Thordon Industrial Solutions for the Forestry and Pulp & Paper Industries
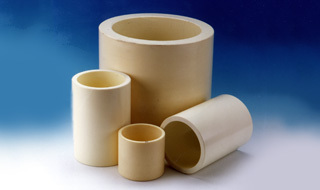
Thordon Industrial Solutions for the Forestry and Pulp & Paper Industries
Many manufacturing processes in the forestry and pulp & paper industries are subject to abrasive conditions. High temperatures, frequent impact loads, humidity, and corrosion are a few challenges that can cause traditional bushings to fail. Millstream Engineering provides creative engineering solutions and innovative products from a variety of brands including, Thordon Bearings Inc.
Thordon Bearings provides reliable, cost-effective non-metallic bearing solutions for a wide variety of industrial applications, including forestry and pulp & paper. They developed elastomeric polymer bearing solutions as ideal replacements for greased bushings, roller bearings and wear pads. Their innovative materials have been proven to:
- Eliminate grease and associated maintenance costs
- Enhance durability when subjected to vibration and shock loads
- Improve reliability and reduce downtime costs
- Provide superior abrasion resistance against other non-metallic materials
Here are 3 examples where Thordon Bearings’ solutions helped their customers in the forestry and pulp & paper industries solve operational challenges.
1. Replacing bronze bearings with ThorPlas-Blue bearings
In 2006, a customer came to Thordon with a challenge in their kiln drying process. The process created extremely high temperatures and humidity, so they required materials that could withstand these conditions. They were using bronze wheel bushings for their sawmill carrying containers, used to dry the loads of wood before further processing. The bronze bushings were exposed to temperatures up to 80℃ and more than 2000psi of bearing pressure. This resulted in a very short wear life of 2 months which they understandably were not satisfied with and hoped to improve.
Due to high temperatures and humidity conditions, Thordon recommended ThorPlas-Blue bearings to replace the bronze. ThorPlas-Blue bearings offer:
- Excellent performance in high impact load and high humidity conditions
- Long bearing wear life with no maintenance
- Excellent dimensional stability with low thermal expansion and water absorption
- Smooth operation without oil or grease
After replacing the bronze wheel bushings in this application, the ThorPlas-Blue bearings provided a minimum wear life of approximately 10 months; 5 times longer than that of the bronze.
2. Equipping Sawmill bumper bars with Thordon SXL elastomeric pads
Many Canadian sawmills sort their lumber using a mechanical arm that directs the lumber into appropriate bins. The sorter’s arm has a mechanical stopper which is often a piece of vulcanized rubber bonded to a steel pipe. In 2006, one of these sawmills came to Thordon looking for an alternative solution to their rubber bonded bumper, as it was being replaced every 4 weeks in some positions.
Thordon recommended their SXL elastomeric polymer as a direct replacement for the bumper pads because of the excellent resistance to impact, vibration, and ability to increase the pad wear life. This installation proved successful as the customer retrofitted all 30 bumper arms in their mill with Thordon SXL wear pads. These new wear pads provided a minimum wear life of 24 weeks, reducing the maintenance interval to twice per year instead of monthly with the rubber pads.
3. Using Thordon SXL Bearings to save monthly costs for paper recycling equipment
When it comes to recycling paper, the process can be quite tough on conventional bearings. Pulp is made from post-consumer waste mashed into a mixture of debris and water to filter out contaminants. At the end of the recycling process, the residue which may contain metal wires, glass, plastic, sand, water, and other waste products, is sent through a machine called a trammel which has internal baffles supported by conventional greased roller bearings. The bearings are often submerged underwater during the recycling process. In time, the waste products reach the bearings, damaging the seals, and the subsequent loss of the lubricating grease causes them to fail.
Cascades Canada Inc. has a large pulp and paper operation, based in Kingsey Falls, Quebec. They came to Thordon in December 2008 with this bearing problem in their process. Between replacing the $3,000 roller bearing, and losing 2 days of production, the disruption was costing the company up to $5,000 every six months. They installed Thordon’s SXL self-lubricated bearings which are resistant to abrasive conditions and do not require any greasing in these submerged applications. Since installing the new bearings, they have been operating efficiently 24 hours a day and 365 days a year, without maintenance or disruption.
Find the engineered solutions you can depend upon for your unique requirements at Millstream Engineering. Let us upgrade your mechanical equipment so you can save costs and reduce downtime. Contact us today at contact@millstreamengineering.com or call 705.413.0933 for more information.