage in pipes and tanks can occur due to various factors, including corrosion, mechanical wear, environmental stress, and improper maintenance. These issues can compromise the integrity and efficiency of industrial systems, leading to costly repairs and operational disruptions. Effective repair and protection solutions are essential to maintain the functionality and safety of these components.
Case 1# Cooling Water Pipes – Repair of Weakened Wall Sections
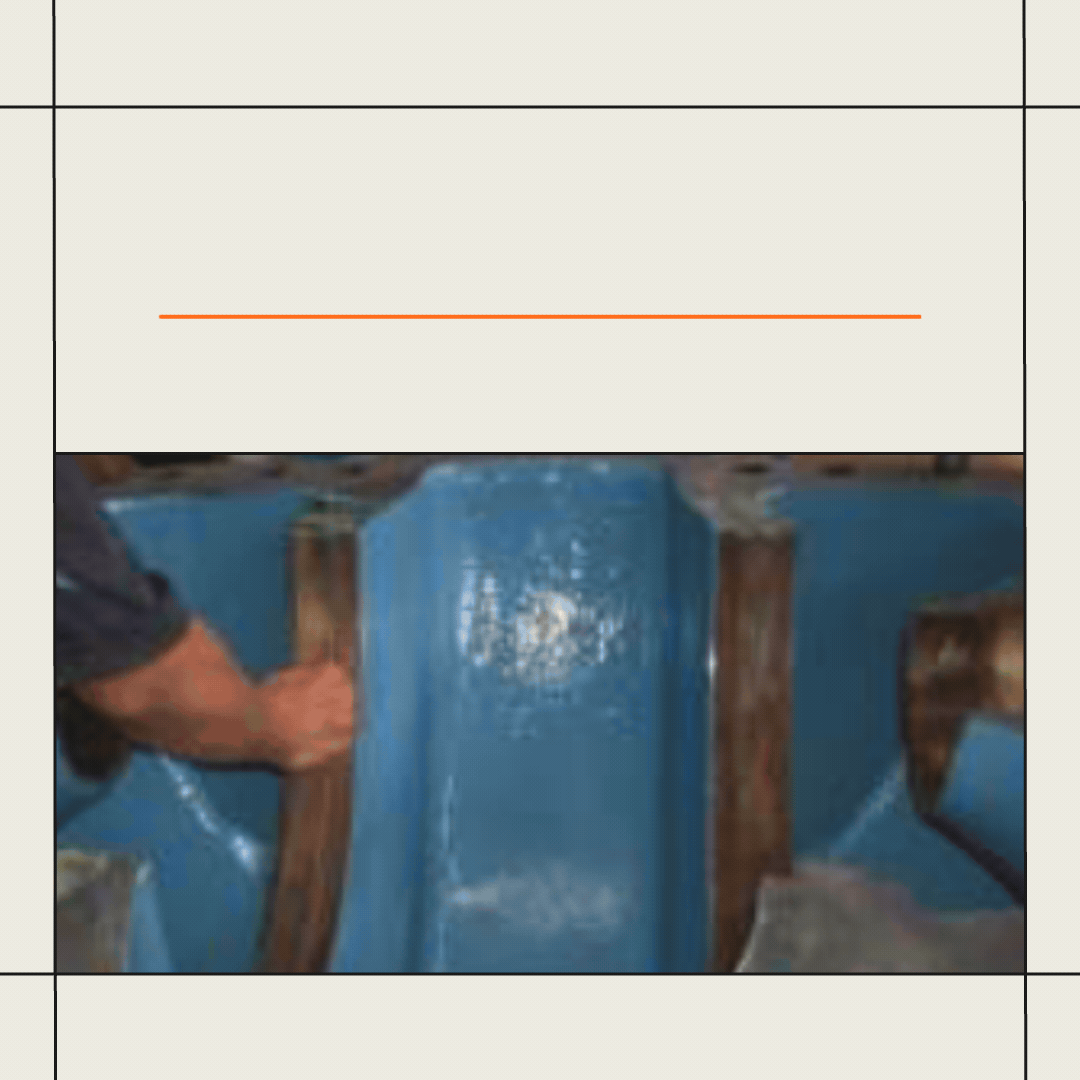
- Situation: Inspection of a water cooling system on the exterior of a UK manufacturing plant revealed heavy internal corrosion and low wall thicknesses in some areas of the pipework.
- Solution: Prepare the surface with mechanical hand tools, rebuild with 101 Paste with embedded reinforcement sheet, and resurface with 202 Ceramic Fluid.
- Application Details: Surface contaminants were removed, and the repair area was mechanically abraded. 101 Paste was applied at 1mm thickness, then reinforced with a layer of 808 reinforcing sheet, followed by another 1mm layer of 101 Paste. Once cured, the area was overcoated with 202 Ceramic Fluid to further protect and strengthen the repair.
Case 2# Steel Wastewater Pipe – Repair of Failed Weld Joint
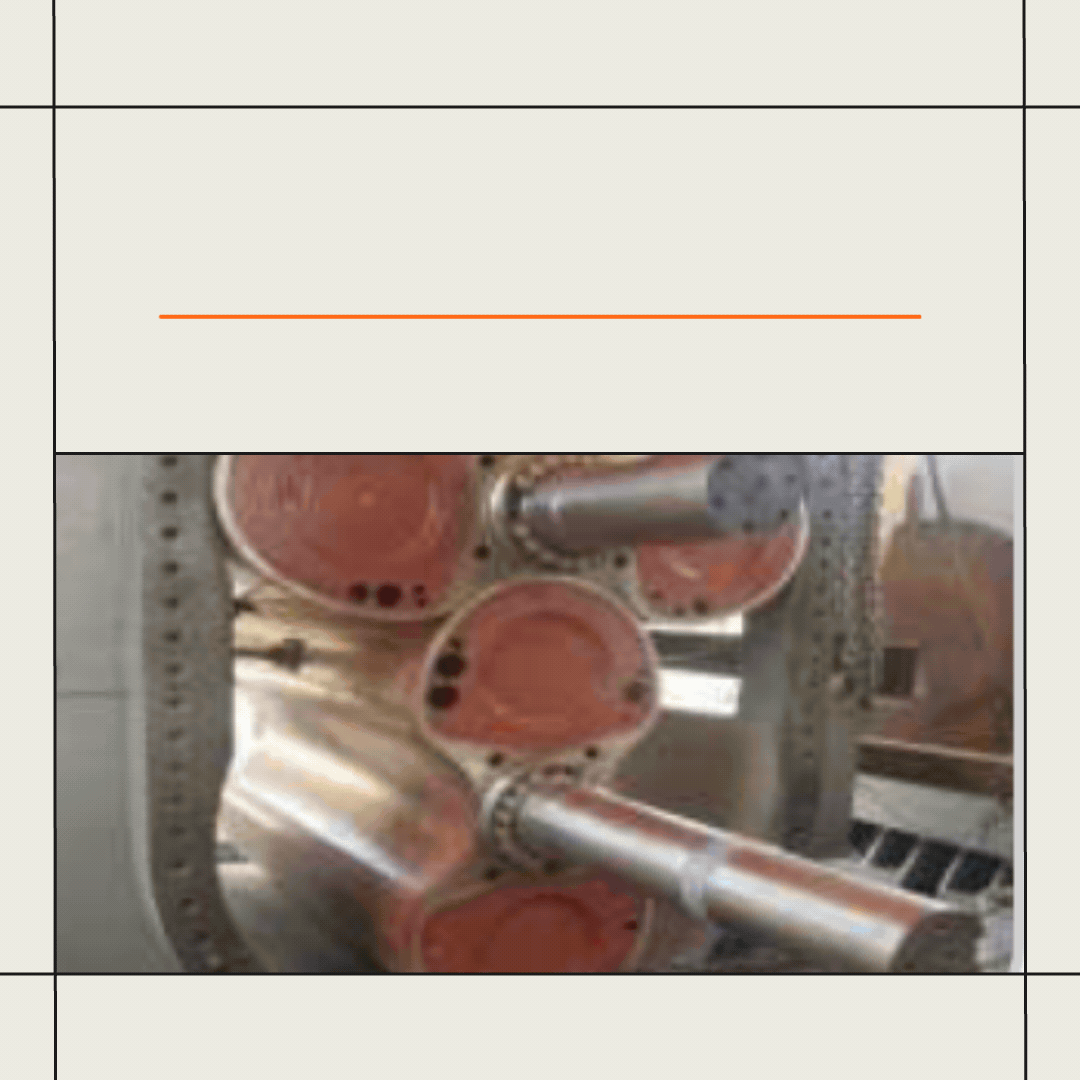
- Situation: A failed weld joint on a steel wastewater pipe.
- Solution: Plate bond with 101 Metal Repair Paste and encapsulate with glass tape reinforced 301 Epoxy Resin to withstand internal pressure and protect against further corrosion.
- Application Details: The pipework was taken out of service and drained of fluid. The substrate was abraded with mechanical grinders to ISO 8501/4 ST3. Both the substrate and a preformed steel plate were coated with 2mm of 101 Metal Repair Paste, then forced and held together until cured. The circumference of the pipe was coated with 301 Epoxy Resin and three layers of glass tape. The repair area was then overcoated with a final coat of 501 CRSG.
Case 3# GRP Chemical Process Piping – Repair of Leaking Section
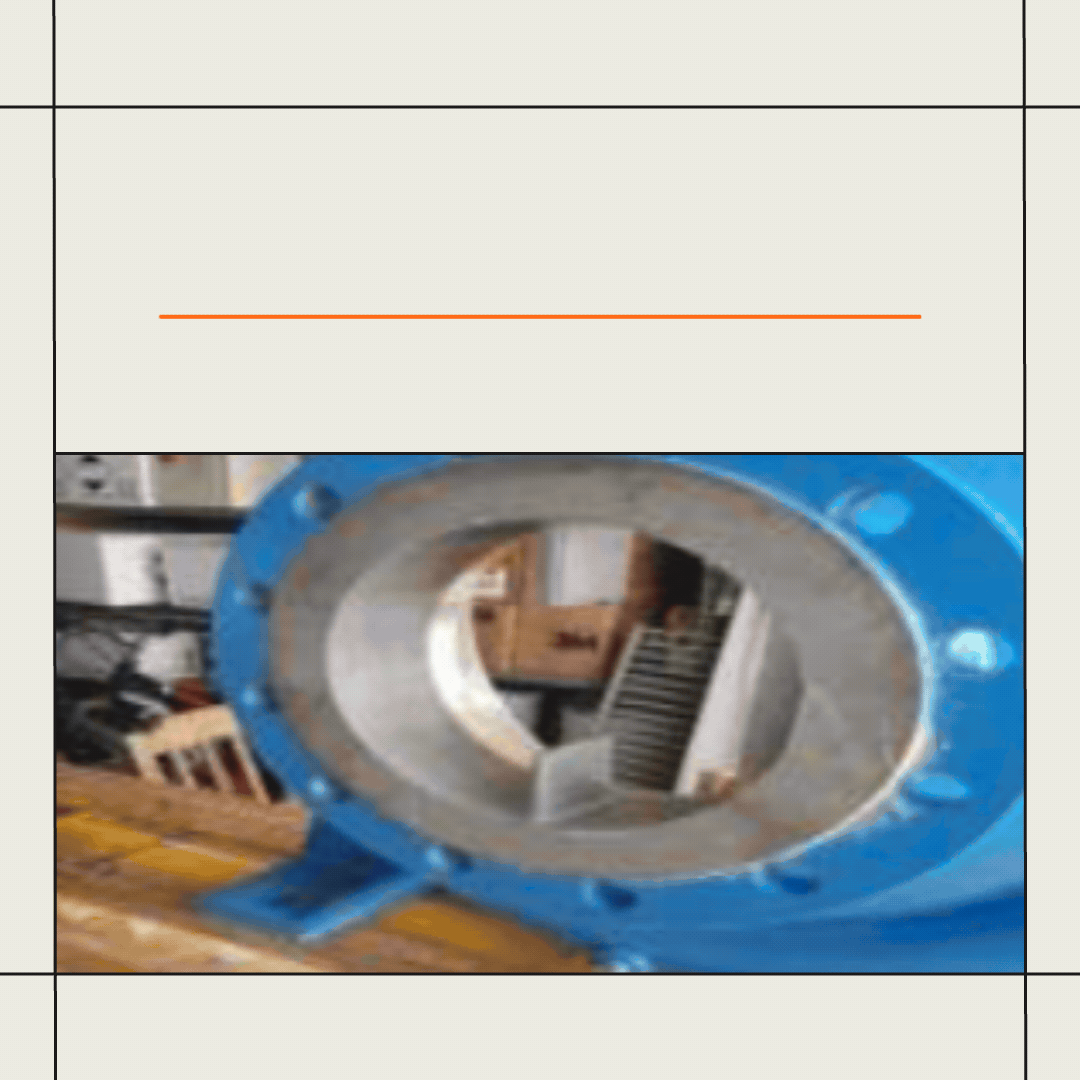
- Situation: A leaking section of GRP pipe in a chemical process line needed a rapid curing solution to minimize shutdown time.
- Solution: Prepare the surface and wrap with 108 Pipe Repair Tape.
- Application Details: The process line was shut down and the pipe drained of fluid. The repair area was abraded with hand-held mechanical tools and cleaned with MEK. Multiple 108 bandages were applied around the damaged section until an overall thickness of 12mm was achieved. The pipe was returned to service within 4 hours of the original shutdown.
Case 4# Steel Mill Pipeline – Corrosion & Leak Repair
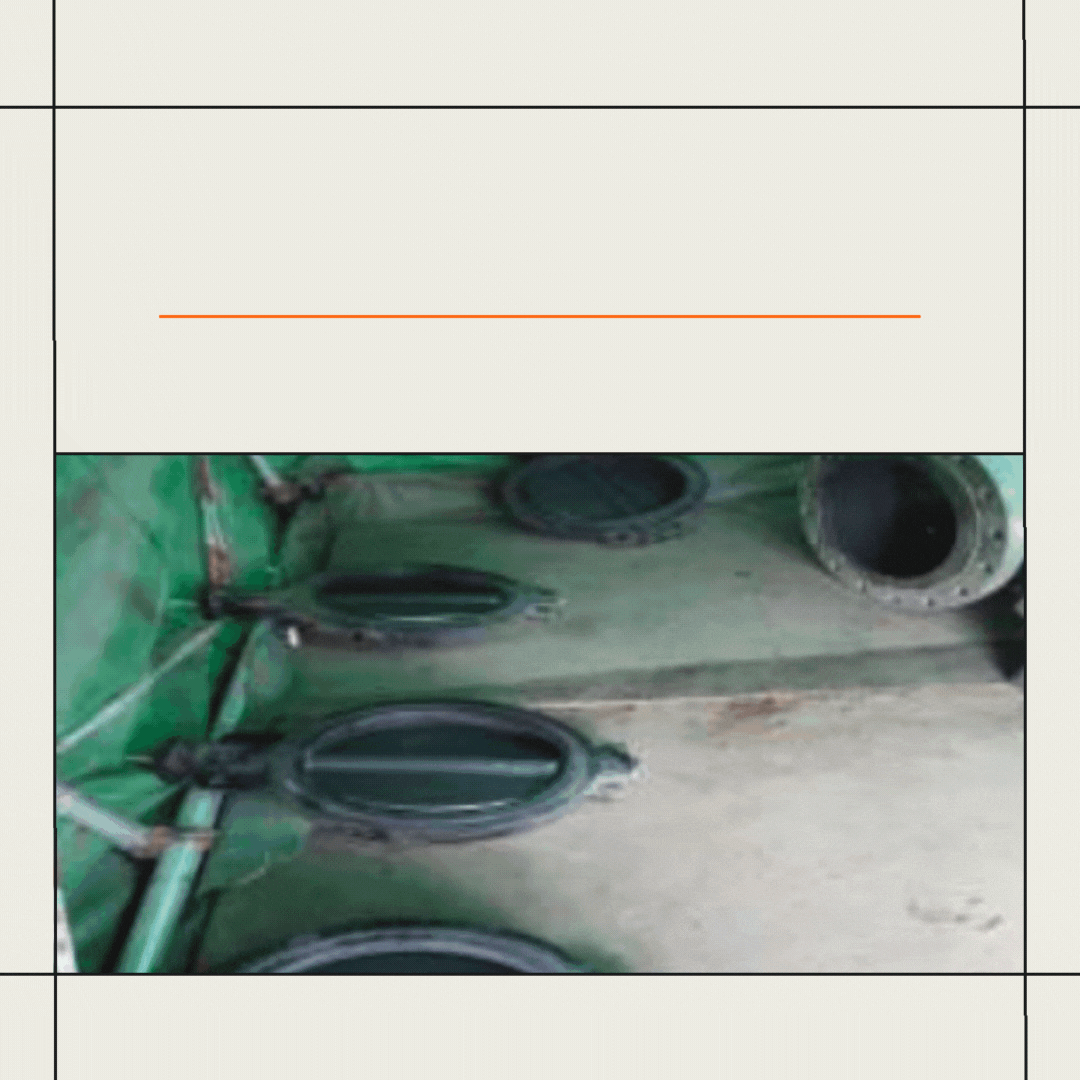
- Situation: A pipeline transporting fluid at 200psi was leaking due to heavy corrosion.
- Solution: Seal the leak by plate bonding with 101 Paste, then wrap with 301 Epoxy Resin and 701 Glass Tape.
- Application Details: The pipe was taken offline, and both the steel substrate and preformed steel plate were abrasive blast cleaned to SA2.5 with a 75-micron profile. 101 Paste was applied to both the damaged section and steel plate at a nominal 2mm thickness. Both surfaces were pressed together and held in place with clamps until cured. The repair area was coated with 301 Epoxy Resin and three layers of 701 Glass Tape, then overcoated with 501 CRSG for additional corrosion protection.
Case 5# Industrial Hopper Tank Nozzle – In-situ Repair
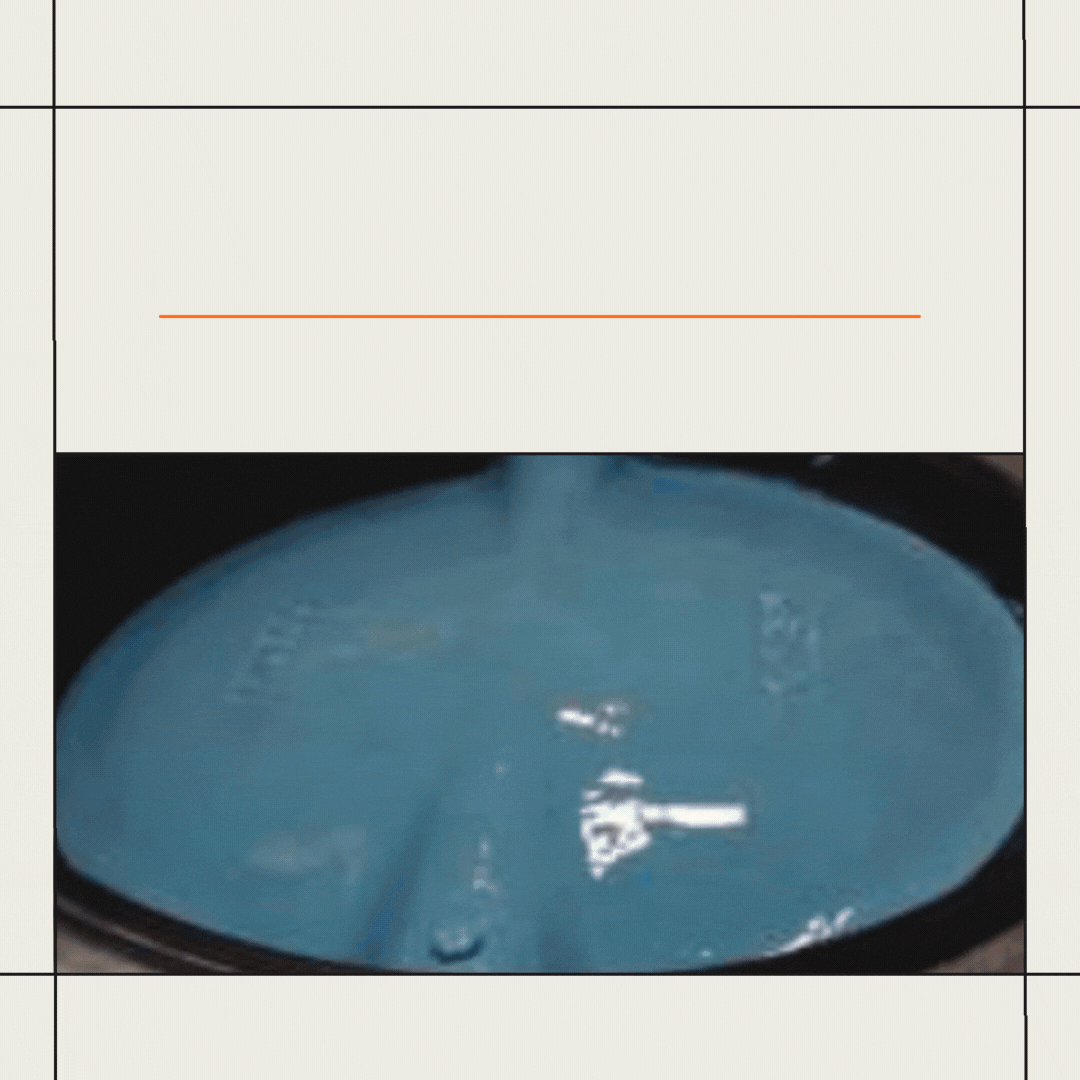
- Situation: The tank nozzle on the underside of an industrial hopper had become worn through and could not be replaced. The repair had to be carried out in-situ.
- Solution: Bond a preformed steel insert to the existing fitting using 101 Repair Paste.
- Application Details: A steel insert was manufactured from 2mm steel plate. The faces to be bonded were abrasive blast cleaned to SA2.5 with a 75-micron profile. 101 Repair Paste was applied to both surfaces, and the pieces were forced together. Once cured, the external face was overcoated with two coats of 501 CRSG for future external corrosion protection.
Case 6# Compressor Cooling Tank – Internal Corrosion Protection
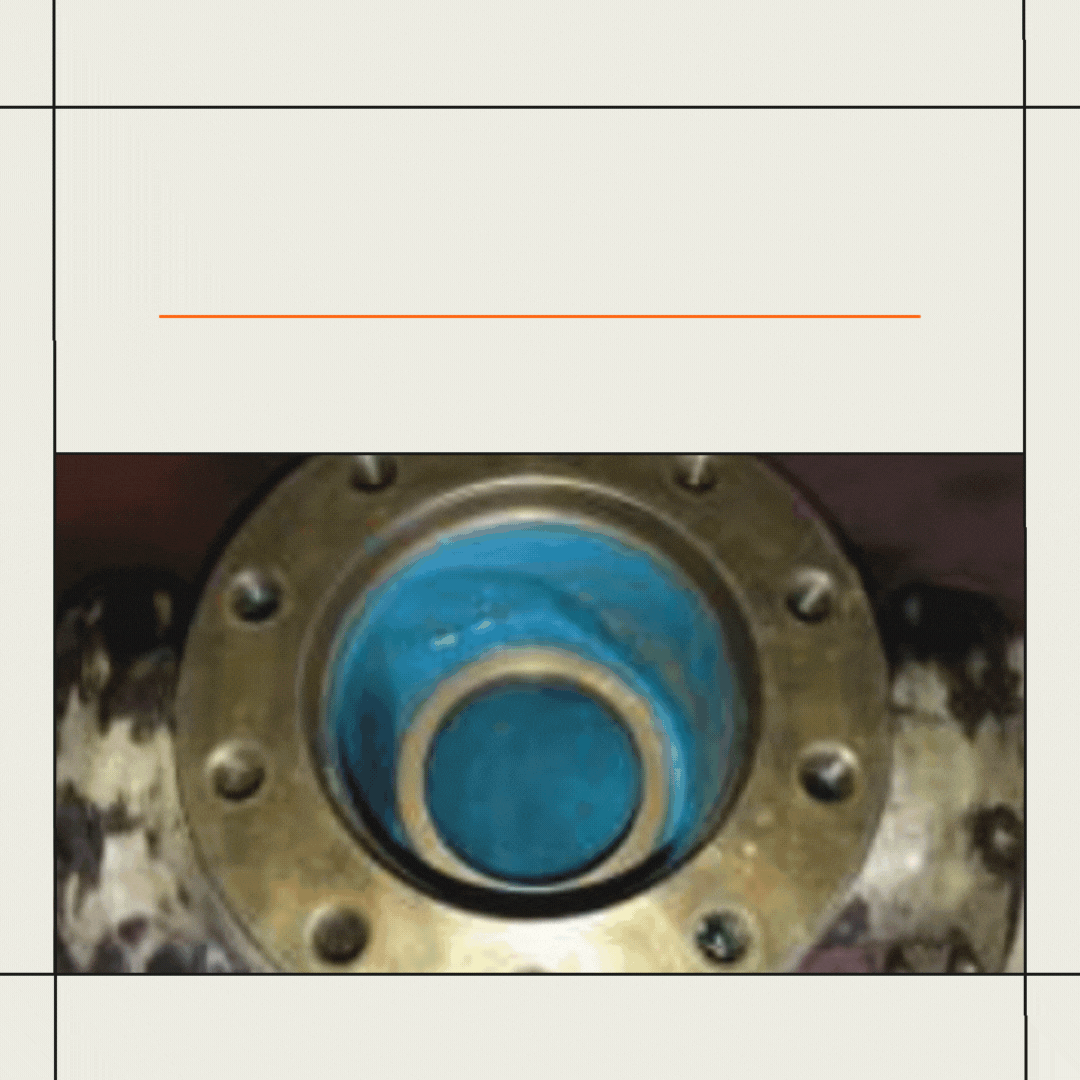
- Situation: An air compressor cooling tank was suffering from high levels of corrosion due to high humidity and operating temperatures (120°C).
- Solution: Prepare the surface and coat with two coats of Resimetal 205 HT Ceramic Fluid.
- Application Details: The tank internal was abrasive grit blasted to SA2.5 with a 75-micron surface profile. 205 HT was applied in two coats to a nominal 500 microns per coat, using plastic applicators and stiff-bristled brushes.
Resimac’s advanced repair solutions offer several benefits for industrial pipes and tanks:
- Enhanced Durability: Improved resistance to further damage and leaks.
- Restored Performance: Restoration of original component performance and safety.
- Cost Savings: Significant cost savings compared to component replacement, coupled with reduced downtime and maintenance requirements.

Repairing leaking or damaged pipes and tanks is crucial for maintaining the operational efficiency and safety of industrial systems. Resimac’s advanced repair solutions provide effective and durable repairs, ensuring these components remain in excellent condition.
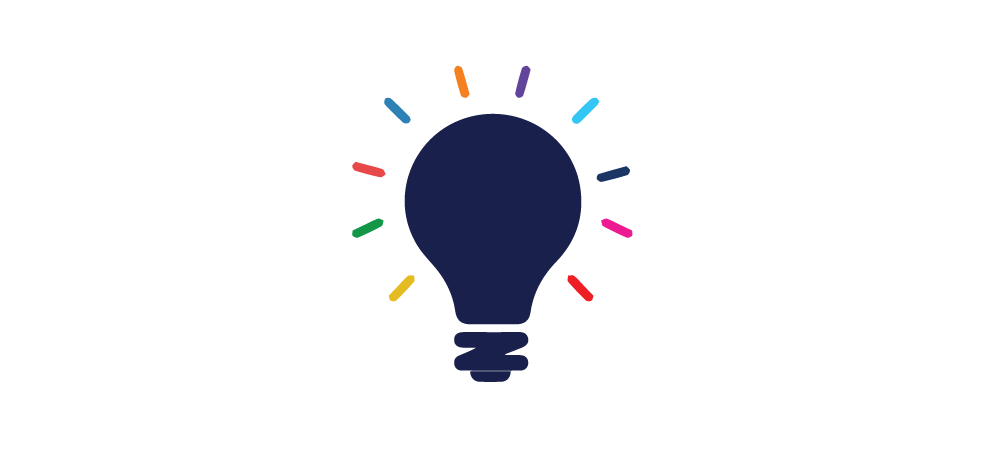
Stay tuned for future blog posts, where we will dig deeper into the technical specifications and benefits of Resimac’s product lines. We will share detailed case studies, application-specific examples, and comprehensive content that highlights the transformative impact of Resimac Solutions in various industrial settings. Don’t miss out on these insights to see how our innovative solutions can address your unique operational challenges.
If you have any questions or are interested in exploring Resimac’s solutions for your industrial applications, don’t hesitate to contact Millstream Engineering for more information