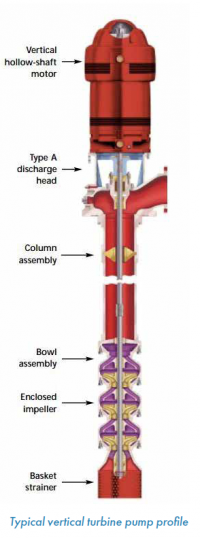
Understanding Vertical Turbine Pump Bearing Failure Modes: Abrasive Wear and Dry Starts
Vertical turbine pumps (VTPs) play a crucial role in pumping water across various applications, including flood control and water supply. To ensure optimal performance and longevity, it is essential to understand the common causes of bearing failure in these pumps. In this blog post, we will delve into the two primary failure modes- abrasive wear and dry starts – and discuss the strategies pump manufacturers employ to mitigate these issues.
Abrasive Wear: A Growing Concern
One of the leading causes of bearing failure in VTPs is abrasive wear. As pumps draw water containing sand, grit, or other suspended particles, these particulates can erode the bearing’s inner diameter and the shaft’s outer diameter, causing significant damage. With the growing global population and rising ocean levels, pumps increasingly handle water with high abrasive content, especially in flood control applications.
To combat abrasive wear, pump manufacturers have developed two primary strategies:
a. Enclosing Tubes: Enclosing tubes isolate the bearing and shaft from the abrasive process water, lubricating them with oil. This method effectively protects the components from wear but comes with the drawback of increased costs.
b. Upgraded Materials: Another approach involves using harder shaft materials and softer bearings, such as rubber, which handle abrasives better. However, this solution presents its own challenges, as rubber bearings can burn up during dry starts due to frictional heat generated with little to no lubrication.
Dry Starts: A Necessary Evil
In many applications, VTPs must start before the presence of water, a process known as a dry start. The extended dry running period can be problematic for materials like bronze, rubber, and most phenolic bearings, which struggle with running dry due to their low friction properties. To address the challenges posed by dry starts, pump manufacturers have implemented the following solutions:
a. Oil Lubrication: Using oil lubrication can provide adequate lubrication to the bearings until process water flows. However, this solution increases operational costs and risks contaminating the process water with oil.
b. Water Flush Systems: Water flush systems can be used to lubricate the bearings until the process water reaches them. While effective, these systems also add additional costs to the pump operation.
Understanding the primary bearing failure modes in vertical turbine pumps is crucial for maintaining their efficiency and longevity. By being aware of the challenges posed by abrasive wear and dry starts, you can better select bearings for your specific VTP applications. Although manufacturers have devised strategies to address these issues, it is essential to weigh the benefits and drawbacks of each solution carefully to ensure optimal performance and minimal downtime.
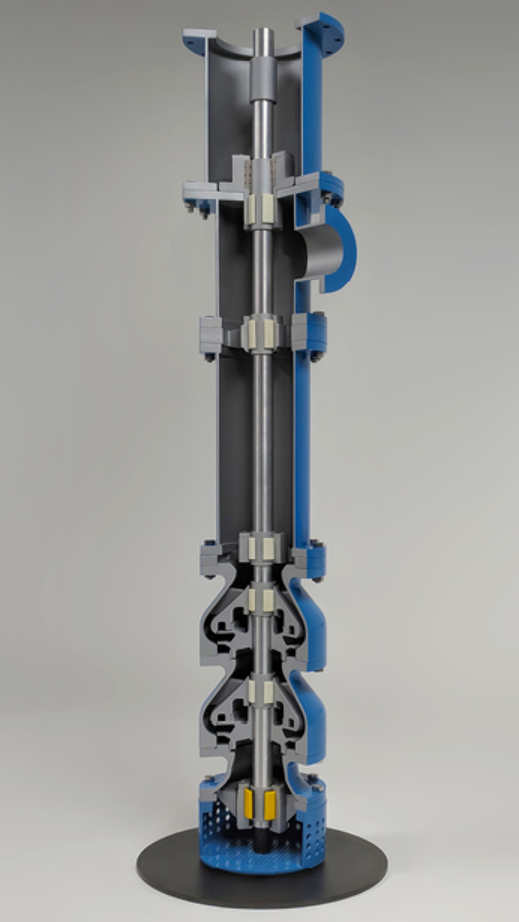
Do you have expensive challenges with your bearings and need a creative, cost-effective solution? Allow Millstream Engineering’s team of specialists to lead your group to a successful, economical solution. Contact us today.