Why Bushings Fail
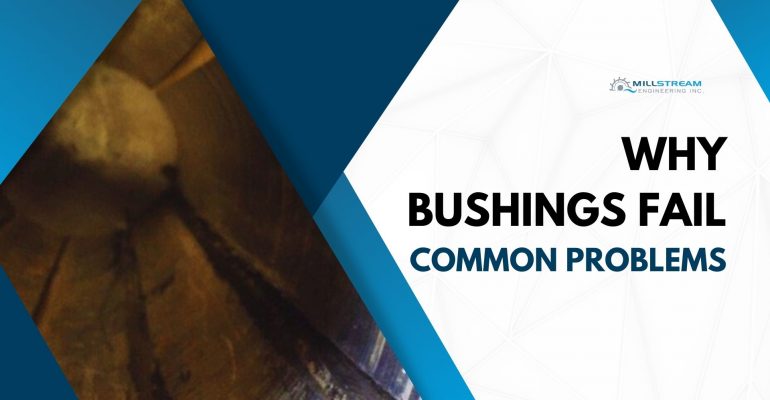
Why Bushings Fail: Common Problems and Smarter Material Choices
Bushings are vital components in industrial machinery, providing support and reducing friction between moving parts. Despite their critical role, bushings are often overlooked until failure occurs, leading to costly downtime and repairs. In this blog, we’ll explore the most common causes of bushing wear and how to prevent them to keep your equipment running efficiently.
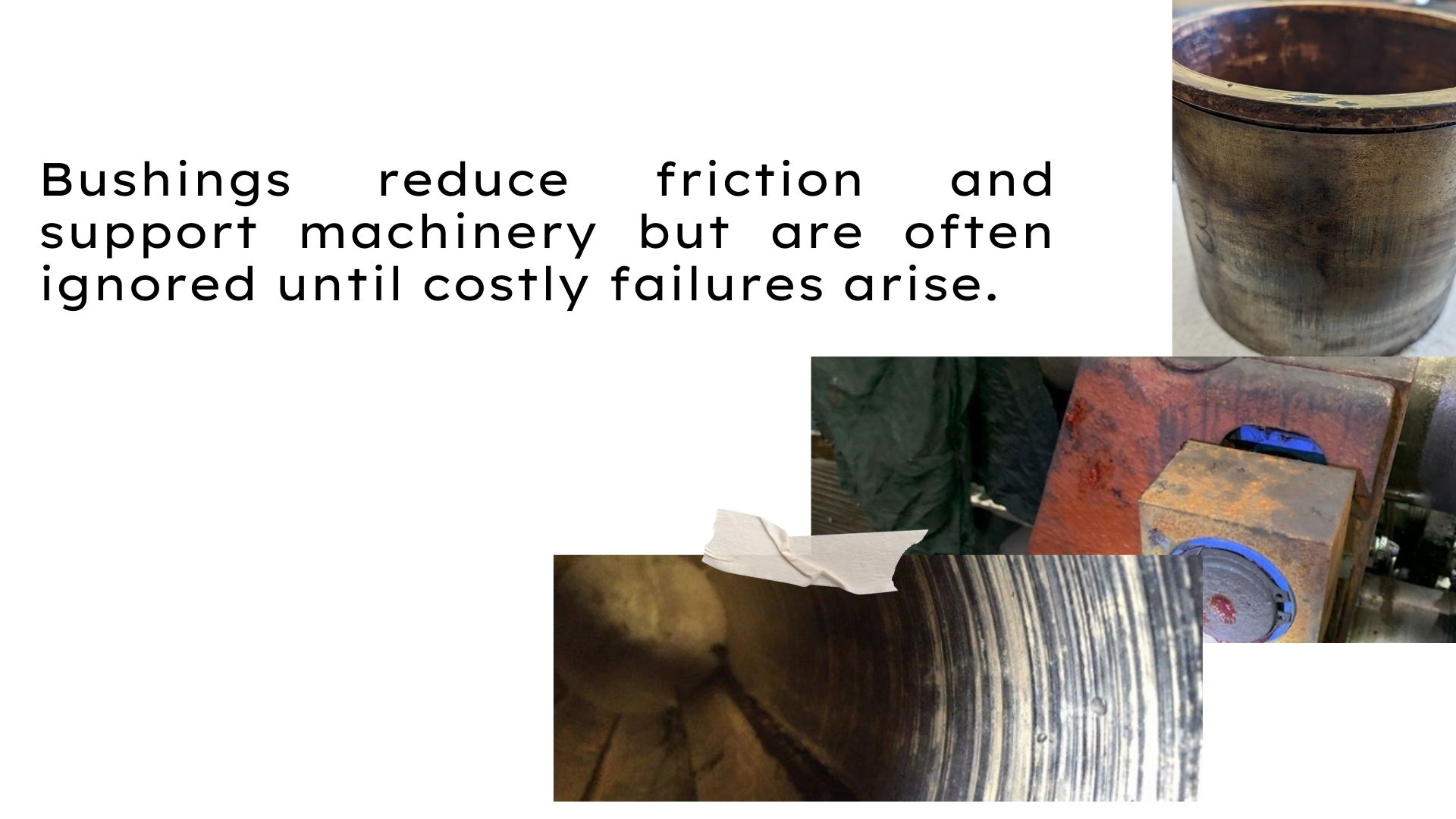
1. Improper Material Selection
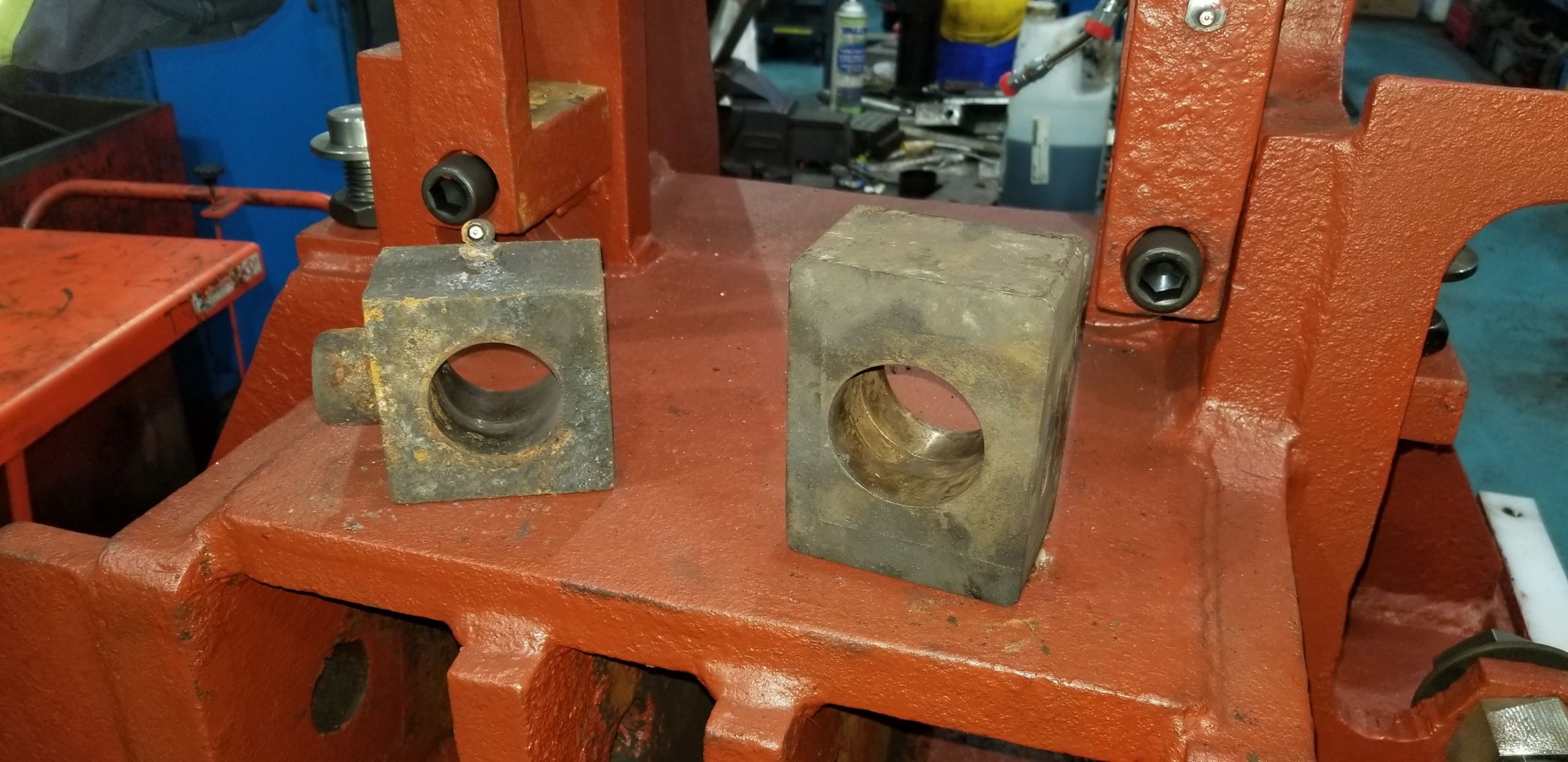
One of the primary reasons bushings fail is using materials that aren’t suited for the operating environment. Conventional materials like grease-lubricated bronze may not withstand harsh conditions such as high loads, extreme temperatures, or exposure to chemicals. Similarly, some common non-metallic bushing materials like nylon and UHMWPE have significant limitations. For example:
- Nylon: Susceptible to moisture absorption, which can cause swelling and dimensional instability.
- UHMWPE: Lacks the strength and dimensional stability required for high-load or high-temperature applications.
How to Prevent It: Choosing advanced materials like Thordon SXL or ThorPlas-Blue ensures superior performance. These high-performance polymers are engineered for demanding applications, offering excellent wear resistance, self-lubrication, and the ability to operate in extreme conditions. Consulting with experts can help evaluate your application and recommend the ideal material for long-lasting results.
2. Insufficient or Incorrect Lubrication
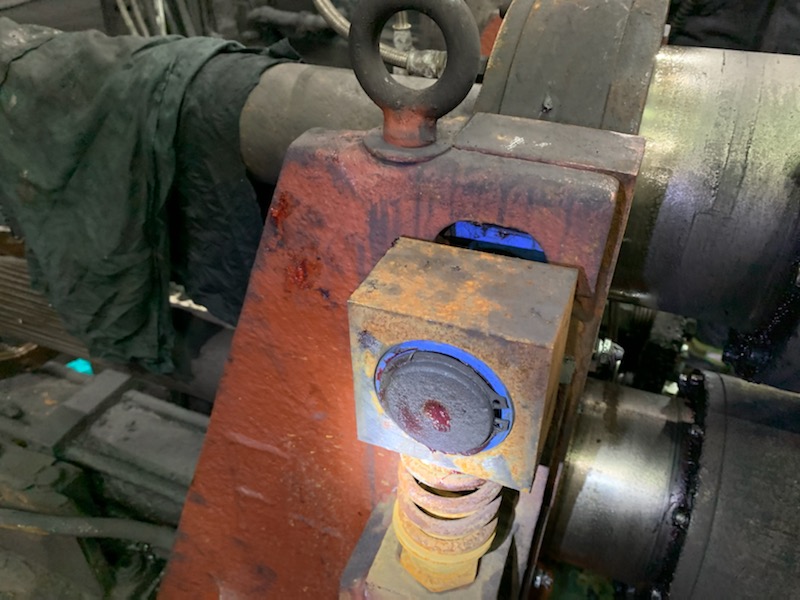
Friction and heat buildup are common issues when bushings are not properly lubricated. Traditional grease-lubricated bronze bushings rely on regular maintenance and missed lubrication cycles can lead to premature wear.
How to Prevent It: Self-lubricated materials like Thordon SXL and ThorPlas-Blue eliminate the need for external lubrication, reducing maintenance requirements and ensuring consistent performance. These advanced solutions can save time, minimize operational disruptions, and extend the life of your bushings.
3. Contamination
Dust, dirt, and other contaminants can infiltrate the system, acting as abrasive particles that accelerate bushing wear. This is especially problematic in environments with heavy industrial activity.
How to Prevent It: Sealed systems and regular cleaning can help mitigate contamination risks. Additionally, Thordon SXL and ThorPlas-Blue materials are designed to perform in contaminated environments, providing enhanced durability and reducing the impact of abrasive particles.
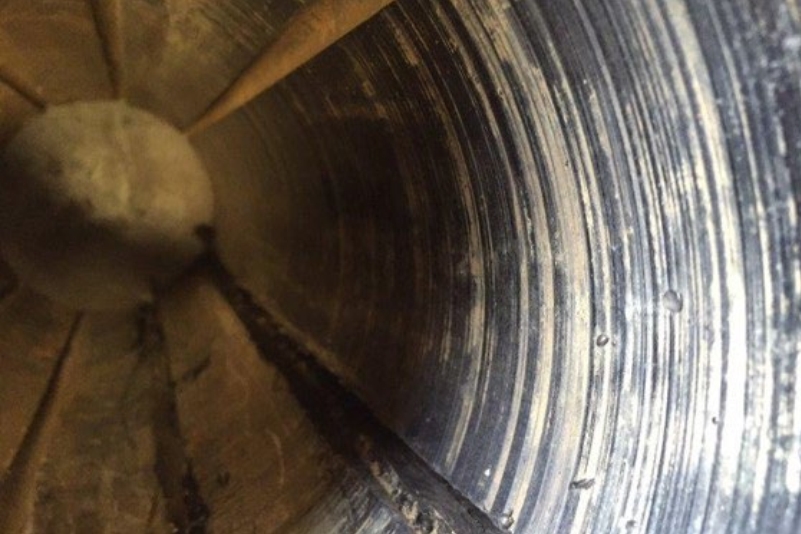
4. Overloading
Bushings are designed to handle specific loads. Exceeding these limits can cause deformation or excessive wear, leading to premature failure.
How to Prevent It: Selecting bushings rated for higher load capacities is essential. Thordon SXL and ThorPlas-Blue offer exceptional load-bearing capabilities and are tailored for high-stress applications. Millstream Engineering’s expertise ensures you’ll get the right solution for your equipment.
5. Misalignment or Poor Installation
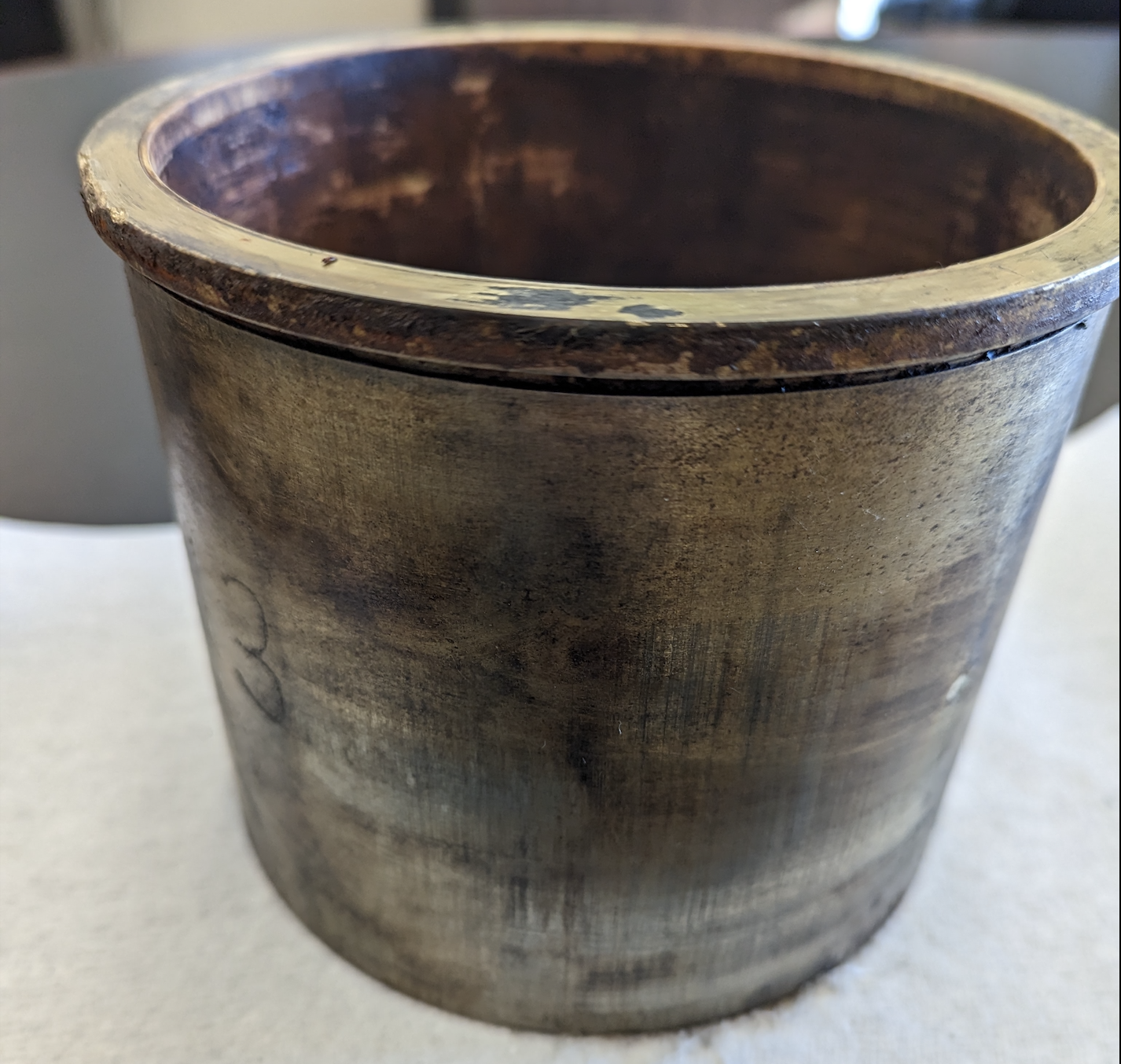
Even the best bushing materials can fail if components are misaligned or improperly installed. Uneven wear patterns and early failure are common consequences.
How to Prevent It: Proper installation and alignment are crucial. Proper guidance on installation practices, along with customized solutions like Thordon SXL and ThorPlas-Blue bushings, can help address minor misalignments effectively.
Bonus Tip: Recognizing Early Warning Signs
Detecting early signs of wear—such as unusual noises, increased friction, or visible damage—can prevent catastrophic failures. Regular inspections and proactive maintenance are key to ensuring optimal performance.
Why Choose Thordon SXL and ThorPlas-Blue?
Thordon SXL and ThorPlas-Blue self-lubricating polymers are designed to outperform conventional grease-lubricated bronze bushings and common non-metallic options like nylon and UHMWPE. These materials offer:
- Reduced Maintenance: No need for external lubrication.
- Extended Lifespan: Superior wear resistance in extreme environments.
- Environmentally Friendly: Elimination of grease reduces environmental contamination.
- Enhanced Performance: Outstanding durability and low friction for smoother operation.
Understanding the common reasons for bushing wear is the first step in preventing equipment failures and costly downtime. By selecting the right materials and partnering with industry experts, you can ensure your bushings operate reliably even in the toughest conditions.
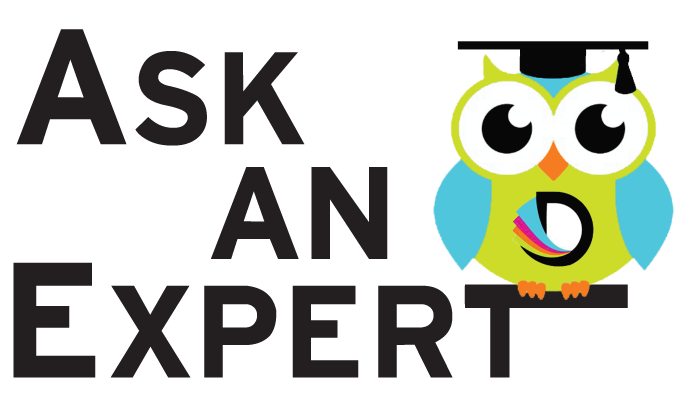
Let us help you transition to advanced solutions like Thordon SXL and ThorPlas-Blue and optimize your equipment for long-term success. Reach out to learn more about tailored solutions and expert advice for your specific needs